В. Круммхойер (ФРГ)
Шестидесятые годы были периодом бурного расцвета пневматических и, в частности, воздухоопорных конструкций во многих промышленно развитых странах. В течение последующего десятилетия в использовании этих конструкций наступил некоторый застой, вызванный главным образом резким ростом стоимости энергии, что во многих случаях сделало неприемлемым применение пневматических конструкций для отапливаемых зданий. Тем не менее эти конструкции по-прежнему остаются объектом повышенного интереса со стороны архитекторов и экономистов.
Как показал опыт, определенные трудности в развитии конструкций были связаны также с недостаточно полным представлением о свойствах материалов пневматических оболочек. Вследствие этого материалы в конструкциях иногда использовались неэффективно [1] или к ним предъявлялись явно преувеличенные требования со стороны заказчиков, что иногда давало повод для негативной оценки пневматических конструкций вообще.
За последние годы накоплены данные, полученные на основе обширных испытаний материалов, которые позволяют в будущем избежать подобных неудач. В настоящей статье предпринимается попытка систематизировать эти данные и оценить их значение для решения практических задач проектирования пневматических конструкций.
Материалы
Если не считать пневматических конструкций небольшого размера, которые в ряде случаев могут быть выполнены из неармированных полимерных пленок, общим направлением в создании воздухоопорных оболочек является применение текстильных материалов (подложка) с покрытиями из эластомеров или термопластов [2]. Более ранние опыты по использованию неармированных пленок в сочетании с крупноячеистыми сетками из высокопрочных нитей не дали положительных результатов.
В качестве подложек применяют обычно технические ткани, тканые сетки (только при невысоких требованиях к прочности материала), ткани типа «малимо» и материалы с трикотажной основой.
Эти материалы могут быть изготовлены из промышленных синтетических волокон — полиэфирных, полиамидных, поливинилспиртовых, из стекловолокна, из волокна «арамид» и т. п.
Для покрытий наибольшее распространение получили: из термопластов — пластифицированный поливинилхлорид (ПВХ), а в последнее время также политетрафторэтилен, из эластомеров — полихлоропрен.
В Западной Европе наиболее широко применяются ткани из полиэфирного волокна с покрытием из ПВХ; в Северной Америке, кроме того, используют ткани из полиамидного волокна с покрытием из полихлоропрена и стеклоткани с покрытием из политетрафторэтилена. В Японии применяют также ткани из поливинилспиртового волокна с покрытием из ПВХ. Наконец, в Восточной Европе отдают предпочтение высокопрочным тканям типа «малимо» из полиамидного волокна с покрытием из ПВХ.
Все эти материалы имеют свои достоинства и недостатки. Наиболее подробно описаны в литературе ткани из полиэфирного волокна с покрытием из ПВХ, с тех пор как они в силу причин экономического и технического характера заняли доминирующее положение в Западной Европе. Этим материалам посвящена в основном и настоящая статья.
При необходимости оценки механических свойств материалов оболочек приведенные ниже результаты могут быть во многих случаях распространены на ткани из полиэфирных волокон с другими видами покрытий (в том числе на тканр типа «малимо» или материалы с трикотажной основой). Это, однако, не касается прочности швов оболочек, поскольку она зависит не только от адгезии покрытия к подложке, но и от вида самого покрытия и его стойкости к воздействиям среды.
В тех случаях, когда не представляется возможным прямо использовать приведенные результаты испытаний, следует руководствоваться изложенным в статье общим подходом к учету свойств материала при расчете оболочек.
Свойства тканей с покрытием из ПВХ
Свойства этих материалов зависят как от самой ткани, так и от вида ее покрытия. Если механические свойства материала оболочки (кратковременные и длительные) являются по существу характеристиками ткани, то его долговечность определяется главным образом химической природой покрытия. Существует, кроме того, еще ряд важных свойств, в равной степени зависящих от обоих компонентов материала.
Механические характеристики
Кратковременн нехарактеристики. Прочность и растяжимость ткани с покрытием являются прежде всего функцией характеристики «усилие — удлинение» отдельных нитей. На рис. 1 показан пример такой характеристики для нитей из полиэфирного волокна. Аналогичной в общем зависимостью между напряжениями и деформациями характеризуется и ткань из таких нитей. Как видно из рис. 2, несмотря на одинаковую плотность нитей основы и утка, характеристики ткани в двух взаимно перпендикулярных направлениях различны. Это различие вызвано различной степенью искривления нитей основы и утка в системе переплетения ткани в связи с их неодинаковым натяжением как в ткацком процессе, так и в процессе нанесения покрытия. Таким образом, обработанная ткань характеризуется различием удлинений и модулей упругости в направлениях основы и утка.
Те же технологические причины обусловливают и анизотропию прочности ткани: уточные нити при растяжении испытывают более значительные поперечные усилия, что несколько снижает их эффективную прочность по сравнению с нитями основы. Эти различия в прочности иллюстрирует табл. 1, в которой приведены характеристики стандартных тканей четырех типов, применяемых сейчас в Западной Европе [3]. В таблицу включены показатели прочности тканей при температуре 70°С с учетом возможного в условиях эксплуатации нагрева оболочек вследствие солнечной радиации. Температура 70°С принята как максимально возможная по данным натурных измерений в умеренных климатических условиях Центральной Европы; для географических районов с более интенсивной тепловой солнечной радиацией может оказаться необходимым учет и более высоких температур. Как видно из табл. 1, при температуре 70°С прочность тканей снижается примерно на 10% по сравнению с их прочностью при комнатной температуре.
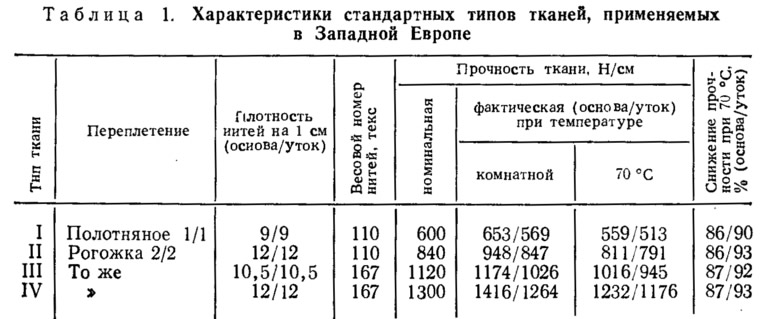
Кроме прочности самой ткани, важное значение имеет прочность ее соединений (швов) [3]. Прочность шва зависит в первую очередь от его геометрии. На рис. 3 показаны типы швов, применяемых в ФРГ для оболочек из тканей типов II и III (см. табл. 1). В табл. 2 приведены характеристики прочности этих швов (в абсолютных и относительных единицах) при комнатной температуре и при 70°С; в некоторых случаях при более высокой температуре наблюдается заметное снижение прочности.
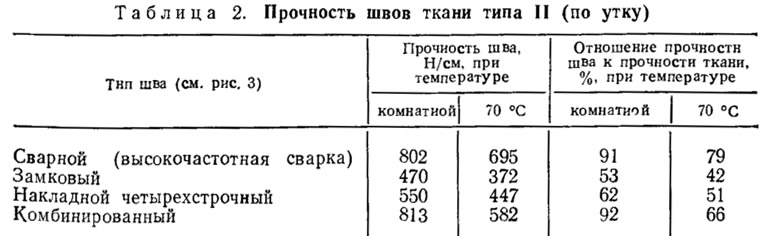
К показателям, требующим особого внимания при расчете и проектировании воздухоопорных конструкций, относится прочность соединений оболочки с анкерными устройствами. Она зависит не только от прочности ткани, но и от геометрии соединений и швов, которая может быть весьма разнообразной, в связи с чем в настоящей статье этот вопрос не рассматривается. В ФРГ применяют обычно стандартные типы таких соединений [4].
Поскольку в пневматических конструкциях материал оболочки подвергается, вообще говоря, двухосному растяжению, решающее значение имеет характеристика материала при таком напряженном состоянии. Соответствующие исследования проводили многие авторы [5—9J; особый интерес представляют результаты испытаний цилиндрических (трубчатых) образцов, выполненных Б. Меффертом [6, 7]. Им установлено, что при двухосном деформировании ткани разрывные усилия и удлинения при разрыве уменьшаются по сравнению с одноосным растяжением, а кривая «усилие—удлинение» имеет более крутой наклон (рис. 4). На рис. 5 показана зависимость разрывной прочности ткани по основе и утку от соотношения соответствующих усилий; снижение прочности по сравнению с одноосным растяжением составляет около 20%, независимо от нагрузки.
Кроме разрывной прочности и удлинения при разрыве — характеристик, непосредственно используемых в расчете, — существует еще ряд механических свойств, играющих важную роль для оценки качества композиционных материалов оболочек. В первую очередь к ним относятся прочность при раздире и прочность сцепления покрытия с подложкой [10]. Важность этих показателей для практического применения тканей очевидна: прочность сцепления является фактором, определяющим прочность швов оболочки, а прочность при раздире характеризует сопротивляемость ткани распространению локальных повреждений. На рис. 6 и 7 показаны схемы испытания образцов ткани для определения прочности сцепления покрытия с подложкой и прочности при раздире.
Как видно из рис. 7, существует несколько различных методов испытания образцов тканей на раздир: в Англии применяют метод «язычка» (рис. 7, а), в Австрии, Бельгии, Нидерландах, Италии, Финляндии и Скандинавских странах —метод «лапки» (рис. 7, б), во Франции и Швейцарии — «маятниковый» метод (рис. 7, в), в ФРГ — метод «лапки», а также метод «трапеции» (рис. 7, г). Методы «лапки», «язычка» и «маятниковый» основаны на одном и том же принципе: усилия прикладываются перпендикулярно к нитям ткани, прочность которых определяется; различие состоит лишь в том, что в методе «язычка» раздир ткани производится по двум симметрично расположенным линиям, а в «маятниковом» методе — при большой скорости перемещения захвата. В отличие от этих методов при испытании по методу «трапеции» нити, прочность которых оценивается, располагаются параллельно направлению раздирающего усилия. Сравнительными испытаниями [10] было установлено, что корреляции между значениями прочности ткани при раздире, полученными при использовании указанных двух принципиально различных методов, отсутствует.
Для практических целей можно рекомендовать применение метода «трапеции», в сочетании с одним из трех других методов, например с методом «лапки». Хотя испытание по методу «трапеции» и более точно воспроизводит характер локального разрушения оболочки, качественное различие между разрывной прочностью ткани и ее сопротивлением «раздиру» не обнаруживается при этом испытании так четко, как, например, при использовании метода «лапки» [10, 11]. Кроме перечисленных выше стандартных методов определения прочности тканей при раздире, следует отметить еще ряд способов, имеющих целью обеспечить лучшее соответствие условий испытания действительному напряженному состоянию материала в пневматических оболочках [12, 13].
На рис. 8 и 9 показана зависимость прочности швов различных типов от прочности сцепления покрытия из ПВХ с подложкой; как видно из графиков, максимальная прочность швов достигается при прочности сцепления около 130 Н/5 см. Дать подобную оценку требуемого уровня прочности ткани при раздире не представляется возможным; по-видимому, эти характеристики вообще нельзя прямо использовать в статических расчетах. Единственное, что можно рекомендовать,-—это устанавливать для тканей, применяемых в оболочках, возможно более высокие требования по их сопротивлению раздиру.
Длительные характеристики. Весьма важное значение имеет сопротивление материала оболочки и ее швов длительно действующим нагрузкам, поскольку на практике пневматические оболочки чаще используются для стационарных сооружений, нежели для временных. При этом наиболее важной характеристикой является длительная прочность материала или прочность при разрушении в условиях ползучести. Для определения этой характеристики образцы материала подвергают без перерывов действию постоянных по величине нагрузок до тех пор, пока образцы не разрушатся, и фиксируют время до разрушения. Чтобы это время было не слишком велико, нагрузки должны быть достаточно высокими; их следует, как правило, принимать с таким расчетом, чтобы в течение первых 1000 ч испытания разрушилось не менее 10 образцов. Откладывая значения нагрузок и соответствующего им времени до разрушения образцов на графике в двойных логарифмических координатах, получают так называемую кривую разрушения в условиях ползучести; на рис. 10 показан пример такой кривой для ткани типа II. Существует примерно линейная зависимость между логарифмами нагрузки и времени до разрушения образца. Используя эту зависимость, можно с достаточной точностью экстраполировать результаты испытаний на время до 105 ч (около 11 лет) и таким образом определить нагрузку, не вызывающую разрушения материала в течение этого срока. Аналогичные зависимости получены и при испытании швов оболочек, что видно из рис. 11, относящегося к комбинированному шву для ткани типа II, Если при таких испытаниях определять удлинения ткани в момент разрушения, то обнаруживается, что их значения весьма близки к значениям кратковременных удлинений при разрыве и, по-видимому, не зависят от времени [7].
Длительные испытания материалов и швов необходимо проводить, естественно, не только при комнатной, но и при повышенной температуре. Поэтому полная программа испытаний (для четырех типов тканей и четырех типов швов), результаты которых здесь приводятся, оказалась весьма обширной и потребовала значительного времени для ее реализации.
В табл. 3 приведены экстраполированные до 105 ч характеристики длительной прочности тканей типов II и III и стандартных швов для этих тканей при комнатной температуре и при температуре 70°С [14, 15]. Там же приведены значения отношений длительной прочности к кратковременной, а также обратные им величины — «коэффициенты потерь», необходимые для расчета оболочек на прочность.
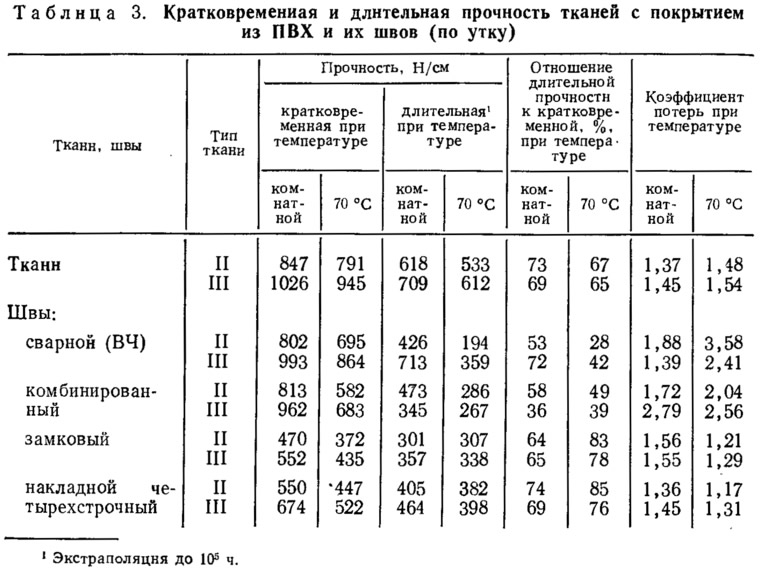
Анализ результатов испытаний при температуре 70°С показывает, что длительная прочность материала при этой температуре практически равна кратковременной прочности при комнатной температуре, умноженной на произведение понижающих коэффициентов, соответствующих длительной прочности при комнатной температуре и кратковременной прочности при 70°С. Наличие такой закономерности позволяет отказаться от проведения длительных испытаний материала при повышенных температурах.
Кроме прочности при разрушении в условиях ползучести, важное значение могут иметь и другие характеристики ползучести материала. На рис. 12 показаны деформации ползучести ткани при длительной нагрузке. Как видно из рисунка, кривые ползучести в полулогарифмических координатах принимают постоянный положительный наклон сразу после достижения некоторого начального удлинения, причем этот наклон не зависит от нагрузки [16].
Испытания при повышенных температурах не обнаружили существенного увеличения скорости ползучести [7, 17]. Те же вязко-упругие свойства материала проявляются и при «обратных» условиях испытания, т. е. при заданном постоянном удлинении; в этом случае усилия (напряжения) в материале уменьшаются со временем, как показано на рис. 13, где приведены результаты испытаний при циклическом изменении температуры. Это явление релаксации напряжений означает с практической точки зрения необходимость «подтягивать» оболочку спустя некоторое время после ее возведения (примерно через сутки), чтобы восстановить первоначальный уровень натяжения, обеспечивающий стабильность конструкции1. Если на сооружение действуют повышенные температуры, может оказаться необходимым повторно «подтянуть» оболочку после первого интенсивного теплового воздействия. В дальнейшем дополнительной корректировки натяжения оболочки уже не требуется.
В реальных условиях эксплуатации усилия в оболочке никогда не остаются постоянными, в связи с чем возникает вопрос о том, как будет реагировать материал оболочки на переменные (повторные) нагрузки. Здесь могут быть рассмотрены два крайних случая: высокочастотная циклическая нагрузка, вызываемая сильными ветрами, и низкочастотная (длиннопериодная) нагрузка от снега. Оба вида воздействий подробно исследованы [7, 17, 18], причем было установлено, что длительная прочность и деформативность материала существенным образом зависят от верхнего уровня нагрузки, так что для надежной оценки этих характеристик можно использовать результаты испытаний материала при постоянном напряжении, соответствующем верхнему уровню действующих нагрузок.
Долговечность. Решающим фактором при решении практических задач является, конечно, устойчивость материалов оболочек к воздействиям среды, характерным для района строительства. Поскольку эти воздействия весьма широко изменяются для разных географических зон и их крайне трудно воспроизвести в лабораторном эксперименте, были своевременно организованы испытания материалов непосредственно в натурных условиях. Вначале такие испытания проводились только в Вуппертале (ФРГ); затем они были поставлены в Дормелетто (Италия), Эбните (Австрия), Тель-Авиве (Израиль) и Майами (США) [19, 20]. Результаты испытаний, представленные в обобщенном виде на рис. 14, показывают, что долговечность тканей существенным образом зависит от толщины покрытия в местах выступов переплетения нитей. Можно с уверенностью считать, что в этих местах толщина покрытия на экспонируемой (наружной) поверхности ткани должна быть не менее 150 мкм; при этом потеря прочности ткани не будет превышать примерно 10%.
Теплофизические характеристики. Как уже было отмечено, в связи с чрезвычайно быстрым ростом стоимости энергии теплоизоляционные свойства материалов оболочек приобрели роль важнейшего фактора при применении воздухоопорных конструкций для зданий, требующих отопления и кондиционирования воздуха. Теплоизоляционные свойства ограждающих конструкций характеризуются коэффициентом теплопередачи К [21], показывающим, какое количество тепловой энергии передается в единицу времени через заданную площадь поверхности ограждения. Для тканей с покрытием из ПВХ значение К составляет 5,7 Вт/(м2·К) [22], что намного превышает соответствующие значения для традиционных строительных материалов. Столь значительная теплопроводность тканевых материалов является, если не принять специальных мер, серьезным препятствием для их использования в оболочках плавательных бассейнов, выставочных павильонов и т. п. Менее существенны теплоизоляционные свойства материалов оболочек для таких сооружений, как, например, склады разного рода продукции, нечувствительной к температурному режиму хранения.
Существует ряд способов улучшения теплотехнических свойств пневматических оболочек, например нанесение на ткань вспененного теплоизоляционного материала [22] или устройство многослойных оболочек [23]. Общие критерии для оценки эффективности таких способов отсутствуют, и вопрос об их использовании должен решаться по существу в каждом конкретном случае.
Огнестойкость. Как и для других полимерных материалов, для тканей с покрытием из ПВХ горючесть является важной характеристикой при их применении в строительстве. В отличие от аналогичных импрегнированных тканей общетехнического назначения, ткани с покрытием из ПВХ для строительных конструкций выпускают со специальными пламегасящими добавками и, таким образом, удовлетворяют требованию трудносгораемости, содержащемуся в нормах ряда стран [24, 25]. В качестве таких добавок используют вводимые в массу покрытия соединения типа диоксида сурьмы или специальные фосфорсодержащие пластификаторы. Вид материала подложки играет лишь второстепенную роль [22]; например, стеклоткань с покрытием из ПВХ не обладает существенно более низкой степенью горючести по сравнению с тканями из синтетических волокон. Дополнительная огнезащитная обработка материала в большинстве случаев вообще не является необходимой, поскольку по действующим противопожарным нормам требуется лишь, чтобы повреждение материала при пожаре ограничивалось зоной непосредственного воздействия огня и горение не распространялось по материалу оболочки за пределы этой зоны. В тех особых случаях, когда требуется полностью исключить любую возможность возгорания оболочки, может оказаться необходимым применение других материалов, например стеклотканей, покрытых политетрафторэтиленом.
Стойкость к загрязнению. Как показали испытания в различных климатических зонах [20], все материалы оболочек подвержены более или менее значительному загрязнению. В воздухоопорных конструкциях такое загрязнение наблюдается уже после относительно короткого срока эксплуатации, поскольку вследствие миграции пластификатора из массы покрытия его наружная поверхность становится липкой. При этом такое широко применяемое средство, как покрытие материала оболочки лаками, оказывается малоэффективным; некоторую защиту от загрязнения обеспечивает только нанесение поверхностного покрытия из поливинилфторида [22]. Следует, однако, иметь в виду, что нанесение на материал оболочки любых дополнительных покрытий значительно затрудняет все операции с ним, делает невозможной сварку швов и, таким образом, допускает устройство только шитых соединений.
В редких случаях, в частности в условиях влажного климата, на поверхности оболочек может наблюдаться появление плесени, что также связано с присутствием пластификаторов, даже если в массу ПВХ введена добавка фунгицида.
Как загрязнение, так и образование плесени практически не влияют на эксплуатационные свойства оболочек и сказываются лишь на их внешнем виде, что, впрочем, может быть весьма нежелательным для сооружений, рассчитанных на определенный архитектурный эффект.
Учет свойств материала при расчете оболочек
Рассмотрев свойства импрегнированных материалов для мягких оболочек, перейдем к использованию полученных выше результатов в расчетах пневматических (воздухоопорных) конструкций.
В ранних работах по данному вопросу [3, 7] устанавливался максимальный уровень натяжения оболочки σа, превышение которого не допускалось ни при каких обстоятельствах:
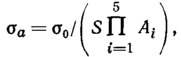
где σ0 — кратковременная разрывная прочность материала; S — коэффициент безопасности; Ai — «коэффициенты потерь», учитывающие снижение прочности материала вследствие длительного действия нагрузки (A1), двухосного напряженного состояния (A2), повышенных температур (A3) и факторов, вызывающих старение материала (A4), а также изменчивость условий обработки материала и изготовления оболочек (A5).
Впоследствии было найдено, что такой подход является слишком грубым, так как основывается на предположении, что конструкция в течение всего времени эксплуатации подвергается действию максимального ветрового давления и повышенной температуры. Поэтому был предложен метод расчета, позволяющий более корректно учитывать реальный режим эксплуатации конструкций [4] и устанавливающий следующие предельные условия для трех основных сочетаний нагрузок (воздействий).
1. Усилия при нормальной температуре, вызываемые номинальным внутренним давлением в оболочке и ветровой нагрузкой:

где σpi — натяжение оболочки от внутреннего давления; σw — то же, от ветра; σa0 — максимально допускаемое натяжение материала, определяемое с учетом коэффициентов A2 и A4.
2. Усилия при максимальной температуре, вызываемые номинальным внутренним давлением и ветровой нагрузкой:

где σaT — допускаемое натяжение материала, определяемое с учетом коэффициентов A2, A3 и A4.
3. Длительно действующие усилия:

где σat — допускаемое натяжение материала, определяемое с учетом коэффициентов A1, A2, A3 и A4.
Коэффициенты в левой части предельных условий установлены исходя из требований надежности [26], на основании статистического анализа метеорологических данных, а также с учетом неизбежной изменчивости условий обработки материала и изготовления конструкций. Поэтому указанные условия уже не содержат коэффициента A5, который ранее учитывался в расчетах.
При решении практических задач расчета следует обеспечивать одновременное выполнение всех трех приведенных выше предельных условий. Значения σpi и σw определяются из статического расчета оболочки, а значения σa0, σaT и σat могут быть приняты по официальным нормативным документам, регламентирующим характеристики материалов для пневматических конструкций и разработанным на основе испытаний, подобных описанным в разделе «Свойства тканей с покрытием из ПВХ». Значения допускаемых напряжений для материалов типа I и II (см. табл. 1) и для различных типов швов оболочек из этих материалов приведены в табл. 4.
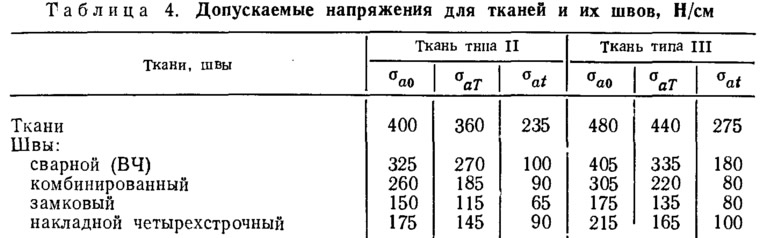
Заключение
Хотя применение методики расчета, изложенной выше, должно было бы гарантировать полную надежность воздухоопорных конструкций, на практике все же наблюдаются повторяющиеся случаи их разрушения. Анализ разрушений [10] показывает, что более чем в 80% всех случаев они не являются прямым следствием разрушения материала оболочек, а связаны с такими факторами, как неудовлетворительное обслуживание, несоблюдение установленных нормами расстояний между сооружениями и т. д. При этом оболочки, как правило, разрушаются полностью — свидетельство того, что их сопротивление раздиру недостаточно для локализации местных повреждений. Ситуация осложняется еще и тем, что сопротивление раздиру тканей с покрытием из ПВХ существенно снижается при низких температурах [10, 27, 28]; это снижение вызывается высоким содержанием пластификаторов в массе покрытия. Рекламируемые на рынке так называемые «морозостойкие» покрытия из ПВХ неэффективны и, более того, вообще не должны применяться в связи с их низкой огнестойкостью. Сопротивление тканей раздиру может быть повышено при использовании специальной технологии их изготовления, например путем введения в полиэфирную ткань волокна «арамид». При этом повышение прочности при раздире доходит до 50%, однако чувствительность материала к низким температурам сохраняется, хотя и в несколько меньшей степени. Радикальным решением проблемы было бы применение материалов покрытий, вообще не содержащих пластификаторов, но принадлежащих, подобно ПВХ, к классу термопластов, так как только тогда материал оболочки будет так же легко перерабатываться. Некоторые обнадеживающие шаги в этом направлении уже сделаны [29, 30]. Можно рассчитывать, что применение новых покрытий позволит одновременно решить и проблему предотвращения загрязнений оболочек.
Подводя итог сказанному, выразим надежду, что уже в ближайшем будущем мы будем иметь новые материалы для покрытий, свободные от недостатков, свойственных покрытиям из ПВХ из-за высокого содержания в них пластификаторов, но в той же степени удобные и экономичные в переработке. При этом можно ожидать удорожания материала примерно на 20%; однако, если учесть одновременное повышение его качества и относительно малую долю стоимости материалов оболочек в общей стоимости сооружений, такое удорожание наверняка окажется не слишком обременительным.
Список литературы
- 1. J. Schlaich, К. Kleinhanss, К. Gabriel.— Symp. «Beschichtete Chemiefaser-gewebe 1979», Institut fiir Kunststoffverarbeitung, RWTH Aachen, F. R Germany, p. 2.1.
- 2. H. Mewes. Producing and Properties of Coated Fabrics for Pneumatic Structures. Research Report IASS — Working Group of Pneumatic Structures 1978, p. 19.
- 3. W. Krummheuer. Mechanical Properties of PVC—Coated Fabrics and their Joints Journal of Coated Fabrics 8 (1979) 302.
- 4. Zulassungsbescheid Z-10.5-27 des Institutes fiir Bautechnik, Berlin, vom 3. Sept. 1979 fiir «PVC—beschichtete Polyestergewebe fiir Traglufthallenbauten».
- 5. М. H. Losch. Bestimmung der mechanischer. Konstanten fur einen zweidi-mensionalen nicht linearen, anisotropen elastischen Stoff am Beispiel beschichteter Gewebe. Diss. Universitat Stuttgart, F. R. Germany (1971).
- 6. B. Meffert. Verhalten von PVC—beschichteten Textil—Geweben. Spannungs-, Deformations- und Versagensverhalten PVC—beschichteter Polyestergewebe unter einachsiger und biaxialer Beanspruchung. 1. Intern. Symp. «Weitgespannte leichte Flachentragwerke». Stuttgart, F. R. Germany, April 1976, Vol. 2.
- 7. B. Meffert. Mechanische Eigenschaften PVC—beschichteter Polyestergewebe. Diss., RWTH Aachen, F. R. Germany, 1978.
- 8. G. Rehm, R. Miinsch. Zweiachsige Langzeit-Zugversuche an PVC-beschich-teten Polyestergeweben. 2. Intern. g'ymp. «Weitgespannte leichte Flachentragwerke», Stuttgrat, F. R. Germany, May 1979, Vol. 1.
- 9. H. W. Reinhard. Zweiachsige Priifungen an textilen Geweben mit beson-derer Beriicksichtigung von Zeitenfliissen auf das mechanische Verhalten. 1. Intern. Symp. «Weitgespannte leichte Flachentragwerke», Stuttgart, F. R. Germany, April 1976, Vol. 2.
- 10. W. Krummheuer. Haft- und Weiterreififestigkeit bei PVC — beschichteten Polyestergeweben. Symp. «Beschichtete Chemiefasergewebe 1979». Institut fiir Kunststoffverarbeitung RWTH Aachen, p. 5.1.
- 11. H. Blumberg. Eurofabric 1979, edited by: Enka AG, Wuppertal, F. R. Germany.
- 12. B. Meffert. Festigkeits- und WeiterreiBfestigkeitsprobleme bei beschichteten Geweben. 2. Intern. Symp. «Weitgespannte leichte Flachentragwerke». Stuttgart, F. R. Germany, 1979, Vol. 2.
- 13. H. Minaml. Strength of Coated Fabrics with Crack Technical R & D Dept. Report edited by: Taiyo Kogyo Co., Ltd., Tokyo and Osaka, Japan.
- 14. K. Strack, F. J. Gunther. Tragverhalten von Nahtverbindungen bei Bauwerken aus PVC—beschichteten Polyestergeweben. Gewebe, Hochfrequenz-1979». Institut fiir Kunststoffverarbeitung, RWTH Aachen, F. R. Germany, p. 6.
- 15. U. Schulz. Tragverhalten von Nahtverbindungen bei Bauwerken aus PVC— beschichteten Polyestergeweben. Nahverbindungen. Symp. «Beschichtete Chemie-fasergewebe 1979». Institut fiir Kunststoffverarbeitung, RWTH Aachen, F. R. Germany p. 6—27.
- 16. H. Blumberg, W. Krummheuer, J. Nebe. Zeitstandverhalten von PVC—be-schichteten Polyamid 6.6- und Polyestergeweben in Praxis- und Laborpriifung. Kunststoffe 66 (1976) 2.
- 17. W. Krummheuer. Das mechanische Verhalten von PVC — beschichteten Polyestergeweben sowie deren Nahtverbindungen unter konstanter und intermittie-render Last. 1. Intern. Symp. «Weitgespannte leichte Flachentragwerke», Stuttgart, F. R. Germany, 1976, Vol. 2.
- 18. H. Blumberg, W. Krummheuer. Das Verhalten von PVC — beschichteten Polyestergeweben bei intermittierender Belastung. Kunststoffe 67 (1977) 772.
- 19. H. Blumberg. Eurofabric 1978, edited by: Enka Ag, Wuppertal, F. R. Germany.
- 20. W. Krummheuer. Light Resistance of Industrial Polyester and Polyamide 6.6 Yarns and of PVC—Coated Fabrics made from these Yarns, presented at CPAI— Coaters and Laminators Meeting. Aug. 1980, New York, N. Y. USA.
- 21. Deutsche Industrie-Norm 4104.
- 22. W. Krummheuer. Development Activities of the Industrial Yarns Institute for Coated and Rubberized Fabrics. Journal of Coated Fabrics 8 (1978) 54.
- 23. J. Linecker. Mehrschichtige Membrankonstruktionen zur Energieeinsparung und gewinnung in Membrankonstruktionen, edited by E. Bubner et ai. Verlagsge-sellschaft W. Muller GmbH, Koln, 1979.
- 24. Deutsche Industrie-Norm 4102.
- 25. Norme frangaise enregistree NF P 92—507.
- 26. G. Konig, M. Heunisch. Gutachterliche Stellungnahme, Teil 1 und 2. «Zur Festlegung von Sicherheitsanforderungen fiir den Standsicherheitsnachweis von Tragluftbauten», Januar 1979. AZ: G 78 106, ordered by: Giiteiiberwachungsge-meinschaft Membrankonstruktionen e. V., Bad Vilbel 1.
- 27. W. Krummheuer. Eurofabric 1978, edited by: Enka AG, Wuppertal, F. R. Germany.
- 28. V. V. Yermolov, S. B. Voznesensky. Air — Supported Structures in Severe Winter Conditions IASS—Working Group of Pneumatic Structures 1978, p. 171.
- 29. W. Krummheuer. Eurofabric 1980, edited by : Enka AG, Wuppertal, F. R. Germany.
- 30. W. Krummheuer. Technical Developments in Western Europe in the Field of Coated Industrial Fabrics presented at: CPAI — Textile Technology Forum. Oct. 1980, Reno, Nevada, USA.
Примечания
1. Явление релаксации напряжений для воздухоопорных оболочек нехарактерно в связи с отсутствием зависимости напряжений в оболочке от удлинений материала; «подтягивать» приходится только тентовые покрытия.