В различных литературных источниках содержатся данные о влиянии добавок на физические и химические свойства материалов на жидкостекольном вяжущем. Однако, в результате того, что исследовались материалы различных физико-химических составов, а также использовались различные режимы их обработки, эти данные неудобны для сопоставления.
Последнее обстоятельство станет совершенно очевидным, если учесть, что даже изменение модуля жидкого стекла или его удельного веда может привести к резкому изменению свойств материала, полученного на его основе. К таким же результатам приводит применение различных заполнителей, режимов хранения и тепловой обработки.
Для получения сопоставляемых результатов и исключения влияния физических и химических качеств различных заполнителей и других факторов на результаты испытаний принималась шихта одного состава: песок речной 90%; песок речной вибромолотый — 10%; жидкое стекло с модулем 2,5 и удельным весом 1,5 в количестве 10% по весу (считая на сумму речного и вибромолотого песка).
В целях приближения условий хранения образцов к производственным последние хранились при температуре 10±5° и относительной влажности воздуха 70±10%.
Определялся только предел прочности при сжатии, для чего испытывались кубики размером 2X2X2 см. Испытания производились на пятитонном прессе.
В виде добавок применялись широко распространенные химикаты, вяжущие и отходы промышленных производств.
Растворимые в воде добавки вводились в измельченном состоянии или в виде растворов. Сроки испытаний образцов приняты следующие. Сразу по изготовлении испытывались образцы, подвергавшиеся сушке в сушильном шкафу при температуре 150—200° в течение двух часов. Остальные образцы испытывались через 10; 40; 180 дней воздушного хранения. Сроки 10 и 40 дней были приняты из соображений длительности химического взаимодействия жидкого стекла и некоторых применяемых в данных исследованиях добавок.
Состав шихты для всех образцов одинаковый (указан выше).
Влияние добавок на прочность и растворимость материалов на жидкостекольном вяжущем будет сравниваться с показателями прочности образцов из вышеупомянутой шихты без добавок, помещенными в табл. 9.
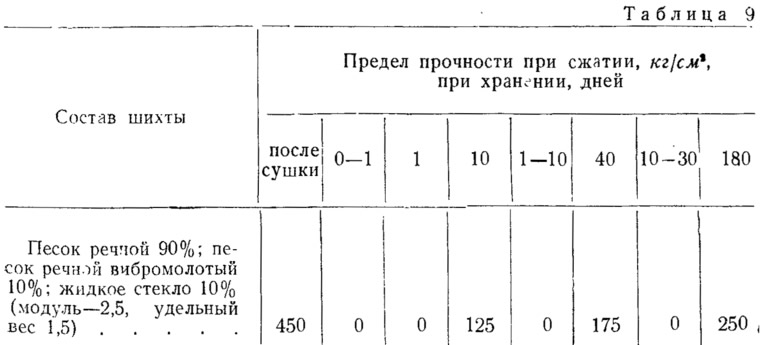
Примечание. Сроки хранения, написанные через тире, обозначают: первая цифра — срок хранения в естественных условиях, после которого образцы погружаются в воду, вторая -— срок испытаний. Сроки, обозначенные одной цифрой, показывают время хранения в естественных условиях.
Влияние окислов металлов
При добавлении к шихте окислов металлов происходит быстрое затвердевание смеси, являющееся результатом взаимодействия между растворимым стеклом и соответствующим окислом в присутствии воды. Согласно установившемуся мнение, реакции между окислами и щелочными силикатами предшествует процесс частичного растворения этих окислов в жидком стекле. Растворившиеся окислы гидратируются раствором щелочного силиката. Затем образовавшиеся гидроокиси, вступая во взаимодействие с жидким стеклом, образуют силикаты соответствующих металлов.
Так, например, реакция между окисью кальция и щелочным силикатом происходит по следующим уравнениям:

Чем большей растворимостью обладает образовавшаяся гидроокись и чем большее содержание в жидком стекле SiO2, тем быстрее происходит реакция. Повышение температуры способствует ускорению реакции.
Аналогично происходит реакция между окислами трехвалентных металлов, а также между портландцементом и основными доменными шлаками. В последнем случае предполагают, что реакция происходит между щелочными силикатами и основными окислами и в частности с СаО. По мнению автора, такое предположение не отражает в полной мере существо происходящей химической реакции, что будет показано ниже.
При добавлении к шихте гидроокисей щелочноземельных металлов Ва(ОН)2, Са(ОН)2, Mg(ОН)2 также происходит заметное ускорение твердения смеси, что, вероятно, является результатом химической реакции, происходящей по уравнению

Согласно этому уравнению, в результате взаимодействия жидкого стекла и гидроокисей щелочноземельных металлов образуются соответствующие гидросиликаты.
В табл. 10 приведены некоторые данные об изменении прочности образцов в зависимости от добавления в шихту окисей и гидроокисей металлов.
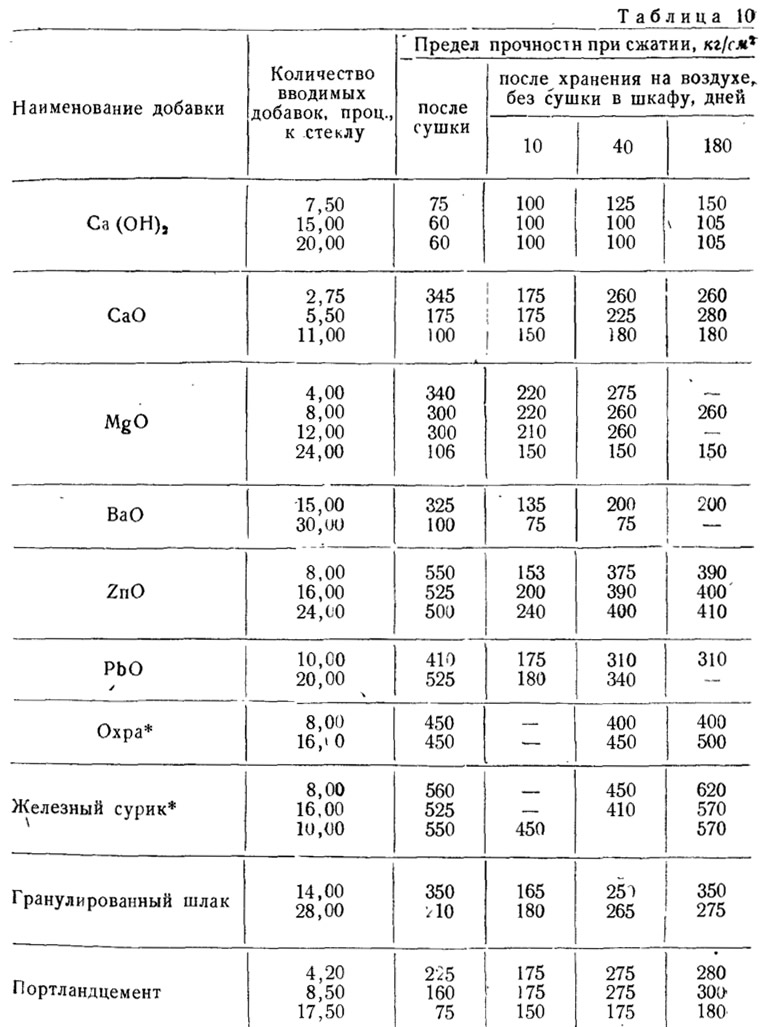
Примечания: 1. Для испытания взята шихта состава: песка речного 90%; песка речного вибромолотого 10%, жидкого стекла с модулем 2,5 и удельным весом 1,5 10%.
2. Сушка производилась в сушильном шкафу в течение двух часов,, с подъемом температуры до 150—200°.
3. Образцы составов, помеченных звездочкой, подвергались двухчасовой сушке, после чего хранились до испытаний на воздухе.
На основании результатов испытаний (см. табл. 9, 10) можно сделать вывод, что окислы различных металлов оказывают различное влияние на прочность образцов.
Почти во всех случаях при введении в шихту окислов щелочноземельных металлов прочность образцов изменяется в зависимости от количества вводимой добавки. С увеличением содержания добавки в шихте прочность падает.
Добавка ZnO, PbO и окислов трехвалентных металлов увеличивает в определенных пределах прочность материала.
Сушка в зависимости от качества и количества вводимых добавок оказывает различное влияние на прочность образцов. В ряде случаев в результате кратковременной сушки можно получить прочность образца, превышающую его прочность в шестимесячном возрасте при хранении в естественных условиях.
Следует полагать, что со временем прочность образцов, хранившихся в естественных условиях, сравняется с прочностью образцов, подвергавшихся кратковременной сушке.
С увеличением содержания окислов щелочноземельных металлов сушка дает худшие результаты и даже приводит к значительной потере прочности.
Продолжительность сушки также оказывает заметное влияние на прочность и водостойкость образцов. Сушка, независимо от ее продолжительности, увеличивает водостойкость образцов. С увеличением продолжительности сушки образцов возрастает их водостойкость. Так, прочность образцов указанного состава с добавкой 8% ZnO, погруженных в воду на двое суток, после сушки в течение двух часов показала при сжатии 300 кг/см2, а после сушки в течение одного часа 200 кг/см2.
Аналогичным образом изменялась прочность образцов других составов в зависимости от длительности сушки при водном хранении.
Однако максимальной прочности образцы достигают в первые 2—4 часа сушки. В дальнейшем эта прочность остается неизменной или несколько понижается.
В большинстве случаев прочность при длительной сушке падает у образцов с большим содержанием добавки. Так, например, прочность при сжатии образцов из шихты указанного состава с добавкой 8% ZnO после двухчасовой и шестнадцатичасовой сушки составляет 550 кг/см2, прочность образцов из шихты указанного состава с добавкой 24% ZnO после двухчасовой сушки — 500 кг/см2, а после шестнадцатичасовой — 25 кг/см2.
Значительное повышение водостойкости образцов может быть достигнуто путем кратковременной сушки и пропитки.
При сушке образцов с добавкой 8% ZnO в течение 1—2 часов и последующей их пропитке в течение часа в горячем растворе CaCl прочность остается неизменной, а потери прочности при водном хранении не превышают 10—15%.
Примерно такие же результаты могут быть получены в том случае, если сушке предшествует пропитка.
В некоторых случаях целесообразно хранить образцы во влажных условиях.
При изготовлении образцов добавки в виде порошка перемешивались с заполнителем, после чего шихта смешивалась с жидким стеклом, как это обычно делается при изготовлении материалов на жидкостекольном вяжущем.
Однако вследствие малой растворимости окислов в жидком стекле при таком порядке перемешиванияих химические свойства используются не полностью, что оказывает влияние на полноту и длительность происходящей реакции.
В результате этого образцы воздушного хранения даже через 40 дней после изготовления оказались неводостойкими, а образцы, подвергшиеся сушке, обладали недостаточной степенью водостойкости. При изменении последовательности смешивания компонентов и создании условий для лучшей растворимости окислов могут быть получены более водостойкие материалы. Подробно об этом будет сказано в разделе «Пеногрунтосиликаты».
Влияние солей щелочных металлов
При добавлении к шихте солей щелочных металлов в результате их взаимодействия с жидким стеклом происходит быстрое твердение смеси.
Можно предположить, что при взаимодействии двухмодульного жидкого стекла с кремнефторидом натрия реакция происходит по уравнению

При увеличении модуля стекла реакция несколько усложняется вследствие наличия кремнезема, коагулирующего в кремнегель совместно с SiO2, который выделяется при разложении мета- и дисиликата натрия.
М. А. Матвеев и В. П. Дятлов на основании проведенных исследований пришли к выводу, что Na2SiF6 и щелочные силикаты частично вступают между собой в химическую реакцию, а частично образуют твердые растворы.
Взаимодействие щелочных силикатов с бикарбонатами объясняется образованием кислот.
В табл. 11 приведены показатели прочности образцов при сжатии в случае введения в шихту различных количеств солей щелочных металлов.
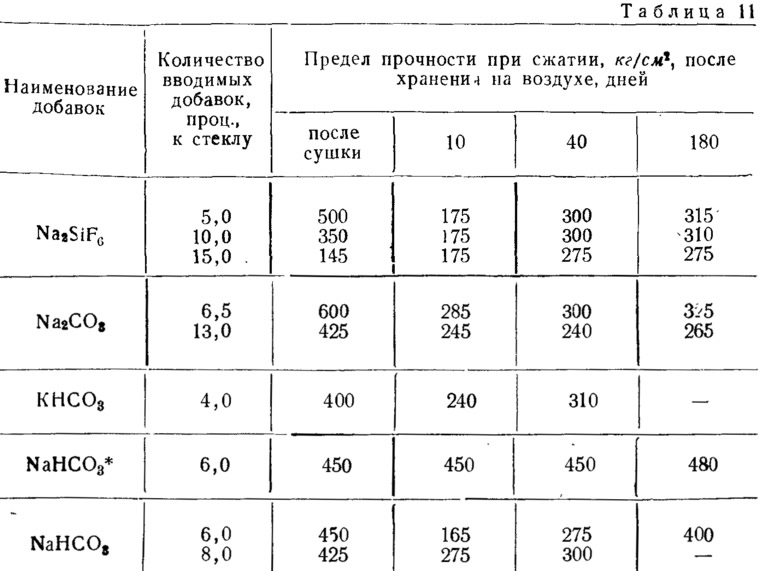
Примечания: 1. Для испытания взята шихта состава: песка речного 90%; песка речного вибромолотого 10%; жидкого стекла с модулем 2,5 и удельным весом 1,5 10%.
2. Сушка производилась в сушильном шкафу, в течение двух часов, с подъемом температуры до 150—200°.
3. Образцы составов, помеченных звездочкой, подвергались двухчасовой сушке, после чего хранились до испытаний на воздухе.
Сопоставив результаты испытаний, приведенных в табл. 9 и 11, можно сделать вывод, что соли щелочных металлов оказывают существенное влияние на быстроту нарастания прочности образцов и их прочность.
С увеличением процентного содержания этих солей в шихте прочность образцов несколько падает. Добавка в шихту солей щелочных металлов повышает водостойкость образцов. Более значительное повышение водостойкости наблюдается при применении сушки.
Влияние растворимых солей щелочноземельных металлов
Взаимодействие жидкого стекла с растворимыми солями щелочноземельных металлов объясняется различными исследователями по разному.
А. Я. Тихонов на основании многочисленных исследований утверждает, что упомянутая реакция идет в направлении постепенного образования гидросиликата соответствующего щелочноземельного металла по уравнению

Такое направление химического процесса подтверждается опытами Ле-Шаталье и В. Н. Юнга.
В. А. Каргин, С. А. Кац и А. Ф. Комовский на основании проводимых исследований утверждают, что в результате этой реакции образуются осадки гидроокисей щелочноземельных металлов и гель кремнезема:

М. А. Матвеев высказывает предположение, что гидроокись металла — Са(ОН)2 — является промежуточным продуктом реакции, а конечным продуктом все же является гидросиликат металла и гель SiO2.
Некоторые продукты реакции, получаемые в первом и втором случаях, должны полностью или частично подвергаться гидролизу при обработке изделий горячей водой или другими видами тепловлажностной обработки, и прочность их должна резко снижаться. Однако в результате длительной обработки изделий в кипящей воде в пропарочной камере или автоклаве прочность образцов почти не снижается, а в некоторых случаях повышается. Поэтому можно предположить, что продукты реакции являются более сложными соединениями, чем это предполагается в указанных уравнениях. Следует обратить внимание на очень быстрое образование этих соединений, о чем свидетельствует тот факт, что образцы подвергались вышеперечисленным видам тепловлажностной обработки сразу после их получасовой или часовой пропитки в горячем растворе хлористого кальция, сохраняя при этом прочность.
В табл. 12 приведены показатели прочности при сжатии образцов, подвергавшихся пропитке в горячих и холодных растворах солей щелочноземельных металлов и Al2(SO4)3.
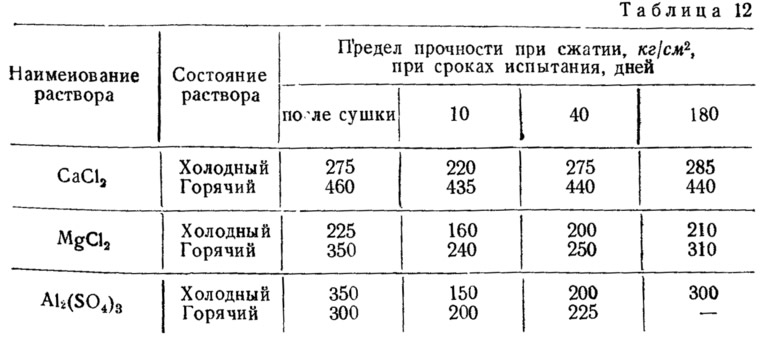
Примечание. Для испытания взята шихта состава: песка речного 90°; песка речного вибромолотого 10%; жидкого стекла с модулем 2,5 и удельным весом 1,5 10%.
Образцы погружались в растворы солей с удельным весом 1,3—1,35 на различные сроки. В холодных растворах образцы выдерживались 1—48 часов, а в горячих 0,5—3 часа.
Пределы прочности образцов при сжатии оказались примерно одинаковыми, независимо от срока пропитки.
Как видно из табл. 12, прочность образцов значительно увеличивается при пропитке их в горячих растворах. Эти образцы имеют более высокую степень водостойкости.
Образцы, пропитываемые в холодных растворах, отличались пониженной прочностью и обладали меньшей водостойкостью.
Сравнительно низкая прочность образцов, пропитанных раствором Al2(SO4)3, могла быть получена вследствие неполной их пропитки в результате быстрого взаимодействия Al2(SO4)3 с жидким стеклом. Производилась также пропитка образцов, подвергшихся сушке и хранению в естественных условиях, кислотами (серной, уксусной, соляной, фенольной и др.) и растворимыми солями металлов. Во всех случаях водостойкость образцов увеличивалась. Прочность образцов в значительной мере зависела от температуры йропитки, удельного веса раствора и способов хранения образцов после изготовления.
С целью определения степени растворимости в воде вяжущего, состоящего из жидкого стекла и добавок (гранулированного доменного шлака, цемента, извести-пушонки и кипелки, золы-уноса, известняка), а также возможности твердения его под слоем воды проведен следующий опыт.
Жидкое стекло, замешанное с соответствующей добавкой, помещалось в стеклянный сосуд. В результате наблюдений установлено следующее.
Жидкое стекло с силикатными модулями 2 и 2,5 при замешивании с вибромолотым гранулированным шлаком, добавленным в количестве 40% от веса стекла, образует однородную, постепенно твердеющую массу черного цвета.
Жидкое стекло с модулем 3,5 и таким же количеством гранулированного шлака в процессе твердения образовало слоистую массу из нижнего слоя черного цвета и верхнего — гелеобразной, массы, очень медленно набирающей прочность и постепенно покрывающейся трещинами.
После 60-дневного хранения в естественных условиях и 30-дневного хранения в воде, смеси на стекле с модулем 2 и 2,5 сохранили прочность, а у смесей на стекле с модулем 3,5 верхний слой размок, нижний остался твердым, но менее прочным.
Увеличение добавки гранулированного шлака привело к ускорений процесса твердения, но в целом картины не изменило.
При погружении упомянутых смесей жидкого стекла и гранулированного шлака сразу после их смешивания в воду в первых двух случаях они затвердели под водой, а при модуле стекла 3,5 образовавшийся осадок затвердел со временем, покрывшись сверху студнеобразной непрочной массой.
При замешивании жидкого стекла с добавкой 20% портландцемента марки 400 результаты получены те же, что и в предыдущем случае. Однако образовавшаяся масса темно-серого цвета обличалась меньшей прочностью и большей хрупкостью.
При замешивании жидких стекол разной модульности с добавкой СаО и Са(ОН)2 (добавлялись в эквимолекулярных количествах) однородная, прочная, водостойкая масса получена при добавке к стеклу с модулем 2,5 СаО. При добавке Са(ОН)2 масса оказалась более хрупкой. Масса, замешанная на стекле с модулем 2 при добавке СаО или Са(ОН)2, оказалась менее водостойкой, ат масса, замешанная на стекле с модулем 3,5, расслоилась и в результате обработки водой сохранила прочность только в нижнем слое.
Добавка мела к жидкому стеклу с модулем 2 приводит к образованию прочной водостойкой массы. При более высоком модуле жидкого стекла Полностью затвердевшие при хранении на воздухе смеси размокают.
Массы, образованные путем перемешивания жидкого стекла с золой-уносом не водостойки. Смеси золы-уноса и жидкого стекла с модулем 2 при водном хранении теряют прочность медленнее, чем при более высокомодульных стеклах. При хранении такой смеси в естественных условиях в течение 60 дней и в воде 30 дней разрушающему действию воды подвергся только тонкий наружный слой. В то же время при более высоких модулях стекла смеси полностью теряют способность сохранить форму.
Несмотря на то, что не удалось установить количественных изменений прочности исследуемых образцов, была получена возможность убедиться в качественной неизменяемости некоторых смесей при хранении в воде (сохранение твердой фазы), а также в возможности их твердения во влажных условиях.
Впоследствии количественные изменения прочностных характеристик были установлены путем сравнения показателей прочности при сжатии образцов, изготовленных на цементном вяжущем, гранулированном шлаке и на двухкомпонентных вяжущих на основе жидкого стекла с добавками гранулированного шлака и цемента.
Образцы изготовлялись из пластичных растворов с водовяжущим отношением 0,6. Один килограмм портландцемента марки 400 приравнивался одному килограмму жидкого стекла модуля 2,33 с удельным весом 1,5. Добавка в виде шлака и портландцемента бралась сверх веса основного вяжущего. Заполнителем во всех случаях служила супесь.
Соотношение между вяжущим и заполнителем по весу выбиралось таким, чтобы во всех случаях количество твердого вещества с учетом заполнителя и добавок было одинаковым и равнялось 3: 1. Все составы содержали одинаковое количество воды.
Соотношение по весу между жидкостекольным вяжущим и, добавками приняты следующие:
- жидкое стекло: вибромолотый гранулированный шлак = 1:0,5;
- жидкое стекло: портландцемент = 1:0,2.
Перемешивание массы на жидкостекольном вяжущем производилось в следующем порядке. При быстром перемешивании разведенного водой жидкого стекла постепенно всыпался заполнитель и добавка. После получения однородной массы смесь наливалась в формы. Перемешивание цемента и шлака с водой и заполнителем производилось обычным порядком. Распалубка образцов на вяжущем жидкое стекло+цемент производилась через 1 час после заливки в формы, на вяжущем жидкое стекло+ранулирсванный шлак — через 8 часов, на цементном вяжущем через 24 часа, на гранулированном шлаке через 72 часа.
Часть образцов сразу после изготовления ставилась в формах в воду. Образцы водного режима хранения погружались в воду через сутки после освобождения от форм.
В табл. 13 приведены результаты испытаний на сжатие кубиков размером 7,07X7,07X7,07 см из упомянутых масс.
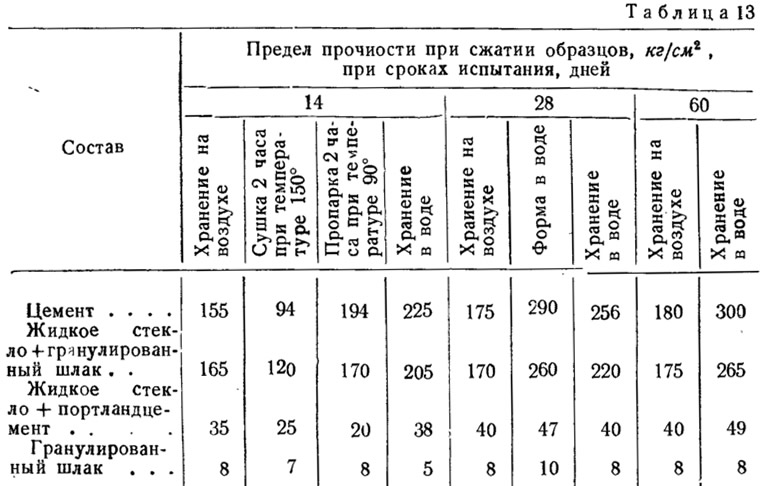
Примечание. В графе «Состав» указано только наименование вяжущего и добавок.
На основании данных табл. 13 можно сделать вывод, что путем введения в жидкое стекло добавки гранулированного шлака можно получить вяжущее, твердеющее в воде. Кроме того, изделия на этом вяжущем, в целях ускорения процесса твердения, могут подвергаться всем видам тепловлажностной обработки.
Результаты дальнейших исследований образцов на жидкостекольном вяжущем (с силикатным модулем 2 и выше) с добавкой гранулированного шлака позволяют сделать вывод, что с увеличением модуля стекла способность образцов набирать прочность в воде уменьшается. С увеличением добавки гранулированного шлака образцы на высокомодульном жидком стекле со временем приобретают водостойкость.
Нарастание прочности при хранении на воздухе в образцах на низкомодульном жидком стекле в первое время идет значительно быстрее, чем на высокомодульном.
Так, при замешивании овражного песка с 10% жидкого стекла (силикатный модуль 2 и удельный вес 1,4) с добавкой 10% гранулированного шлака через два часа после формовки прочность образцов при сжатии составляет 20—30 кг/см2, через сутки 80—90 кг/см2, а вибрированных при формовке 100—150 кг/см2. Прочность образцов того же состава на жидком стекле с силикатным модулем 3,5 в пять-восемь раз меньше.
В дальнейшем нарастание прочности при хранении в естественных условиях на жидком стекле с более высоким модулем идет интенсивней, чем на низкомодульном.
С увеличением содержания гранулированного шлака в шихте увеличивается скорость нарастания прочности в образцах.
Способность набирать прочность в воде жидкостекольного вяжущего с добавкой гранулированного шлака при прочих равных условиях в значительной степени зависит от содержания в нем едкой щелочи.
Для проверки действия щелочи (NaOH) на вяжущие свойства вибромолотого котельного и гранулированного доменного шлаков, а также портландцемента изготовлены образцы на цементном и шлаковом вяжущем с заполнителем из овражного песка состава 3:1 при водовяжущем отношении 0,35. На каждом вяжущем изготовлено две партии образцов. Одна партия затворялась водой, содержащей 20% NaOH, а вторая — обычной водой. Образцы на шлаковых вяжущих, затворенные, водой без NaOH, при испытании показали ничтожную прочность. В табл- 14 приведены некоторые данные испытаний образцов на вяжущих с добавками щелочи и на цементном вяжущем и обычной воде.
По данным, приведенным в табл. 14, видно, что добавка NaOH к гранулированному шлаку в значительной степени повышает его вяжущие свойства. Проявляются при этом вяжущие свойства и у котельного шлака.
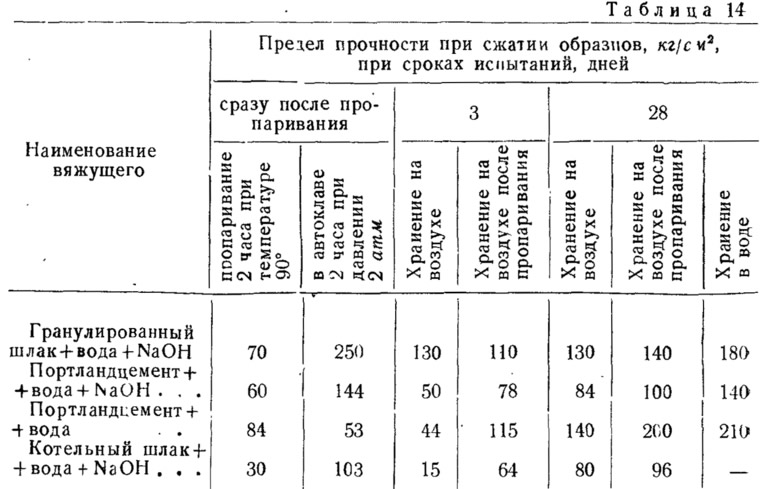
Поэтому следует полагать, что на интенсивность реакции между гранулированным шлаком и щелочными силикатами оказывает влияние не только состав шлаков и содержание SiO2 в жидком стекле, но и содержание щелочи.
Обращает на себя внимание и тот факт, что в образцах на шлаковом и цементном вяжущем при затворении водой, содержащей NaOH, интенсивно нарастает прочность даже при незначительном повышении давления и температуры.
Источник: «Грунтосиликаты», В. Д. Глуховский, 1959