Для цемента, изготавливаемого совместным помолом компонентов, следует использовать негигроскопичные соединения щелочных металлов — соду, фтористый натрий и т. п. Во всех остальных случаях щелочные компоненты необходимо вводить с водой затворения.
Шлакощелочной цемент должен быть размолот до Sуд=3000÷3500 см2/г по ПСХ-2 или остатка на сите 008 не более 5%.
Для ускорения помола можно вводить активные добавки — эффузивные горные породы, известняки, горелые породы — в количестве не более 25% от массы шлака.
Условия транспортирования и хранения шлакощелочного цемента аналогичны условиям для портландцемента (ГОСТ 10178—62). Кроме того, они должны исключать попадание в этот цемент портландцемента, извести и гипса.
Марка шлакощелочного цемента находится в пределах 300—1000 и зависит от тонины помола, химического состава шлака, содержания в нем стекловидной фазы, природы и расхода щелочного компонента.
Требования к заполнителям. В качестве крупного заполнителя следует использовать щебень и гравий, удовлетворяющие требованиям ГОСТ 8267—75, ГОСТ 10260—74 и ГОСТ 8268—74.
В качестве мелкого заполнителя можно применять пески природные и искусственные, удовлетворяющие требованиям ГОСТ 10268—70 со следующими дополнениями: могут применяться пески с модулем крупности до 0,9; содержание в песках частиц алевритовых фракций может быть увеличено до 20, а глинистых до 5%.
Прочность и морозостойкость заполнителя оценивается испытанием в бетоне.
Нельзя применять заполнители, содержащие зерна гипса или ангидрита.
По минералогическому составу песчаная и алевритовая фракции заполнителя могут быть представлены кварцем, известняками, полевошпатными и другими минеральными образованиями, использование которых допускается в обычных бетонах, а глинистая — каолинитом, метагаллуазитом, галлу-азитом, монтмориллонитом, а также их смесями.
Присутствие в заполнителе более 0,5% минеральных веществ, легко взаимодействующих со щелочами с образованием сернистых, хлористых и других щелочных солей сильных кислот, не допускается.
Органических щелочерастворимых веществ (т. е. свободных гуминовых кислот) в заполнителе не должно быть больше 0,2%.
Подбор составов бетонов. Приведенные данные о вещественном составе продуктов гидратации шлакощелочных цементов позволяют рекомендовать общие принципы подбора составов бетонных смесей на их основе.
Прежде всего проектируется состав шлакощелочных вяжущих. Он определяется составом новообразований, которые предполагается синтезировать в бетоне при принятом режиме твердения.
Ожидаемый, или предпочтительный, состав новообразований в зависимости от состава шлакощелочного вяжущего по окислам, содержащимся в самом шлаке, может быть установлен по приведенным выше результатам рентгеноструктурного анализа гидратных новообразований и термодинамическому расчету шлакощелочных систем на основных, нейтральных и кислых шлаках.
Содержание окиси кальция в них находится в пределах 30—50%. Соотношение между глиноземом и кремнеземом в шлаке превышает оптимальное 1:(2-4), обеспечивающее формирование водостойких щелочных гидроалюмосиликатов и достигает 1:6—1: 8. Избыточный по отношению к оптимальному для щелочных гидроалюмосиликатов кремнезем будет связываться в низкоосновные кальциевые гидросиликаты тоберморитовой группы.
С ними будут суммироваться гидраты, синтезируемые при взаимодействии активных добавок с едкими щелочами состава R2O·Al2O3·xSiO2·nH2O, где х = 2, 3, 4. Причем наиболее вероятный вещественный состав связки в начальные сроки твердения R2O·Al2O3·2SiO2·nH2O; при кратковременном пропаривании — R2O·Al2O3·(2—3)SiO2·nH2O; при длительных пропаривании или запаривании — R2O·Al2O3·4SiO2·nH2O.
Зная состав шлака, задаваясь расходом щелочного компонента и вводя добавки, можно рассчитать состав новообразований или, задаваясь составом новообразований, рассчитать состав шлакощелочного цемента. При этом следует руководствоваться тем обстоятельством, что в шлакощелочных вяжущих роль щелочного компонента, в основном, сводится к созданию условий, при которых безводные вещества шлака переходят в гидратную форму, образуя низкоосновные силикаты кальция, а щелочные окислы, взаимодействуя с алюмокремниевым веществом шлака, связываются в водостойкие щелочные гидроалюмосиликаты. Кроме того, едкие щелочи, возникающие в процессе гидратации вяжущего, связывают глинистые минералы или стекловидные породы добавки или заполнителя.
При использовании в виде щелочного компонента едких щелочей или щелочных орто- и метасиликатов шлак может совсем не содержать окиси кальция (топливный шлак).
Для основных шлаков, независимо от условий твердения, можно использовать щелочные компоненты первой (едкие щелочи), второй (несиликатные соли слабых кислот) и третьей (силикатные соли) групп; для нейтральных и кислых шлаков твердение в естественных условиях и в воде обеспечивают щелочные компоненты первой и третьей групп; щелочные компоненты второй группы в этом случае следует использовать в сочетании со щелочными соединениями первой и третьей групп; при твердении же в условиях гидротермальной обработки так же, как и для основных шлаков, могут использоваться щелочные компоненты всех трех групп.
На основании вышеизложенных соображений задаются видом и расходом щелочных компонентов, после чего определяют марку шлакощелочного цемента по ГОСТ 310—60 со следующими отклонениями, определяемыми способом его получения.
Первый способ предусматривает выдачу готового цемента, полученного путем совместного помола гранулированного шлака с содой; второй — двух его компонентов — шлака молотого гранулированного и любого щелочного компонента, поставляемых в комплекте раздельно.
При производстве шлакощелочного цемента по первому способу марка цемента определяется по ГОСТ 310—60 со следующими изменениями:
1. С целью улучшения условий растворения соды в цементе рекомендуется предварительное перемешивание цемента с водой в пропеллерной мешалке. Длительность перемешивания 5 мин. Количество воды затворения принимается из расчета, чтобы В/Ц не превышало 0,34.
2. Для определения прочностных характеристик цемента изготавливаются образцы — балочки из цементного раствора 1:3, состоящего из одной части цемента и трех частей песка, при В/Ц не более 0,34 и консистенции раствора, характеризуемой расплывом конуса на встряхивающем столике не более 105 мм.
3. Образцы — балочки из шлакощелочного цемента, в отличие от портландцемента, после изготовления хранятся не в ваннах с гидравлическим затвором, а в формах нераспалубленными в течение 3 суток. По истечении 3 суток образцы осторожно расформовывают и укладывают в бассейн с водой в горизонтальном положении таким образом, чтобы они не соприкасались друг с другом.
4. Допускается ускоренное испытание цемента по следующей методике. Образцы — балочки — не ранее, чем через 4 ч после изготовления, подвергаются пропариванию в формах по режиму 3 + 6 + 3 при температуре изотермического прогрева 95±5°С. Испытание образцов в этом случае производится через сутки после тепловой обработки. Прочность образцов должна обязательно составлять не менее 80% от марки цемента, получаемой на 28 день водного твердения.
5. С целью повышения активности цемента вместо воды затворения допускается применять растворы соединений щелочных металлов низкой плотности — до 1,10 г/см3 (соду, смесь соды с поташем, растворимое стекло с силикатным модулем до 2, в том числе мета- и дисиликат натрия).
При производстве шлакощелочного цемента по второму способу марка цемента также определяется по ГОСТ 310—60 со следующими изменениями:
1. Для определения прочностных характеристик цемента изготовляют образцы — балочки из цементного раствора 1:3, состоящего из одной части по массе цемента и трех частей песка.
Затворение сухой смеси должно производиться растворами едких щелочей, несиликатных и низкомодульных силикатных солей щелочных металлов плотностью 1,20 г/см3 (эталонный раствор) из такого расчета, чтобы водоцементное отношение было не более 0,36, а расплыв конуса на встряхивающем столике, характеризующий консистенцию раствора, не более 105 мм.
2. Активность цемента зависит от природы щелочного компонента и его расхода. Поэтому для получения высокомарочного цемента (М600—1000) затворение смеси следует производить более концентрированными растворами едких щелочей или низкомодульных растворимых стекол, в том числе мета- и дисиликатов натрия. Для повышения активности цемента на любых щелочных компонентах следует увеличивать плотность их растворов.
В остальном испытания проводятся так же, как и для шлакощелочных цементов совместного помола.
Установив активность цемента, подбирают состав бетонной смеси. Для этой цели целесообразно пользоваться известными методами подбора, применяемыми для портландцементного бетона.
Кроме этих методов, разработаны методы, учитывающие особенности шлакощелочных цементов. Некоторые из них приводятся ниже.
Метод подбора состава бетона на шлакощелочном вяжущем, разработанный И. М. Френкелем и Э. А. Шахмуратьян [63], основывается на следующих положениях:
- заданная прочность бетона при постоянном качестве применяемых материалов определяется качеством шлакощелочного клея, состоящего из шлака и затворителя (Ш:З);
- требуемая по условиям работ удобоукладываемость смеси достигается при определенном количестве шлакощелочного клея данного качества;
- техническая эффективность состава бетона (минимальный расход шлака и щелочи) обеспечивается при определенном (оптимальном) соотношении фракции заполнителя в бетоне (r=П/(П+Щ)).
Проектирование состава бетона на конкретном шлакощелочном цементе и заполнителях надо начинать с установления фактора прочности бетона (отношения шлак : затворитель 15%-ной концентрации — Ш : 3). В интервале Ш:З — 1,5÷3 функция Rб=f(Ш:3) аппроксимируется к линейной. Для установления такой зависимости изготавливают три состава бетонной смеси. Ориентировочные составы для пробных замесов приведены в табл. 27.
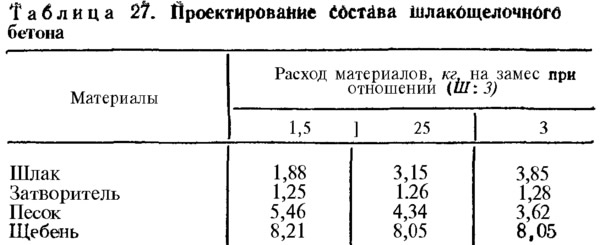
Изготовленные образцы выдерживают 4—16 ч в помещении с нормальной температурой и влажностью, а затем пропаривают по режиму, принятому на данном предприятии, испытывают образцы на сжатие и строят зависимость Rб=f(Ш:3).
На основании полученной зависимости для заданной прочности устанавливают требуемое отношение шлак : затворитель (Ш:3). В случае, если требуемое (Ш:3)>3, что усложняет условия уплотнения бетонной смеси, следует эту функцию установить для вяжущего с концентрацией затворителя 20%, Это обеспечит снижение требуемого (Ш:3). Если требуемое (Ш:3) попадает в область низких значений, при которых расход шлака будет меньше минимально допустимого (Шmin≈300 кг/м3),то следует перейти на применение затворителя 12%-ной концентрации, что обеспечит возможность увеличить требуемое отношение (Ш:3), а следовательно и расход шлака (Ш).
Определение зависимостей консистенции бетонной смеси от количества шлакощелочного клея данного качества, как и выбор оптимальной доли песка в смеси заполнителей, устанавливается опытным путем как и для обычных цементных бетонов. Далее определяется вес сухих материалов и количество затворителя определенной концентрации на 1 м3 бетонной смеси.
При поступлении новой партии шлака данного завода достаточно изготовить 2 состава бетонной смеси при отношениях (Ш:3)=1,5 и (Ш:3)=3 и определить по установленной функции Rб=f(Ш:З) требуемое отношение (Ш:3).
Подбор состава тяжелого бетона на шлакощелочном вяжущем представлен на схеме.
В связи с возможной влажностью заполнителей в дозировку затворителя, как и в дозировку воды для цементных бетонов, вносят производственные поправки. Однако следует отметить, что в бетонах на шлакощелочном вяжущем изменение количества воды изменяет концентрацию затворителя, что отражается на качестве шлакощелочного клея. Для возможности учета влаги, содержащейся в заполнителях, нами предлагается готовить более концентрированные растворы, а затем доводить их до нужного содержания воды в затворителе заданной концентрации с учетом влажности заполнителей. Так, при работе с затворителем 15%-ной концентрации необходимо готовить затворитель 20%-ной концентрации. На замес отвешивают (или отмеривают) определенное количество затворителя 20%-ной концентрации с количеством щелочи, равным содержащемуся в необходимом по подбору количестве затворителя 15%-ной концентрации (табл. 28), Затем добавляют (в соответствии с графой — «добавка воды») необходимое для получения 15%-ной концентрации количество воды за вычетом воды, находящейся во влажных заполнителях.
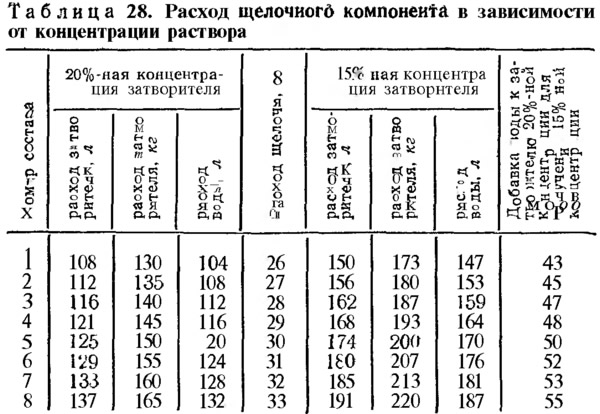
Например, влажность щебня — 1%, песка — 3%, расход материалов на 1 мг по производственному составу, кг: шлака — 450, затворителя 15%-ной концентрации — 180, песка — 621, щебня — 1150. По строке 2 табл. 28 находим, что необходимое количество щелочи для такого количества затворителя — 27 кг. С таким количеством П необходимо отвесить 135 кг (или отмерить 112 л) затворителя 20%-ной концентрации. Добавка воды для получения 180 кг (153 л) затворителя 15%-ной концентрации за вычетом воды, содержащейся в заполнителях, составит
45 — (621·0,03 + 0,01·1150) = 45 — 30,2 = 14,8 л.
Наряду с описанным способом, применяя метод абсолютных объемов для подбора состава бетона, можно использовать предложенные Днепропетровским филиалом НИИСПа [57] зависимости прочности бетона Rб от водовяжущего отношения В/Вж и активности вяжущего Rв при твердении бетонов в нормальных условиях

при условии тепловлажностной обработки (t°=85÷90°С)

В табл. 29 приведены расходы материалов для пробных замесов крупнозернистых шлакощелочных бетонов, в случае расчета их составов по методике ВНИИСТа.
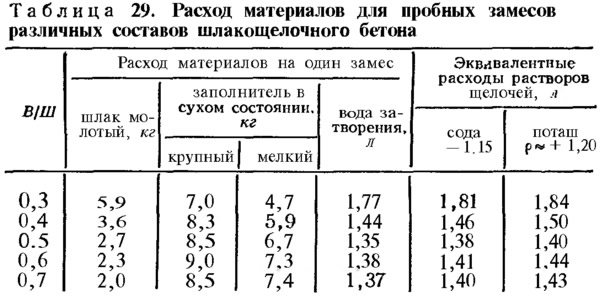
Ориентировочный расход воды затворения, в зависимости от требуемой консистенции и качества заполнителей, может быть назначен по табл. 30.
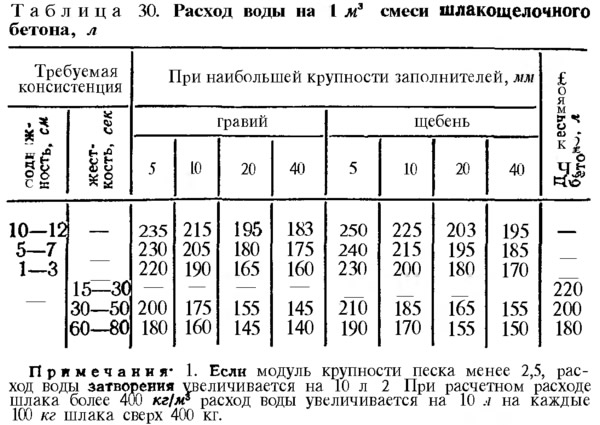
Выбранный по табл. 30 расчетный расход воды затворения (В) служит основанием для назначения состава бетона.
Расход шлака (Ш) определяется на основании определенного из эксперимента фактора В/Ш по формуле

Потребный расход щелочного раствора (Р) заданной плотности (ρ) определяется по формуле

где С — содержание сухого щелочного компонента в растворе, г/л.
Зависимость плотности раствора соды (ρ, г/см3) от концентрации d, г/кг раствора, выражается формулой

Расход сухого щелочного компонента А определяется по формуле

Суммарный расход заполнителей (П + Щ) вычисляется по формуле

где γсм — объемная масса уплотненной смеси, найденная из эксперимента; Рρ — масса раствора щелочного компонента при плотности ρ.
Доля песка (р) в смеси заполнителей может быть принята при использовании гравия р=0,36÷0,38; при использовании щебня — р=0,40÷0,47. Тогда расход заполнителя определяется по формулам:

В основу подбора шлакощелочного мелкозернистого бетона также может быть положен метод абсолютных объемов [59]. Отличием методики является то, что кроме такого традиционного показателя, как водовяжущее отношение, учитывается также и водопотребность заполнителей. Это объясняется тем, что подвижность исследуемых бетонных смесей определяется не только количеством воды, которое необходимо для придания пластичности тесту вяжущего, но и в значительной степени водой, необходимой для смачивания заполнителя. Для обычных мелкозернистых бетонов принято, что количество воды на смачивание заполнителей является величиной постоянной, так как применяемые заполнители имеют относительно низкую удельную поверхность (от 20 до 150 см2/г) и вследствие этого обладают низкой и примерно равной водопотребностью.
В бетонах на шлакощелочных вяжущих удельная поверхность заполнителя, даже без учета глинистых минералов, колеблется в широких пределах от 20 — для песков до 800—900 см2/г — для супесей. Следовательно, количество воды, необходимое для смачивания заполнителей, будет различным. В связи с этим при проектировании бетонной смеси используется такой показатель, как оптимальная влажность бетонной смеси, которая изменяется от 8 для крупных песков до 14% для пылеватых супесей.
Расход шлака в этих бетонах целесообразно ограничить 15—25%, а в отдельных случаях, при высокой дисперсности заполнителя, можно допустить 30%.
В этом случае содержание отдельных компонентов в шлакощелочном бетоне будет находиться в таких пределах, кг/м3: мелкий заполнитель — 70—85%, или 1500—1900; молотый шлак — 15—30%, или 300—600; щелочной компонент — 1,0—2,0%, или 20—40.
Марку шлакощелочного бетона на дисперсных заполнителях определяют на кубах с размерами сторон 10 см, изготовленных из бетонной смеси рабочего состава и испытанных после тепловлажностной обработки при температуре 95+5°С по режиму 3+6+2 ч или хранении в нормальных условиях в течение 28 суток.
Влажность смеси на песчаном заполнителе определяется в зависимости от требуемой подвижности и метода укладки по табл. 30.
Содержание шлака и воды в смесях на заполнителях, включающих глинистые и пылеватые примеси, назначается с учетом их дисперсности. При высоком содержании этих составляющих следует принимать верхний предел влажности, при малом — нижний.
Оценка содержания шлака в смеси, проц.: малое — менее 20, среднее — 20, высокое — 25 и более.
Ориентировочный состав смеси и влажность шлакощелочного бетона на дисперсных заполнителях принимается в указанных выше пределах.
Для экспериментальной проверки необходимо назначить не менее двух дополнительных составов с таким расчетом, чтобы основной состав был промежуточным. Дополнительные составы должны отличаться от основного по содержанию шлака в среднем на ±2%. Содержание воды и щелочного компонента во всех составах остается постоянным. За счет изменения содержания шлака изменяется содержание заполнителя.
В соответствии с установленными составами бетона изготавливают пробные замесы. Последовательность перемешивания компонентов такова, сначала заполнитель перемешивают в сухом состоянии с молотым шлаком, затем полученную смесь затворяют водным раствором щелочного компонента. В случае совместного помола шлака со щелочным компонентом цемент предварительно затворяют водой и перемешивают.
После этого полученный шлам смешивают с заполнителем.
Если ни в одном из приготовленных замесов проектная марка не будет достигнута, испытания следует повторить, изменив состав бетона.
Расчет завершается составлением таблицы расхода материалов на 1 м3 бетона в плотном теле. Далее производится проверка и подбор на опытных замесах, которые следует готовить на сухих заполнителях.
После получения удовлетворительных результатов нужно внести поправки, учитывающие естественную влажность материалов.
Примеры расчета. Приводим примеры подбора составов шлакощелочных мелкозернистых бетонов.
Пример 1. Задано: влажность смеси W=13%, масса одного замеса Р=350 кг (принята с учетом коэффициента выхода бетона из бетономешалки 0,6). Емкость бетономешалки 250 л, объемная масса шлакощелочного бетона γ=2300 кг/м3.
Состав смеси, проц.: заполнителя — 75; шлака — 25. Влажность грунта не превышает 1,5% и в расчете не учитывается. Смесь затворяется 15%-ным раствором соды.
Расчет:
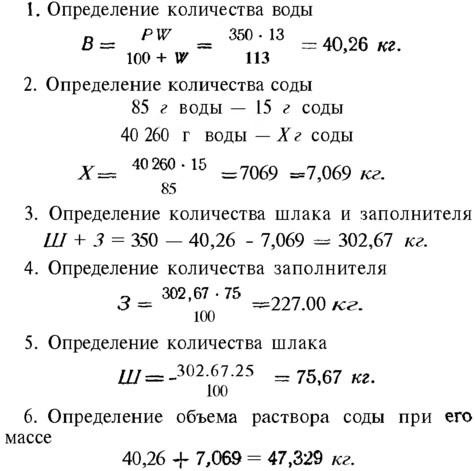
Плотность 15%-ного раствора соды равна 1,15 г/см3. Следовательно, объем, который займет полученный раствор, составляет:
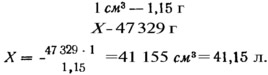
Пример 2. Исходные данные те же, что и в первом примере, кроме влажности заполнителя WЗ, которая равняется 5%. Содержание воды, шлака и заполнителя принимаем по примеру 1.
1. Определение количества воды В, содержащейся в заполнителе

где W — влажность заполнителя.
Следовательно, для приготовления бетонной смеси нужно взять 227+10,8=237,8 кг заполнителя (с учетом содержащейся в нем воды).
2. Поскольку в смесь вместе с заполнителем вводится 10,8 кг воды — общее ее количество надо уменьшить на эту величину

3. Уточняем концентрацию полученного раствора соды.
Масса раствора равна: 29,46+7,069=36,529 кг.
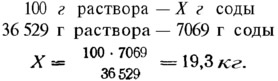
Следовательно, концентрация раствора соды 19,3%.