После вылеживания в течение некоторого времени камни вынимают из раствора, высушивают и укладывают в дело.
Рансомом рекомендовалась для камней, пропитанных в растворе хлористого кальция, последующая промывка в холодной воде для удаления образовавшегося в результате реакций хлористого натрия. Такая обработка камней в воде не приводит к повышению их прочности (прочность несколько понижается). Для выщелачивания хлористого натрия в существенных количествах процесс промывки указанным способом должен производиться в течение длительного времени.
По нашему мнению, в целях выщелачивания избытка хлористого кальция, содержащегося в изделиях, а также образовавшегося в результате реакции хлористого натрия и других веществ, изделия после пропитки следует обрабатывать горячей водой, нагретой до температуры кипения или несколько ниже ее, или же паром при атмосферном давлении и температуре 85—95°. В результате такой обработки прочность изделий несколько повышается. Креме того, длительность обработки в этом случае может быть сокращена до 30—120 минут.
Аналогичный прием может применяться и при пропитке изделий другими растворимыми солями.
Некоторые исследователи рекомендуют не пропитывать изделия полностью, а опрыскивать их поверхность раствором хлористого кальция. Следует полагать, что такой способ не всегда может привести к положительным результатам, так как раствор проникает сравнительно на небольшую глубину.
В результате проведенных автором опытов с образцами, пропитанными с поверхности СаСl2, установлено, что изделия, изготовленные таким способом, могут со временем разрушиться совсем или же покрываются трещинами. Это объясняется, очевидно, тем обстоятельством, что пропитанные и непропитанные слои изделия обладают несколько отличными свойствами. В частности, наружный слой вследствие наличия в нем NaCl и избытка СаСl2 обладает некоторой гигроскопичностью. Этим свойством не обладает внутренняя, непропитанная часть изделия. Поэтому при увлажнении изделия даже в результате повышения содержания влаги в окружающей среде могут выйти из строя. Такие изделия теряют прочность при замачивании в течение длительного времени после изготовления в результате проникновения воды через пропитанные слои и размокания в связи с этим непропитанной их части.
На том же принципе взаимодействия жидкого стекла с растворами различных солей основано силикатирование грунтов с целью повышения их несущей способности и водонепроницаемости.
Силикатирование грунтов осуществляется по следующей схеме. С помощью инъекторов в грунт под давлением 30—40 атм и более поочередно нагнетают растворы жидкого стекла и растворимых хлористых солей, щелочноземельных металлов (СаСl2, MgCl2, ВаСl2). Чаще всего для этой цели применяют СаСl2 как наиболее дешевую из перечисленных солей.
Жидкое стекло и хлористый кальций, встречаясь в порах грунта, вступают в химическое взаимодействие, образуя студнеобразный осадок, обволакивающий частицы грунта, и заполняющий промежутки между ними.
Осадки представляют собой сильно обводненные набухшие коллоидные гели, непроницаемые для воды. В сухом грунте отдельные его частицы покрываются тонким слоем цементирующего вещества, состоящего в основном из коллоидного кремнезема. Радиус закрепления грунтов одним инъектором — 0,25—0,75 м в зависимости от их плотности, химического и физического состава и ряда других обстоятельств.
Б. А. Ржаницын, на основании лабораторных исследований, рекомендует для закрепления песчаных грунтов применять жидкое стекло с силикатным модулем 2,7—3, при удельном весе его для сухих грунтов (влажность 5—8%) 1,45, а для водонасыщенных — 1,5. Раствор хлористого кальция рекомендуется применять с удельным весом 1,24—1,28.
Силикатированию описанным способом могут подвергаться песчаные грунты, а также грунты, содержащие глинистые примеси. Изменение прочности просиликатизированного песка в зависимости от модуля жидкого стекла характеризуется данными, приведенными в табл. 4.
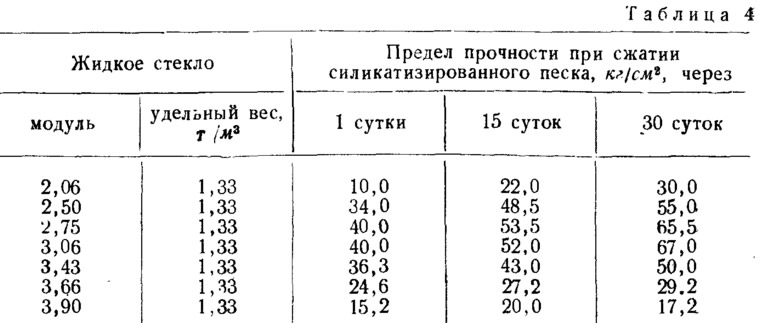
Образцы изготовлялись из люберецкого песка, содержащего 41% фракции 0,5—0,25 мм и 59% фракции 0,25—0,05 мм.
По данным, опубликованным А. И. Жилиным, видно, что примесь глины не влияет на закрепление грунтов (табл. 5). Следует полагать, что такое заключение может быть справедливо только для низкомодульных жидких стекол.

Метод силикатирования грунтов применяется при строительстве метро, для защиты котлованов от проникновения подземных вод, при строительстве различных шахт, тоннелей и др.
Путем попеременной поверхностной пропитки или пропитки под давлением жидким стеклом и растворами упомянутых солей можно увеличить прочность, атмосфероустойчивость и водостойкость, а также химическую стойкость различных природных иискуственных пористых материалов.
При пропитке под давлением в закрепляемом материале пробуривается несколько скважин, через которые нагнетается раствор жидкого стекла и растворимой соли.
При попеременной поверхностной пропитке камни поочередно покрываются растворами солей. Удельный вес растворов постепенно повышается. При этом наружные поверхности могут быть пропитаны на довольно значительную глубину. Вследствие образования отложенных в порах материалов продуктов реакции жидкого стекла и растворимых солей происходит плотное закупоривание пор материала. В результате пропитки значительно улучшаются прочностные характеристики даже сильно пористых материалов — песчаников, изделий из мрамора, штукатурок и др.
Поверхность бетонных конструкций в результате пропитки уплотняется и становится водонепроницаемой, а также покрывается тонкой пленкой толщиной 1—2 мм, прочно пристающей к бетону и предохраняющей его от проникновения агрессивных паров и газов.
Впервые способ химического закрепления грунтов взамен применявшейся цементации был предложен Иостеном в 1926 г. Начало научного обоснования процессов, происходящих в этом случае, было положено М. И. Стаматуи.
Разрешению и дальнейшему развитию этой проблемы в основном содействовали обширные исследовательские работы советских ученых.
Строительство шоссейных дорог на жидкостекольном вяжущем с инертными заполнителями (известняк, доломит, кварцит, песчаник, гранит) основано на способности жидкого стекла образовывать твердые монолитные массы с заполнителями.
Работы, проводимые в этом направлении в различных странах,, в одних случаях дали положительные результаты, а в других—отрицательные. В Италии и особенно во Франции построено тысячи километров силикатированных шоссейных дорог. Германией в этом вопросе не достигнуто положительных результатов.
В нашей стране работы по силикатированию дорог проводились В. М. Шалфеевым и дали удовлетворительные результаты.
Строительство таких дорог может производиться способом силикатного бетона или способом пропитки.
При строительстве способом силикатного бетона рабочая смесь, состоящая из крупного заполнителя, высевок и жидкого стекла,, после тщательного перемешивания укладывается слоем 10 см и уплотняется катками. Через 24 часа масса приобретает достаточную прочность и по ней может двигаться транспорт.
При строительстве дорог по способу пропитки смесь щебня и крупных высевок укладывается в корыто дороги и укатывается. Затем в готовое щебеночное покрытие вводится заранее приготовленная смесь известняковых высевок и жидкого стекла. Можно высевки и жидкое стекло вводить поочередно.
Такие дороги более дешевые, чем бетонные и дороги с другими видами щебеночных покрытий. Они в полтора-два раза долговечнее, чем асфальтовые и бетонные, а также более износо-, водо- и морозостойкие.
В. М. Шалфеевым установлено, что для силикатирования дорог следует применять жидкое стекло с силикатным модулем 3,4—3,5 и удельным весом 1,3. Применение жидкого стекла с более низким силикатным модулем, по его утверждению, дает худшие результаты.
Наиболее подходящим заполнителем являются известняки с объемным весом 2—2,7 г/м3, пределом прочности при сжатии 400—1400 кг/см2 и пористостью не более 4—5%.
Применение твердых известняков в смеси с высевками из более мягких известняков возможно только в случае их неявно выраженной кристаллической структуры. Это объясняется тем обстоятельством, что на процесс силикатизации оказывает влияние пористость заполнителя. Наличие пор ускоряет разложение силиката вследствие явлений диализа через тонкие стенки пор. Щелочь диффундирует через поры, и выделяющийся коллоидный кремнезем прочно сцепляется с поверхностью твердых частиц.
В. М. Шалфеевым установлено также, что даже незначительное количество глинистых примесей в твердых породах действует отрицательно на связующую способность жидкого стекла. На этом основании не рекомендуется применять для силикатирования карьерные пески, всегда содержащие примеси глины.
А. И. Жилин утверждает, что замечание о недопустимости содержания глинистых примесей требует дополнительной проверки, так как противоречит выводам по химическому укреплению грунтов.
По мнению автора, возможность применения песков, содержащих глинистые примеси, зависит от силикатного модуля жидкого стекла. При низкомодульных стеклах глинистые примеси не оказывают вредного влияния. В данном случае при применении жидкого стекла с силикатным модулем 3,5 наличие глинистых примесей даже в небольших количествах приводит к резкому падению прочности покрытия.
Жидкое стекло применяется для ремонта поверхностных частей бетонных сооружений. В этом случае на смоченное водой поврежденное место накладывают слой жидкого стекла с модулем 3,3—3,4, который посыпают порошком цемента. В результате химического взаимодействия между цементом и щелочным силикатом происходит быстрое твердение смеси.
На этом принципе основана пропитка жидким стеклом песчано-цементных изделий и бетонов с целью повышения их прочности, водонепроницаемости, а также защиты от действия растительных масел, жиров и других веществ.
Источник: «Грунтосиликаты», В. Д. Глуховский, 1959