Доставляемый на завод гипсовый камень укладывают в штабели. Запас его на заводе должен быть не менее трехмесячного. Гипс обжигают на ангидрит в шахтной или вращающейся печи. В первом случае гипсовый камень дробят на щековой дробилке на куски размером от 5 до 15 см в поперечнике. Во втором случае гипсовый камень дробят до зерен величиной 3—4 см в поперечнике.
Мелочь, получающуюся при дроблении гипсового камня для обжига в шахтной печи (количество ее не должно превышать 5—10%, величина зерен — от муки до 5 см), нельзя загружать в печь, так как это нарушает тягу (эту мелочь используют для производства штукатурного гипса).
На рис. 11 изображена схема производства ангидритового цемента с двумя катализаторами (сульфат натрия и железный купорос), Принятая на одном из действующих заводов. Гипсовый камень обжигают в шахтной печи производительностью около 50 т ангидрита в сутки.
Дробленый гипсовый камень со склада 1 при помощи скипового подъемника 2 подают в шахтную печь 3. Размер кусков камня, подаваемого в печь, регулируют при помощи решетки, установленной над загрузочной воронкой. От размеров кусков зависит не только продолжительность и полнота обжига, но и равномерность питания печи сырым материалом. Слишком большие куски гипса при поступлении в загрузочную воронку, диаметр которой составляет около 50 см, могут заклиниться в горловине и воспрепятствовать посадке конуса в отверстие воронки, а это нарушит тягу в печи и задержит поступление в нее камня.
Шахтная печь для обжига гипсового камня на ангидрит должна быть с выносными топками, с принудительным дутьем под колосники и подводкой вторичного воздэрса для создания окислительной среды. Основные размеры такой печи производительностью около 50 т ангидрита в сутки приведены на рис. 12.
Техническая характеристика печи такова:
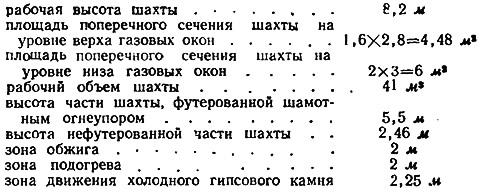
Гипсовый камень обжигают в температурном интервале 600—700°, с выдержкой в зоне обжига при указанной температуре около 3—4 час. и в зоне остывания 8 часов. При выдержке в зоне обжига в течение 3 часов ускоряется процесс обжига, соответственно уменьшается расход топлива и, следовательно, снижается себестоимость цемента. Весь процесс обжига гипсового камня на ангидрит занимает около 17—18 часов.
Гипсовый камень загружают в печь каждые 15 минут по 1 т. Воздух подают в зону охлаждения через верхнее или нижнее отверстие (при крупных кусках гипса — через нижнее отверстие, а при мелких — через верхнее). Дымосос должен работать с таким расчетом, чтобы в шахте создавалось разрежение в 1,5—2 мм вод. ст. или, в крайнем случае, во избежание вылета пламени из топок при заброске угля, нулевое давление в зоне жаровых влетных окон. Температура дымовых газов составляет 130—150°. Расход условного топлива около 7%. Коэффициент полезного действия печи — 0,5.
Продукт обжига выгружают из шахтной печи при помощи разгрузочного устройства системы Антонова с трехступенчатым шкивом на редукторе. Температура ангидрита при выходе из печи около 200—300°. Из печи ангидрит попадает на пластинчатый транспортер 4 (см. рис. 11) и направляется по последнему в дробилку 5 дчя измельчения до величины зерен 3—4 мм в поперечнике. Так как из шахтной печи ангидрит выходит хрупким, то для дробления вполне целесообразно применять молотковую дробилку конструкции Белякова, изображенную на рис. 13.
Корпус этой дробилки состоит из основания 1 и крышки 2, в верхней части которой крепится приемная воронка 3. На боковых выступах основания установлены подшипники 4, в которых вращается вал с насаженными на него двумя дисками 5. В отверстиях дисков шарнирно устанавливаются шесть молотков 6. Корпус дробилки с внутренней стороны облицован плитами 7 из закаленного чугуна или стали. В нижней части корпуса на шарнире 8 подвешивается колосниковая решетка 9.
Техническая характеристика молотковой дробилки Белякова такова:
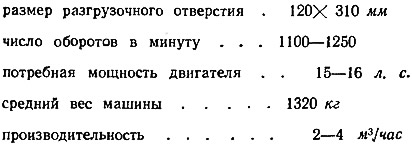
Пройдя дробилку, материал ковшовым элеватором 6 (см. рис. 11) (передается в главный железобетонный бункер 7, снабженный тарельчатым питателем. Объем бункера — около 70 м3. Бункер состоит из призматической пирамидальной частей; размер призматической части — 4,2X4,1X4,8 м, высота пирамидальной — 2,3 м. Запас ангидрита в бункере должен быть рассчитан не менее чем на двое суток работы, что очень важно на случай временной остановки агрегатов, расположенных между печами и главным бункером. Тарельчатый питатель диаметром 130 см делает 4 оборота в минуту.
Смеси катализаторов приготовляют следующим образом. Сульфат натрия со склада 8 (см. рис. 11) подают в сушилку 9 для подсушки, которая производится в подовой сушилке, во вращающемся сушильном барабане или в специальной установке для подсушки материала во взвешенном состоянии. После подсушки сульфат измельчают в дробилке 10, в которой измельчают также и ангидрит, и элеватором 11 подают в бункер 12 емкостью 9,7 м3. Часть ангидрита берут с пластинчатого транспортера 4 и тем же элеватором 11 направляют в бункер 13.
Оба бункера 12 и 13 через тарельчатые питатели подают сульфат и ангидрит в весовом отношении 1 : 10 в смесительный шнек 14 длиной 4 м. В шнек подается в минуту 5 кг катализатора и 50 кг ангидрита. Из шнека 14 смесь направляют элеватором 15 в бункер 16 емкостью 8,3 м3.
После того как заготовлена смесь сульфата натрия с ангидритом, таким же способом и в таком же соотношении заготовляют смесь из железного купороса с ангидритом. Железный купорос со склада 8 направляют в сушилку 9, измельчают в дробилке 10 и элеватором 11 перебрасывают в бункер 12, к этому времени уже освобожденный от измельченного сульфата. После подачи купороса в бункер 12 начинают подавать ангидрит. Его через дробилку 10 элеватором 11 подают в бункер 13, к этому времени также освобожденный от ангидрита первой смеси. Из обоих бункеров материалы через тарельчатые питатели снова направляют в смесительный шнек 14, откуда готовую смесь подают элеватором 15 в бункер 17 емкостью 8,3 м3.
Таким образом, бункер 16 наполняется смесью «сульфатной» (сульфат натрия -с ангидритом), бункер 17 — смесью «купоросной» (купорос с ангидритом) и бункер 7 — ангидритом (продуктом обжига гипсового камня в шахтной печи). Из всех этих-бункеров материалы через тарельчатые питатели подают в определенной пропорции на ленточный транспортер 18. Количество этих материалов контролируют при помощи особых указателей — двух металлических линеек с делениями в сантиметрах. Вертикальная металлическая линейка устанавливается на подъемном механизме, т. е. на колпаке, спускающемся от бункера на тарелку, а горизонтальная металлическая линейка — у горизонтального тарельчатого скребка.
Правильность дозировки материалов проверяют не менее 2—4 раз в смену. Только при равномерной подаче материалов из бункеров на транспортерную ленту обеспечивается в дальнейшем необходимое соотношение между ангидритом и катализаторами, и, следовательно, стандартное качество цемента.
С ленточного транспортера материалы поступают на помол в шаровую мельницу 19. Запас катализаторных смесей в бункерах 16 и 17 создается на 30—40 час. работы. Когда этот запас истощается, катализаторные смеси заготовляют снова в указанном выше порядке.
Ангидрит с катализатором размалывают в однокамерной укороченной шаровой мельнице с замкнутым циклом помола.
Техническая характеристика мельницы такова:
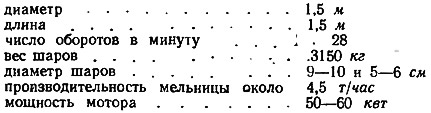
Подшипники мельницы охлаждают водой. Материал поступает в мельницу через полую цапфу со шнековыми лопастями на внутренней поверхности. Выходная полая цапфа с такими же лопастями снабжена сеткой, задерживающей крупные куски материала.
Мелкие частицы ангидритового цемента из мельницы 19 поступают при помощи элеватора 20 в сепаратор 21. В сепараторе от цемента отделяются крупные частицы, возвращающиеся обратно в мельницу.
Схема мельницы с сепаратором показана на рис. 14.
Техническая характеристика сепаратора такова:

Сепаратор снабжен шестью лопатками.
Так как размолотый ангидритовый цемент доходит до этой установки еще теплым, то частицы его прилипают к стенкам сепаратора, и поэтому каждые 2—3 дня его обязательно вскрывают и стенки очищают волосяными щетками. Крышки люков сепаратора должны плотно прилегать, так как иначе возможно выдувание тонких фракций цемента.
Из выходного отверстия сепаратора ангидритовый цемент поступает на ленточный транспортер 22 (см. рис. 11), а с него, через элеватор 23 — в железобетонные сил осы 24, которых должно быть от 2 до 4, емкостью 350—400 т каждый. Из силосов ангидритовый цемент направляют по течке непосредственно в железнодорожные вагоны 25 или навалом грузят в автомашины. Иногда его упаковывают в бумажные или джутовые мешки.
При работе только на одном катализаторе (известь, основной доменный шлак, обожженный доломит и др.) схема приготовления катализаторной смеси с ангидритом упрощается. Бункер 13 заполняют ангидритом, а бункер 12 — катализатором. Ангидрит и катализатор направляют в смесительный шнек 14 и элеватором 15 Поочередно подают в бункеры 16 и 17. Из последних материалы поступают через тарельчатые питатели и транспортерную ленту 18 в шаровую мельницу 19. Подача катализатора регулируется с таким расчетом, чтобы в конечном продукте (ангидритовом цементе) содержалось 3,5% извести (в зависимости от ее активности), или 10—15% доменного шлака, или 3,5% обожженного доломита.
Когда гипсовый камень обжигают на ангидрит во вращающейся печи, то схема производства ангидритового цемента предусматривает такие операции:
- 1) дробление гипсового камня в щековой дробилке до кусков величиной 3—4 см в поперечнике;
- 2) обжиг во вращающейся печи, футерованной шамотным огнеупором;
- 3) помол в шаровой однокамерной мельнице с сепаратором.
Если для производства ангидритового цемента используется природный ангидрит, то его до дробления обычно подсушивают при 170—180°. Предварительная подсушка снижает механическую прочность естественного камня и значительно облегчает помол.
В связи с тем, что исключается процесс обжига или продолжительность его уменьшается до 1 часа, себестоимость цемента из природного ангидрита ниже, чем из искусственно полученного безводного гипса.
Основные правила техники безопасности при работе на заводе ангидритового цемента те же, что и на заводах портландцемента.