Конвейерные способы. По конвейерной технологии с применением синтетического связующего изготавливают основной объем минераловатных изделий. Технологический процесс предусматривает: получение силикатного расплава; получение минерального волокна из расплава; приготовление раствора связующего; получение минераловатного ковра, пропитанного раствором синтетического связующего, формование и термообработку минераловатного массива заданной плотности; разрезку на изделия заданных размеров; упаковку и складирование готовой продукции.
Принципиальная схема технологического процесса получения изделий из минеральной ваты и технологическая линия СМТ-126 представлены на рис. 3.71 и 3.72.
Минеральный расплав перерабатывают в волокно центробежным способом с использованием комплекта многовалковой центрифуги СМТ-182 производительностью 3200 кг/ч по расплаву. Полученное минеральное волокно попадает в камеру волокноосаждения, на сетчатом конвейере которого образуется минераловатный ковер. Для отделения корольков на торцевой части камеры волокноосаждения устанавливают стальную плиту.
При производстве рулонных прошивных матов после камеры волокноосаждения устанавливают станок для прошивки минеральной ваты, после чего ковер обрезают, рулонируют и направляют на склад.
Для приготовления раствора связующего смешивают смолу с водой в необходимых пропорциях. Вода и смола из расходных баков поступает в объемные дозаторы, затем в промежуточный бак с мешалкой, далее в расходный бак с мешалкой, откуда по трубопроводу с помощью насосов раствор связующего подается для нанесения его на минеральные волокна.
Минераловатный массив заданной толщины и плотности формуют приложением к нему определенных механических усилий посредством профилирующих и калибрующих приспособлений, предусмотренных данной технологией. Деформативные свойства минераловатного ковра могут быть описаны уравнением
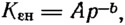
где Кεн — коэффициент пористости под нагрузкой; р — давление на минераловатиый ковер, Па; А и b — коэффициенты, зависящие от качественных показателей ваты.
Эмпирические значения коэффициентов А и b зависят от способа получения ваты и равны: 1,033 и 0,5 — при центробежно-дутьевом способе; 0,545 и 0,4 — при центробежно-валковом; 0,245 и 0,3 — при фильерно-дутьевом способе соответственно. Уравнение для Кея действительно в пределах давлений, обычно используемых в практике производсгза минераловатных изделий — (0,049—9,81)·104 Па, — и может быть использовано для определения давления, необходимого для формования изделий заданной средней плотности из волокон, полученных различными способами. Уменьшение Кεн свидетельствует о более высоких упругих свойствах волокна и необходимости большей нагрузки давлением. Так как упругие свойства возрастают с уменьшением диаметра волокна, то наибольшее давление при формовании минераловатного ковра необходимо применять для тонкого фильерно-дутьевого волокна. С увеличением среднего диаметра волокна и содержания неволокнистых включений восстанавливающаяся деформативнач способность ковра уменьшается.
После предварительной калибровки минераловатный ковер через промежуточный конвейер подается в камеру полимеризации на термообработку. Здесь ковер доуплотняется до заданной плотности и термообрабатывается, в результате чего происходят отверждение связующего с образованием фазовых конденсационных контактов и сушка ковра за счет прососа через его толщу газообразного теплоносителя. На рис. 3.73 показана камера полимеризации СМТ-128, входящая в состав технологической линии СМТ-126. (Камера полимеризации СМТ-097 имеет аналогичную конструкцию и отличается лишь длиной рабочей зоны).
Камера представляет собой установку непрерывного действия с позонным регулированием температуры и гидравлического режима. Конструктивно она состоит из секций длиной по 6 м каждая. Между секциями имеются шторы, разделяющие камеру на тепловые зоны.
Подпрессовка минераловатного ковра осуществляется между двумя парами конвейеров. Каждая пара состоит из сетчатого конвейера, рабочая ветвь которого лежит на рабочей ветви цепного конвейера. Сетчатый конвейер формирует поверхность изделия, а цепной создает давление прессования.
Подъем и опускание направляющих верхнего конвейера обеспечивают необходимый рабочий зазор между ветвями цепных и сетчатых конвейеров, что определяет толщину изготавливаемых изделий.
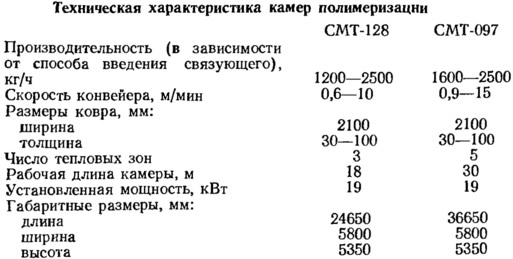
При тепловой обработке минераловатных плит, в которые связующее введено распылением, достаточно двух зон, при введении связующего способом полива — четырех зон.
Для получения и подачи теплоносителя в камеру полимеризации используют соответствующее теплотехническое оборудование. Теплоносителем служат топочные газы с температурой 180—250°С, получаемые в результате сжигания топлива и смешивания продуктов сгорания с отработавшими газами. В линиях по производству минераловатных плит на синтетическом связующем используют комплект теплотехнического оборудования марки СМТ-100 производительностью по теплоносителю 600—700 м3/ч.
На выходе из камеры полимеризации минераловатный ковер разделывают и охлаждают. При необходимости в месте выхода ковра из камеры можно расположить устройство для подклейки бумаги или другого материала, смоченного с одной стороны разогретым в ванне битумом.
По конвейерному способу с использованием синтетического связующего можно формовать: рулонные изделия (прошивные маты и минераловатный войлок); минераловатные цилиндры разного диаметра; плиты различной жесткости (ПМ — мягкие, ПП — полужесткие, ПЖ — жесткие, ППЖ — повышенной жесткости) и др.
Рулонные минераловатные изделия
Прошивные маты получают прошивкой на выходе из камеры волокноосаждения минераловатного ковра, который может заключаться в обкладки из различных материалов (картон, бумага, полиэтилен и др.) с одной или обеих сторон. В камере волокноосаждения минераловатный ковер может быть пропитан небольшим количеством связующего (1—2 %) или минерального масла для обеспыливания ваты. Перед прошивкой ковер незначительно уплотняют. Для данного типа изделий термообработку не применяют. После прошивки ковер разрезают, рулонируют, упаковывают и складируют.
Минераловатный войлок получают пропиткой ковра распылением связующего с последующим незначительным уплотнением и термообработкой. После камеры полимеризации ковер охлаждают, разрезают, рулонируют, упаковывают и складируют.
Технология получения минераловатных плит идентична, за исключением операции рулонирования и получения изделия более коротких размеров.
Минераловатные цилиндры
Минераловатные цилиндры на синтетическом связующем изготавливают способом навивки (рис. 3.74). Вначале увеличением скорости конвейера камеры волокноосаждения до 15 м/мин получают минераловатный ковер толщиной не более 30 мм, пропитанный синтетическим связующим. Далее ковер сетчатым конвейером подается на прорезиненную ленту 2 станка для навивки цилиндров (рис. 3.75). Лента совершает сложное движение, огибая ряд барабанов, в том числе и барабан на качающихся кронштейнах 8. Минераловатный ковер навивают на металлические, предварительно смазанные петролатумом, перфорированные скалки цилиндрической формы. При этом прорезиненная лента выполняет функции не только транспортирующего органа, но и уплотняющего. По достижении необходимой толщины навивки срабатывает концевой выключатель, и качающиеся кронштейны с помощью пневмоцилиндра 9 переводятся в горизонтальное положение. Отрывают минераловатный ковер от навитого на скалку цилиндра за счет включения электродвигателя и увеличения скорости движения ленты. Далее цилиндр со скалкой передают на станок проката и калибровки.
Калибровочный станок состоит из двух расположенных друг над другом ленточных конвейеров, движущихся в противоположных направлениях, в щель между которыми протаскивают скалку с цилиндром при помощи цепного конвейера. Калибровку и дополнительную подпрессовку цилиндров осуществляют за счет разницы в скорости движения цепного конвейера и ленточных калибрующих конвейеров.
Откалиброванные цилиндры на скалках с влажностью 10—12 % поступают в камеру полимеризации, где в течение 15 мин сушатся до влажности 0,3 % и отверждаются за счет прососа горячего теплоносителя с температурой 140—180°С через перфорированную скалку и минераловатный цилиндр.
Термообработанные цилиндры освобождают от скалок и подают на пост поперечной разрезки. Полную продольную разрезку цилиндров осуществляют лишь с одной стороны, с другой стороны делают надрез глубиной 10—15 мм, что облегчает их монтаж на трубопроводах. Заключительные технологические операции — упаковка цилиндров и их складирование.
Технологический процесс производства минераловатных цилиндров полумеханизирован и автоматизирован.
Плиты повышенной жесткости
Плиты повышенной жесткости (ППЖ) относятся к высокоэффективным минераловатным изделиям, интенсивное освоение выпуска которых в нашей стране началось в 70-е годы. Развитие мощностей по их изготовлению осуществляется наиболее интенсивно: уже в текущей пятилетке их выпуск возрастает в 5—6 раз по сравнению с предыдущими годами.
Средняя плотность плит повышенной жесткости примерно в 1,5 раза больше, а жесткость в 5—15 раз выше аналогичных показателей рядовой промышленной продукции.
Плиты повышенной жесткости по конвейерной технологии изготовляют тремя способами, отличительной особенностью которых являются количество и способ введения связующего в минераловатный ковер и направление ориентирования волокон в плите: 1) ленточного формования; 2) формования блоковым методом (ламельные плиты); 3) формования из гидромасс.
Ленточное формование ППЖ мало чем отличается от технологической схемы производства минераловатных изделий, представленной на рис. 3.71. Синтетическое связующее можно вводить способом распыления или полива минераловатного ковра. Требуемая жесткость плит в данном случае достигается за счет повышения содержания связующего до 10 % и увеличения давления подпрессовки в камере полимеризации.
Комплект оборудования СМТ-198 (рис. 3.76) производительностью 60—75 тыс. м3/год с автоматизированным управлением предназначен для производства методом ленточного формования минераловатных плит повышенной жесткости средней плотности 150—250 кг/м3. Ширина ковра 2050 мм. Скорость конвейера 0,6—5 м/мин, плавно регулируется. Толщина получаемых плит 30— 60 мм.
Волокно с нанесенным на него связующим осаждают и конвейерами рулонирующего автомата и промежуточным конвейером передают в камеру термообработки СМТ-199. Пройдя камеру термообработки, минераловатный ковер переходит на форматный станок, где его разрезают на плиты заданных размеров. Отрезанные кромки измельчают на установке измельчения отходов и возвращают пневмоконвейером в камеру волокноосаждення.
Параметры процесса тепловой обработки и конструктивное решение камеры термообработки СМТ-199 таковы, что длина ее рабочей зоны составляет всего 3 м. Удельное усилие подпрессовки 0,03 МПа. Камера оснащена устройствами, предотвращающими влияние неравномерной плотности ковра на процесс термообработки.
Волокна в изделиях, полученных методом ленточного формования, ориентированы в продольном направлении.
Блоковый способ получения ППЖ позволяет получать ламель-ные плиты повышенной жесткости без увеличения их средней плотности за счет вертикального ориентирования минеральных волокон. Технологическая схема производства плит повышенной жесткости с вертикально расположенными волокнами представлена на рис. 3.77.
В процессе осаждения минеральное волокно перемешивается с распыленным раствором связующего и осаждается на сетке непрерывно движущегося конвейера в виде ковра. Минераловатный ковер, пройдя по конвейерам станка прошивки минеральной ваты, рулонирующего автомата и по промежуточному конвейеру, поступает на подпрессовщик, где ножом продольной разрезки разрезается на две полосы и обжимается до толщины 120 мм. Прессованные полосы движутся далее в устройство механизма для поперечной резки, где разрезаются на заготовки размером 1000Х1000 мм.
Механизм загрузки заготовок переносит их в формы формовщика блоков. Заполненные блоки поочередно поступают на пост термообработки, где отверждаются горячим теплоносителем, далее — на пост охлаждения и выгрузки блоков на конвейер-накопитель. Загрузчик блоков перегружает блок с конвейера в механизм послойной резки. Блок ориентируют в пространстве таким образом, чтобы резка осуществлялась поперек волокон блока. В таком положении блок разрезают на слои, которые подклеивают к рубероиду, пергамину или другому покровному материалу при помощи битума. Готовые плиты передают на упаковку и складирование
Блоковый способ получения плит повышенной жесткости наиболее экономичен по энерго- и материалоемкости.
Весь процесс изготовления ламельных минераловатных плит автоматизирован.
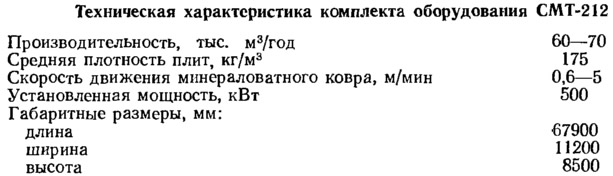
Способ формования ППЖ из гидромасс состоит из трех основных технологических операций: получения гидромассы, формования из нее непрерывного минераловатного ковра и его термообработки.
На рис. 3.78 показано технологическое оборудование линии СМТ-194 для производства минераловатных плит повышенной жесткости из гидромасс.
Особенность технологии заключается в том, что непропитанный минераловатный ковер из камеры волокноосаждения попадает в гидросмеситель периодического или непрерывного действия, куда подается раствор связующего и добавка в виде пенообразователя. Пенообразователь облегчает смешивание волокна со связующим, уменьшает измельчение волокна при перемешивании, повышает однородность гидромассы.
Полученная смесь попадает в расходный бункер формовочного механизма и раскладывается слоем на непрерывно движущийся конвейер. Слой можно формовать подпрессовкой гидромассы до заданной толщины слоя и отливкой слоя ковра. Схемы этих способов представлены на рис. 3.70. В обоих случаях осуществляется вакуумирование, в результате которого оптимизируется влажность ковра и содержание в нем связующего. Далее ковер поступает на термообработку, в процессе которой он уплотняется до заданной толщины и средней плотности материала. Затем в продольном и поперечном направлениях его разрезают на плиты заданных размеров, упаковывают их и складируют.
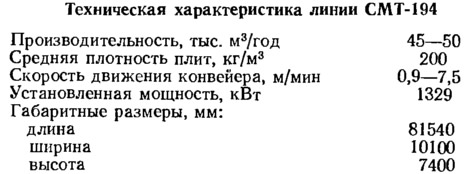
Минераловатные плиты, полученные из гидромасс, имеют структуру, занимающую промежуточное положение между структурой плит с горизонтально расположенными волокнами и ламельных плит с вертикально направленными волокнами, т. е. характеризуются хаотичным расположением волокон. Этим можно объяснить то положение, что при равной средней плотности у этих плит прочность на сжатие выше, чем у плит с горизонтально направленным волокном.
Основные показатели различных видов минераловатных плит на синтетическом связующем приведены в табл. 3.26.
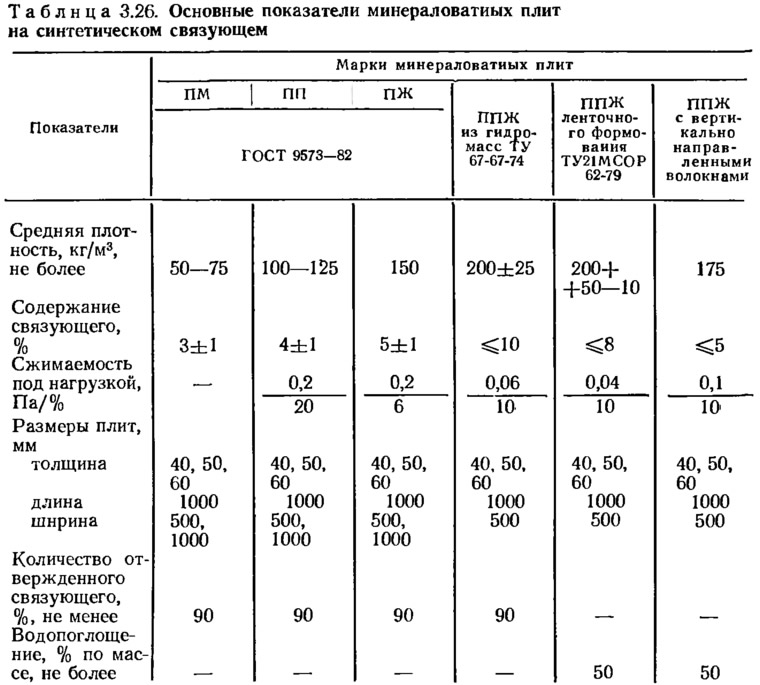
Прессовый способ формования минераловатных изделий включает следующие основные технологические операции (рис. 3.79): получение связующего в виде водно-битумной эмульсии; разрыхление минеральной ваты; получение гидромассы из эмульсии связующего и минеральных волокон; формование изделий из гидромасс; тепловую обработку изделия.
Отличительной особенностью технологии жестких изделий на битумном связующем прессовым способом является ее цикличность.
Битумную эмульсию получают при температуре 175—180°С за счет сплавления непарафинистых битумов марок БН-III и БН-V, которые перекачивают затем в бак-смеситель, куда подают канифоль. В другом баке готовят суспензию минерального наполнителя, сообщающего изделиям жесткость и огнестойкость, в качестве которого могут использовать каолиновые и бентонитовые глины, трепел и диатомит. Для получения устойчивой суспензии производят пептизацию глин добавкой едкого натра.
Концентрированную битумно-каолиновую эмульсию приготавливают в диспергаторе, а затем в баке-смесителе, где она разбавляется до 3 %-й рабочей концентрации. Далее эмульсию и разрыхленную минеральную вату подают в смеситель, в котором получают гидромассу с соотношением вата:вода в пределах 1:9—1:10.
Из гидромассы способом прессования изготавливают плиты, полуцилиндры, сегменты. Прессование, наряду с вакуумированием через перфорированные вакуум-щит и днище формы, позволяет понизить остаточную влажность изделий перед термообработкой до 75 % при прессовании и до 60% — при комплексном прессовании с вакуумированием. Давление прессования плит 0,003—0,004 МПа, полуцилиндров 0,015—0,02 МПа.
Схема устройства для формования полуцилиндров из гидромасс с применением битумного связующего методом прессования и вакуумирования приведена на рис. 3.80.
Аналогично формуют минераловатные плиты на битумном связующем. Отформованные изделия направляют на термообработку в туннельные сушильные камеры с противопотоковым движением теплоносителя, где удаляют оставшуюся влагу и отверждают изделия в течение 12—24 ч.
Производство твердых плит
Производство твердых плит также относится к цикличному способу производства. Пропитывают минераловатный ковер в камере волокноосаждения. Затем его прошивают и разрезают на заготовки, которые на металлических полых поддонах подают на многопольные гидравлические прессы, где их уплотняют и термообрабатывают. Термообработку осуществляют за счет подачи теплоносителя в полость поддонов. Далее изделия охлаждают, обрезают и складируют.
Твердые плиты отличаются повышенной средней плотностью (300—500 кг/м3) прочностью при изгибе 0,4—1,2 МПа.