Расход цемента в таких бетонах на 1 м3 колеблется в пределах от 150 до 500 кг. Однако следует иметь в виду, что опило- и стружкобетоны с расходом цемента менее 280—300 кг на 1 м3 можно укладывать только монолитным способом, ибо получение достаточно прочных и транспортабельных изделий при таком расходе вяжущего затруднительно.
В состав опило- и стружкобетонов большей частью вводят различные минеральные добавки (глину, песок, трепел). Иногда в шихту для нейтрализации вредно действующих на цемент экстрактивных веществ древесины добавляют известь. Такие добавки, как известь, глина и трепел придают шихте большую подвижность. Для ускорения твердения цемента и для минерализации древесных частиц используют хлористый кальций, жидкое стекло, хлорную известь и др.
В качестве утеплителя бесчердачных кровель промышленных зданий институтом ЮжНИИ предложен опилобетон под наименованием термопорит. Материал характеризуется следующим расходом вяжущих на 1 м3: цемента — 230 кг, известкового теста — 100 кг. Кроме того, он содержит добавку растворимого стекла и хлорной извести. Термопорит имеет предел прочности при сжатии от 5 до 15 кг/см2 при объемном весе от 500 до 650 кг/м3. Укладывается он монолитным способом.
Тем же институтом предложен другой опилобетон под наименованием «термиз». на 1 м3 которого расходуется (в кг): цемента — 150—170; трепела — 200—240; изъести-пушонки — 30—50. Термиз естественного твердения имеет предел прочности при сжатии — 5—10 кг/см2. Объемный вес термиза колеблется от 550 до 700 кг/м3. Предназначается он преимущественно для утепления кровель.
Опилобетон на цементе с добавкой песка нашел применение для строительства стен сельскохозяйственных сооружений в Латвийской ССР.
Наибольшее распространение в зарубежном строительстве имеет опилобетон, изготовляемый по способу шведской фирмы «Третон». Способ обработки опилок фирмой «Третон» сохраняется в секрете. Предел прочности при сжатии такого опило-бетона на цементе с добавкой песка составляет до 50 кг/см2 при объемном весе до 1300 кг/м3. Опилобетон «Третон» применяют для изготовления изделий (пустотелых стеновых блоков, перегородочных плит и пр.), а также укладывают и монолитным способом (например, для устройства оснований под настил из линолеума, плиток, паркета). Опилки, обработанные по способу фирмы «Третон», используют и в растворах для штукатурки и кладки, а также для звукопоглощающей отделки помещений.
В Польше изготовляется опилобетон с применением цементного вяжущего. В качестве минерализатора рекомендуется применять хлорную известь с концентрацией раствора 4—10%, глину, коллоидные взмученности, а в качестве заполнителя — опилки хвойных пород с влажностью 20—30%.
В Австралии применяется опилобетон на цементе с добавкой песка. Такой опилобетон состава 1:1,25:0,75 (цемент: опилки: песок) имеет предел прочности при сжатии 90 кг/см2 при объемном весе 1000 кг/м3. Для укладки основания под пол рекомендуется состав 1:1:2 или 1:2:1 (цемент:спилки:песок). В качестве минерализатора опилок применяется хлористый кальций.
За рубежом также широко применяются изделия из стружкобетона, изготовляемого по способу швейцарской фирмы «Дуризол». Расход цемента колеблется в пределах от 300 до 450 кг/м3. Здания с применением дуризола сооружаются в странах с различным климатом — от холодной Гренландии до тропических зон Африки. Далл указывает, что в США и Канаде имеется ряд дуризоловых заводов, работающих по лицензиям, закупленным в Швейцарии. Из дуризола изготовляют блоки и плиты.
Подбор состава опило- и стружкобетонов
Во ВНИИНСМе было изучено влияние производственных факторов на свойства опило- и стружкобетонов. Этой работой было доказано, что для получения высококачественных изделий большое значение имеет вид применяемого минерального вяжущего, правильный подбор состава, интенсивность уплотнения и условия вызревания. Под правильным подбором состава понимается не только установление правильного соотношения между вяжущим и заполнителем, но, что не менее важно, травильное назначение водной добавки.
Имеется определенное сходство свойств пористых минеральных заполнителей, применяемых в легких бетонах, и древесных частиц, заключающееся в способности тех и других как отсасывать воду из окружающей массы вяжущего, так и отдавать свою влагу твердеющему вяжущему, сохраняя в каждый данный момент равновесие между водонасыщением вяжущего и заполнителя.
Основная трудность при подборе состава опило- и стружкобетонов заключается в том, что неизвестно, как распределяется влага между древесными частицами и вяжущими, каково оптимальное содержание теста вяжущего (истинное В/Ц) для получения массы бетона с наилучшей удобоукладываемостью.
Для выявления баланса влаги во ВНИИНСМе были поставлены специальные опыты, которые показали, что предел увлажнения древесных частиц в шихте оптимальной влажности составляет 240—300% от их собственного веса, а истинное водоцементное отношение колеблется от 0,2 до 0,4 в зависимости от жирности состава. Чем жирнее состав, т. е. чем больше вяжущего, тем меньше истинное водоцементное отношение.
Правильное назначение величины водной добавки очень важно: недостаток влаги ведет не только к чрезмерному обезвоживанию цементного теста в результате отсоса воды из него заполнителем, но и к ухудшению удобоукладываемости древесно-цементной массы, из-за чего даже при значительной затрате труда на уплотнение не удается получить доброкачественных изделий, ибо недостаточно увлажненные древесные частицы упруги и при уплотнении пружинят.
Переувлажнение также недопустимо: избыток воды, свыше той, которая удерживается древесными частицами и той, которая нужна для нормального твердения цемента, ослабляет цементный камень. Отсюда следует, что имеется оптимум водосодержания. Этот факт подтверждается известной работой Н. А. Попова по изучению легких бетонов.
Для определения оптимальной водной добавки, обеспечивающей оптимальную подвижность древесно-цементных масс, был предложен прибор, действующий по принципу выжимания влаги из массы посредством ее вибрирования с пригрузкой (вибровыжимание). При этом способе подвижность массы характеризуется временем вибровыжимания в секундах.
Прибор состоит (рис. 79,а) из виброплощадки с вертикально направленными колебаниями, цилиндра (рис. 79,б) со скошенными краями у основания и с латами для крепления прибора к виброплощадке, вкладыша весом 1,5 кг (рис. 79,в).
Для получения показателей на приборе отвешивается порция древесно-цементной массы (100 г), взятой как средняя проба от всего замеса, и закладывается в цилиндр прибора, после чего сверху ставится вкладыш (пригрузка). В момент пуска виброплощадки включается секундомер, а в момент появления обильной влаги (молока вяжущего) вокруг основания цилиндра, секундомер выключается. Количество секунд с момента пуска до появления влаги является «показателем подвижности». Показатель подвижности, характеризующий массу оптимальной удобоукладываемости, можно назвать «показателем оптимальной подвижности». Для получения точных показаний на приборе нужно иметь не меньше трех отсчетов, за окончательный показатель следует взять среднее арифметическое из них.
В самом начале работы необходимо найти свойственный этому приберу «показатель оптимальной подвижности», который определяют опытным путем: для какой-либо древесно-цементной массы изготовляют образцы с различными водовяжущими отношениями при постоянной работе уплотнения. Состав, показавший наименьший коэффициент выхода, является оптимальным, а соответствующий этому составу .показатель подвижности в секундах является «показателем оптимальной подвижности».
Как показали опыты, проведенные во ВНИИНСМе, для каждого прибора может быть получен универсальный показатель оптимальной подвижности, действительный для всех древесноцементных масс, независимо от расхода и вида вяжущего.
При нижеследующих технических характеристиках вибро-площадки: частота колебаний — 2850 кол/мин; кинетический момент — 3,77 кг/см; возмущающая сила — 380 кг; средняя амплитуда колебаний — 0,4 мм; вес вкладыша — 1,5 кг; внутренний диаметр цилиндра — 50 мм; «показатель оптимальной подвижности» равнялся 12—15 сек. для всех исследуемых древесно-цементных масс, для всех составов по жирности (от 1:1,5 до 1:7 — древесные частицы: вяжущее, по весу) и для всех видов минеральных вяжущих.
Изучение влияния основных производственных факторов на прочность опило- и стружкобетонов показало, что химический фактор — фактор взаимодействия древесины с цементом, — проявляемый в первые сутки твердения, приобретает из-за большой поверхности опилок и дробленой стружки еще большее значение, чем при производстве цементного фибролита. Из данных табл. 33 видно, что из опилок в те же сроки выделяется в 2—3 раза больше экстрактивных веществ, чем из древесной шерсти, изготовленной из той же древесины.
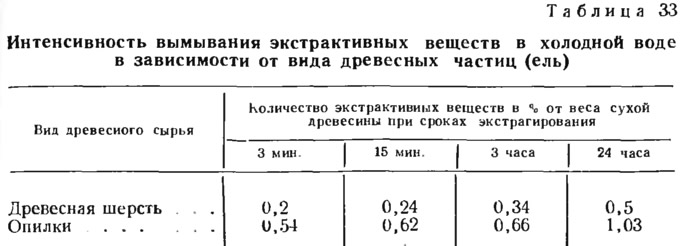
С точки зрения удобоуплотняемости лучше применять опилки и стружку влажностью 25—30%; однако с точки зрения локализации цементных ядов их следует перед использованием хранить на воздухе слоем до 0,5 м. Желательно производить перелопачивание отхода 1 раз в 2—3 дня.
Изучение влияния крупности древесных частиц показало, что при жирных составах крупность частиц не влияет на прочность бетонов (вяжущее имеется в избытке); при тощих составах использование, например, опилок поперечной резки приводит к снижению прочности в связи с резким увеличением общей поверхности опилок в условиях недостатка вяжущего.
Изучение фактора работы уплотнения показало следующее (рис. 80).
1. Увеличение работы уплотнения сдвигает оптимум водосодержания в сторону уменьшения В/Ц, правда, в значительно меньшей степени, чем для обычных легких бетонов.
2. Эффект от увеличения пригрузки с 10 г/см2 до 150 г/см2 при уплотнении масс вибрированием является незначительным; это говорит о том, что пригрузка в 10—20 г/см2 вполне достаточна.
3. С увеличением работы уплотнения увеличивается зона оптимума, т. е. кривая В/Ц становится более пологой.
Изучение влияния водоцементного фактора (рис. 81) для опилобетонов различных составов показало следующее.
1. Кривые В/Ц для опило- и стружкобетонов имеют тот же вид, что и аналогичные кривые для легких бетонов на пористых минеральных заполнителях.
2. Прочностные показатели образцов при изменении водоцементного отношения меняются в широком диапазоне.
3. По мере уменьшения расхода вяжущего кривые В/Ц становятся более пологими (аналогичное явление характерно для всех бетонов).
4. Из-за большой водопоглощающей способности древесных частиц водопотребность тощих составов намного больше, чем жирных.
Изучение фактора расхода и активности вяжущего выявило зависимость между этими факторами и прочностью, что иллюстрируется рис. 82,а. Из графиков видно, что увеличение расхода вяжущего на единицу объема изделия вызывает приблизительно пропорциональный рост прочности. Если по оси абсцисс откладывать расход вяжущего на единицу веса заполнителя (рис. 81,б), то тогда получается еще более чистая пропорциональная зависимость прочности от расхода вяжущего. Изменение активности вяжущего или изменение способа обработки заполнителя (минерализации) вызывает изменение угла наклона кривой на графике (рис. 82,в). Чем жирнее состав (т. е. чем больше расход вяжущего), тем значительней эффект от увеличения активности вяжущего. Чем больше активность вяжущего, тем больше угол наклона прямой к оси абсцисс.
Таким образом, опило- и стружкобетоны в отношении влияния активности вяжущего и его расхода на прочность ведут себя так же, как и легкие бетоны, и подчиняются тем же закономерностям, какие были установлены Н. А. Половым для легких бетонов.
Построены зависимости оптимального водосодержания от состава (рис. 83,а) и от расхода вяжущего на 1 м3 материала (рис. 83,б).
Это позволяет рекомендовать способ подбора состава опило- и стружкобетонов. Подбор состава заключается в изготовлении и испытании образцов трех — четырех составов с предварительно выявленной оптимальной водной добавкой. Строят три кривые (рис. 84): кривая зависимости оптимального водовяжущего отношения от расхода вяжущего, кривая зависимости водовяжущего отношения от состава, кривая прочности при сжатии при оптимальных ВЩ.
Приводим пример подбора состава опилобетона по заданной прочности изделия. Требуется подобрать состав известково-цементного опилобетона с пределом прочности при сжатии 10 кг/см2 и объемным весом 550 кг/м3. Тогда:
- а) по рис. 84,а определяем, что для получения прочности на сжатие 10 кг/см2 при марке цемента 400 необходимо израсходовать 300 кг вяжущего на 1 м3 бетона;
- б) по рис. 84,6 определяем оптимальную водную добавку В/Ц при расходе цемента 300 кг на 1 м3 изделий; водовяжущее отношение будет равно 2;
- в) по рис. 84,в находим нужное соотношение вяжущего и заполнителя; оно будет равняться 1:1,15 (опилки:вяжущее, по весу).
Производство опило- и стружкобетонов
Технологический процесс производства опило- и стружкобетонов состоит из нижеследующих операций:
- а) измельчения и сепарации древесных частиц по фракциям;
- б) минерализации древесных частиц;
- в) смешивания минерализованных древесных частиц с вяжущими;
- г) добавления к цементно-древесной массе песка и смешивания с ним (при производстве изделий повышенной прочности);
- д) наполнения пресс-форм и уплотнения (без набора в пакеты);
- е) твердения изделий;
- ж) механической обработки по размерам и сушки изделий.
Требуемая фракция древесных частиц определяется видом изготовляемых изделий. Неоштукатуренные изделия должны иметь предельный размер частиц не свыше 15 мм, а оштукатуриваемые — не свыше 25 мм. Минимальный размер древесных частиц — 5 мм. Опилки обычно нуждаются только в отсеве излишне мелких частиц. Станочная стружка подвергается дроблению и затем просеиванию и фракционированию.
Древесные отходы хранят в сухом проветриваемом помещении (рис. 85,а), откуда их пневматическим способом или с помощью скребкового транспортера направляют в сепаратор. Применяют сепараторы барабанного или плоского типа. Остатки с сит поступают пневмотранспортом в отдельные закрома. Стружку, не прошедшую через крупную сетку, отправляют на повторное измельчение. Из закромов стружки или опилки подают пневмотранспортом на минерализацию и смешивание.
Минерализация древесных частиц производится сернокислым глиноземом и известковым молоком или хлористым кальцием. Концентрированные растворы минерализаторов приготовляют в специальных резервуарах, откуда их перекачивают в расходные баки, а затем подают на минерализацию. Расходный бак известкового молока должен иметь перемешивающее устройство.
Минерализация производится в том же смесителе, где перемешиваются древесные частицы с цементом. Смеситель представляет собой вертикально установленный металлический цилиндр (рис. 85,б), опирающийся и вращающийся на шарикоподшипнике. Сверху имеется люк для подачи древесных частиц, минерализаторов и цемента, а на дне цилиндра — отверстие для выгрузки готовой смеси. Затвор (шибер), перекрывающий это отверстие, открывается и закрывается при помощи рычагов. Внизу, снаружи цилиндра, установлен зубчатый венец цепной передачи привода, вращающего цилиндр. Внутри цилиндра вращаются лопасти в направлении, обратном вращению корпуса, обеспечивающие лучшее перемешивание.
После загрузки в смеситель определенного количества стружки или опилок туда подают сернокислый глинозем, а затем известковое молоко. По окончании минерализации, проводимой в течение 1—2 мин., в смеситель поступает цемент. На крупных предприятиях его подают пневматически, на мелких же загружают вручную в бункер скипа. Смешивание минерализованной увлажненной стружки или опилок с цементом длится 1,5—2 мин., после чего готовую смесь выгружают через нижний затвор в приемник.
В случае необходимости получения материала повышенной прочности минерализацию осуществляют в чанах или бассейнах с наклонными стенами для обеспечения стока излишка раствора минерализатора из древесных частиц во время их выемки из бассейна. Стружку или опилки насыпают в бассейн, перемешивают в растворе в течение 1—2 мин., а затем извлекают сетчатыми ковшами. После стока излишка раствора минерализованные частицы засыпают в мешалку, где они смешиваются с цементом.
После того как древесные частицы покрываются цементом, в мешалку добавляют песок и, если нужно, воду. Песок заполняет пустоты между древесными частицами, придает бетону большую плотность, что увеличивает прочность и облегчает формование изделий. При использовании тонкой и мелкой стружки или опилок песок вводят в цементно-древесную массу в объемном соотношении 6:1 (масса:песок); с повышением требований в отношении прочности изделий количество вводимого песка увеличивается.
Плиты формуют в следующем порядке. Металлический или фанерный поддон, слегка смазанный щелочью для предотвращения прилипания цементно-древесной массы, устанавливают на стол рольганг. На поддон ставят металлическую разборную рамку, также слегка смазанную изнутри. Пресс-форма наполняется цементно-древесной массой и проталкивается на роликах дальше, где масса разравнивается лопатками и утрамбовывается по периметру и по углам. Затем форма проталкивается под пресс, где масса спрессовывается до высоты, фиксируемой ограничителем. Рычаг или винт, поднимаясь в исходное положение, поднимает крышку, и открытая пресс-форма с опрессованной массой выталкивается по роликам из пресса. Потом металлическую рамку снимают, а поддон с плитой уносят на площадку и укладывают для твердения, которое длится 4—7 дней, в зависимости от температуры воздуха в цехе.
Этим же способом формуют полые плиты. По торцам рамки имеются круглые отверстия, в которые вкладывают трубы.
Цементно-древесная масса трамбуется между трубами и по периметру еще более тщательно После прессования вынимают сначала трубы, затем снимают боковины пресс-формы и поддон с плитой относят на площадку для твердения.
Для формования пустотелых блоков применяют специальный вибростол с пригрузом (рис. 85,е). Свежеотформованный пустотелый блок на поддоне по транспортеру подают на стеллажи для твердения.
Изделия формуют также в стальных формах. Последние заполняют массой и вибрируют их с пригрузкой в 10—20 г/см2 на вибростоле при частоте 3500—4000 колебаний в минуту и амплитуде 0,4—1 мм. Частота колебаний зависит в основном от величины частиц заполнителя: чем крупнее частицы, тем выше частота. По мере оседания массы, во время вибрирования, добавляют новые порции до полного заполнения формы. После вибрирования в течение 1/2 мин. форма с отпрессованным изделием ставится на ровный пол и ее боковины снимаются. Съем боковин производится осторожно, во избежание порчи изделия. После 4—7-дневного твердения в помещении изделия выдерживают на складе в течение 28 дней.
Масса после снятия пригрузки обычно разбухает на 1—2 мм (в основном по направлению прессования), причем величина разбухания зависит от степени уплотнения, упругости древесных частиц и т п.
Для придания блокам стандартных размеров обрабатывают их поверхности с помощью устройства типа двухшпиндельных деревообрабатывающих фрезерных станков. Вместо стальных фрез на шпиндели устанавливают абразивные круги. Один шпиндель поставлен в подшипниках, неподвижно закрепленных в станине станка, а другой в подшипниках, закрепленных в суппорте, передвигающемся в горизонтальном направлении. Просвет между абразивами, соответствующий размеру обрабатываемого блока, регулируют передвижением суппорта Каждый шпиндель снабжен индивидуальным электродвигателем. К этому станку подводится гусеничный звеньевой транспортер. Последний расположен перпендикулярно к оси станка и проходит в просвете между абразивами. Пустотелый блок, подлежащий обработке, укладывается плашмя на звено двигающегося транспортера, который продвигает его к просвету между точильными камнями. Станочник подводит рычагом подвижной суппорт до заданного размера обрабатываемого блока, обтачивая его с торцов.
Складирование изделий производится на открытом воздухе (рис. 86).
Применение стружкобетонов в строительстве
За рубежом изоляционные плиты из стружкобетона выпускаются двух видов: а) неоштукатуренные шириной 50 см, длиной 100 и 150 см и толщиной 3; 5; 7 м 10 см; б) оштукатуренные шириной от 30 до 85 см, длиной 100; 150; 270; 300 см и толщиной 5, 7 и 10 см. Плиты используют в качестве звукоизоляционных прокладок в конструкции пола, а также для устройства накатов балочных перекрытий и перегородок. Плиты снабжены гребнем и пазом. Выпускаются также изоляционные неоштукатуренные плиты больших размеров, армированные деревянными рейками.
Стеновые пустотелые блоки из стружкобетона выпускают за рубежом 2 размером 25x50 см при толщине 15; 20; 25 и 30 см. Изготовляют также специальные блоки, например, соединительные и угловые, обеспечивающие кладку углов, примыкание внутренних стен, перекрытий. Стеновые блоки снабжены гребнем и пазом. Толщина стенки пустотелого блока 4—5 см. Внутренняя перегородка блока делается не на полную высоту.
Строительство за рубежом многоэтажного дома из стружкобетонных блоков показано на рис. 87. После выкладки каждых новых двух рядов блоков пространство между ними заливается легким бетоном, а на наиболее ответственных участках стен (точка опоры балок перекрытий, примыканий внутренних стен к углам и т. д.) этот бетон армируется.
Помимо стеновых блоков, за рубежом изготовляют также пустотелые оштукатуренные стеновые плиты размером в плане 50x141 см и толщиной 10 см (включая наружный штукатурный слой 8 мм и внутренний слой гипсовой штукатурки 6 мм).
Такими плитами заполняют металлические, деревянные или железобетонные стеновые каркасы жилых и промышленных зданий. С внутренней стороны шов закрывают накладными рейками, а иногда, наоборот, подчеркивают скосом углов плит. При малоэтажном строительстве стеновые плиты обычно укладывают горизонтально, при многоэтажном и промышленном строительстве — вертикально. Приемы крепления стеновых плит по каркасу показаны на рис. 88 и 89.б. Необходимо отметить, что плиты ввиду их подвижности не следует ставить вплотную друг к другу или к элементам каркаса. Общий вид стены показан на рис. 89,а.
За рубежом выпускают также многопустотные стружкобетонные плиты-вкладыши для монолитных железобетонных перекрытии и различные армированные плиты длиной до 3,5 м для укладки по балкам перекрытий и покрытий (рис. 90, 91, 92).