Песок — первый компонент силикальцита.
По химическому составу пески весьма разнообразны. Для ориентации приводим данные по районам Ростовской области (таблица 2).
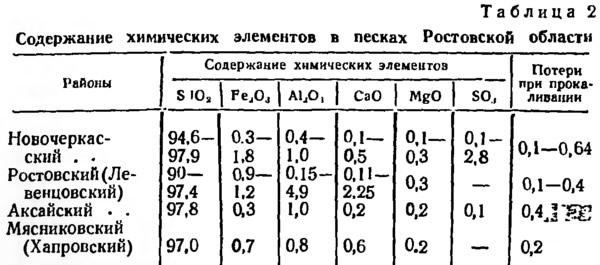
В минералогическом составе песков преобладает кварц, имеются примеси глии -и полевых шпатов.
Физические свойства определяют следующие показатели: цвет, размер и формы зерен, суммарная поверхность песчинок в грамме песка.
Чистый кварцевый песок имеет белый цвет. Примеси придают ему желтоватый, красноватый и другие оттенки.
Размер зерен — в пределах 40—60 микрон и до 4—5 мм. Форма их — острогранная, угловатая, окатанная или округленная.
Суммарную, .или удельную, поверхность песчинок в грамме песка определяют особым прибором — поверхностометром В. В. Товарова. Она характеризует тонину (дисперсность) материала и для естественных песков составляет 70—150 см2/г.
Всесоюзного стандарта на пески для изготовления силикальцита нет. Поскольку их гранулометрический состав и форма зерен при помоле совершенно меняются, то за редким исключением почти все пески годны для производства силикальцитных стройдеталей.
Наличие в песке 10—15% глины не вредно, так как она содержит примерно 60—70% высокодисперсной окиси кремния, а также окись алюминия, которая дает в изделии кальциевые соединения. Присутствие небольшого количества (4—6%) окиси кальция и железа не влияет на качество силикальцита.
О пригодности всех песков для получения силикальцита можно судить по тому, что свыше двухсот проб, присланных на Таллинский завод из самых различных краев Советского Союза, дали после помола в дезинтеграторе полноценный строительный материал, хотя в естественном состоянии многие из них были совершенно непригодны для производства. Все это свидетельствует о том, что основной компонент силикальцита — песок, который входит в шихту в количестве 85—90%, дает возможность повсеместно изготовлять стройдетали.
Известь — второй компонент силикальцита.
Сырьем для производства извести служат различные известковые горные породы, содержащие углекислый кальций (мрамор, плотный и рыхлый известняк, мел, известковый туф, известняк-ракушечник). Все они обычно имеют примеси глины и углекислого магния, количество которых .предопределяет качество получаемой после обжига негашеной извести.
Свойства извести зависят еще от того, как производился обжиг и какая была максимальная его температура. Если процесс проходил неправильно, может быть много недожога или пережога извести.
Обычно при изготовлении силикальцита известь-пушонку вводят в количестве 8—14% (в пересчете на 100% СаО) по весу от общего количества шихты. Чем тоньше помол песка, тем больше требуется извести, так как значительно увеличивается поверхность песка, вступающего в реакцию с окисью кальция.
В зависимости от способа гашения и режима водотермической обработки, известь приобретает свойства, которые ее делают пригодной для силикальцита. Она должна быть погашена так, чтобы при автоклавной обработке в изделиях не было дефектов из-за отсутствия постоянства объема (ГОСТ 1174—51).
Выгоднее пользоваться известью с содержанием окиси кальция 60% и более, окиси магния — до 5% и скоростью гашения — не свыше 30 минут. Незначительное содержание примесей — окислов железа и алюминия — не вредно. Во время водотермической обработки они также реагируют с окисью кальция.
Во всех случаях, когда известь идет на производство силикальцитных изделий, необходимо предварительно в заводской лаборатории установить ее качество и оптимальное количество для ввода в шихту. Обычно лаборатория изучает скорость гашения, химический состав извести (СаО, Fe2O3, Al2O3), содержание окиси магния, количество недожога и пережога.
Скорость гашения извести имеет большое значение, так как процесс должен полностью пройти до загрузки изделий к автоклав. Продолжение гашения в период водотермической обработки приводит к трещинам и другим дефектам из-за увеличения объема «при (переходе СаО в Са(ОН)2.
Гашение извести на силикальцитных заводах производят в гидраторах. Гидратор представляет собой резервуар, работающий при давлении пара 5 ати. В него подают дробленую известь, пар /и воду. Время гашения — 40—60 минут. Для ускорения реакции гидратор вращают. Получают известь большой дисперсности. В дальнейшем процессе работы такая известь дает однородную шихту и мелкозернистую структуру изделий. Затем гашеную известь и лесок совместно размалываю^ в дезинтеграторе.
На силикатных заводах известь гасят по-иному. Смесь песка и извести прогревают паром до 70°. Выделенное известью тепло при переходе СаО в Са(ОН)2 доводит температуру до 100°. Вследствие этого длительность процесса сокращается и получается мелкодисперсная известь.
В результате строительства нескольких сотен заводов, которые будут выпускать силикальцитные изделия, резко возрастет потребность в извести. Организация известковых карьеров, их эксплуатация, транспортировка сырья на место .потребления могут несколько задержать темпы дальнейшего продвижения силикальцита в СССР. Вот почему следует своевременно обратить внимание на материалы, содержащие окись кальция. Профессор А. В. Волженский предложил вместо извести использовать металлургические отвальные шлаки и торфяные золы. В настоящее время в отвалах металлургических заводов имеется примерно 75 миллионов тонн шлаков и ежегодно еще добавляется до 15 миллионов тонн. Стоимость молотых шлаков и зол не будет превышать 40—50 рублей за тонну, в то время как такое же количество извести после измельчения и гашения обходится по 100 рублей и более.
Второй источник расширения известковой базы для силикальцитных изделий автоклавного твердения — использование магнезиальной и доломитовой извести.
Научно-исследовательские работы института стройматериалов МПСМ БССР и практика Ивановского силикатного завода показали, что можно пользоваться магнезиальной известью с содержанием окиси магния в пределах 8—14% при добавке в шихту 4% трепела. В этом случае аморфный кремнезем в автоклаве быстрее соединяется с окисью кальция, чем с окисью магния, и создает довольно прочную решетку в массе, что препятствует деформации изделий от увеличения объема окиси магния при дальнейшей водотермической обработке. Можно получить вполне доброкачественные изделия, даже когда в шихте имеется до 33% окиси .магния. Правда, тогда обжиг высокомагнезиальной извести приходится производить особым способом (профессор Э. Д. Певзнер).
Таким образом, повсеместное распространение извести или отходов производств, которые ее содержат, дает прочную базу второму компоненту для изготовления силикальцита.