Теоретические соображения и практический опыт показывают, что в настоящее время имеется полная возможность изготовления силикальцитных изделий с очень высокими свойствами. Например, нами была получена морозостойкость вибрированных силикальцитных образцов объемным весом 1,82 г/см3 (10X10X10 см), свыше 200 циклов. Образцы изготовлялись из производственных дезинтегрированных смесей с удельной поверхностью песка 510 см2/г, активностью 10,5% СаО и формовочной влажностью 15,3%.
Десятилетняя практика эксплуатации силикальцитных изделий, использованных при строительстве зданий, показывает, что они отвечают предъявляемым к ним требованиям в отношении морозостойкости. Однако при расширении номенклатуры изделий их морозостойкость необходимо повышать.
Технологические факторы, влияющие на морозостойкость силикальцита
Рассмотрим главные технологические факторы, от которых зависит морозостойкость силикальцита.
а) Качество сырьевых материалов
Принципиально силикальцит можно приготовить из песка и извести любою качества.
Пригодность различных песков для изготовления силикальцита высокой морозостойкости определяется пока только опытным путем. Теоретические основы вопроса требуют еще детальных исследований.
На основании работ, проведенных на Опытном заводе УПСМ СНХ ЭССР в целях определения пригодности различных песков для приготовления силикальцита, выяснилось, что силикальцит, получаемый на базе некоторых песков, обладает уменьшенной морозостойкостью.
В производстве известково-песчаных изделий важное место занимает качество извести.
При изготовлении плотных нзвестково-пеечаных изделий имеется, как известно, два основных направления в части применения извести: во-первых, изготовление изделий на базе гашеной и, во-вторых, на базе негашеной извести. Преимуществом последнего метода является возможность более легкого достижения высоких объемных весов [16]. Но при применении кнпелки даже самое незначительное отклонение от технологии и пониженное качество извести сразу ведут к понижению качества изделий и к возникновению дефектов. При низком качестве извести, поступающей на снликалыштный завод (низкая активность, высокая магнезиальность и содержание пережженных частиц), необходимо применять гашеную известь, т. к. содержание даже небольшого количества негашеных частиц отрицательно влияет иа качество структуры монолита.
Нужно отметить, что при запаривании изделий на базе извести, содержащей небольшое количество негашеных частиц, обычно не возникает дефектов, заметных простым глазом.
Для уточнения этого вопроса был проведен следующий опыт.
Часть.извести, применяемой Для изготовления текущей продукции Опытного завода, гасилась водой (во влажном состоянии находилась 12 часов), часть — в гасильном барабане Опытного завода и часть — после гасильного барабана дополнительно в автоклаве (вместе с изделиями).
Продолжительность гашения извести в гасильном барабане составляла 50 минут при давлении 4 ати.
Из всех трех видов извести приготовили прессованные цилиндры, которые затем запаривались (рис. 17 а, б, в). Образцы из извести, загашенной водой, разрушились полностью (рис. а), на образцах из извести, загашенной в цеховом гасильном барабане, появились трещины (рис. б), а образцы из извести, загашенной дополнительно в автоклаве, были без всяких дефектов (рис. в).
На базе извести, загашенной вышеприведенными способами, были приготовлены силикальцитные смеси, из которых вибрированием изготовлялись кубики размерами 7x7x7 см.
Данные испытания образцов приведены в таблице 1.
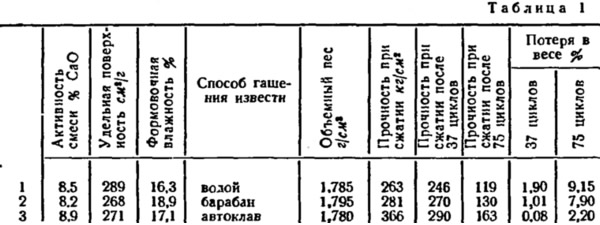
Картина разрушения образцов после запаривания была следующей:
- а) в случае применения извести, загашенной водой, наблюдалось сильное расслаивание поверхности и сильное разрушение нижних краев образцов;
- б) в случае извести, загашенной в цеховом гасильном барабане, возникло расслаивание торцевой поверхности и характерное разрушение образца с нижних краев;
- в) в случае извести, загашенной полностью, наблюдалось обламывание краев.
Определение морозостойкости производилось по ГОСТ 7025—54.
Из таблицы видно, что в случае использования извести, загашенной в гасильном барабане, прочность при сжатии составляет 77%, а в случае использования извести, загашенной водой, — 72% от прочности при сжатии, полученной при использовании полностью погашенной извести при одних и тех же объемных весах и показателях смеси. На зависимость морозостойкости от степени гашения извести наиболее характерно указывает потеря образцов в весе.
Из таблицы 1 также видно, что самая высокая морозостойкость получается в случае применения полностью загашенной извести, меньше — извести, загашенной в барабане, и самая низкая — при гашении извести холодной водой.
На основании вышеизложенного можно сделать вывод, что для изготовления изделий высокой морозостойкости необходимо применять только полностью гашеную известь.
б) Оптимальные активности смесей и продолжительность запаривания
До настоящего времени проведено довольно много работ по исследованию оптимальной активности известково-песчаных смесей. Притом оптимальную активность оценивали, главным образом, по прочностным показателям. На основании этих исследований выяснены оптимальные активности смесей в зависимости от удельных поверхностен песка [6,7, 8].
И А. Хинт дает следующую формулировку оптимального количества извести в смеси [5].
- а) количество извести, которое при данной величине удельной поверхности песка и автоклавном режиме полностью вступает в соединение с молекулами SiO2;
- б) количество извести, достаточное для образования на поверхности всех зерен кварцевого песка разъедания кристаллической решетки и образования вяжущего на известном оптимальном протяжении;
- в) количество извести, позволяющее хорошее уплотнение смеси, при разных удельных поверхностях песка [6, 7, 8].
В течение последующих лет полученные ранее значения оптимальной активности уточнялись.
По теоретическим соображениям для получения высокой морозостойкости каждому значению удельной поверхности соответствует определенная оптимальная активность и, соответственно, определенная структура новообразования.
Образование структуры максимальной морозостойкости зависит от количества извести на 1 мг песка в смеси, от удельной поверхности дезинтегрированной смеси и продолжительности запаривания.
В 1959 г. нами изучался вопрос о влиянии продолжительности запаривания и активности смеси на морозостойкость силикальцита. Ниже представлены важнейшие результаты проведенной работы.
Нами [13] были изготовлены прессованные образцы различных объемных весов из смесей разных активностей.
В таблице 2 приведены данные примененных смесей.
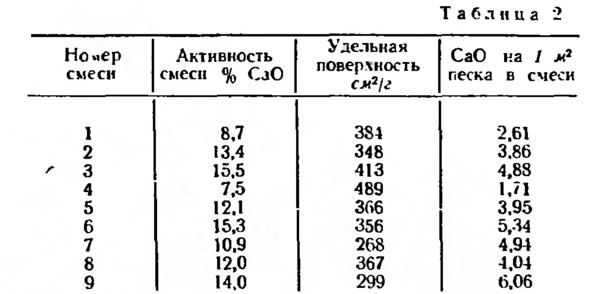
Применяемая для приготовления смесей известь была полностью погашена.
Образцы формовались в виде цилиндров, имеющих высоту и диаметр равные 42 мм, и в виде кубиков размерами 70x70x70 мм. Образцы запаривались с разной продолжительностью при давлении 10 ати.
Данные относительно прочности при сжатии образцов приведены на рис 18.
Анализ данных, приведенных на рис. 18, показывает, что образцы из смеси 4 (уд. поверхность 489 см2/г, активность 7.5%) приобретают максимальную прочность менее чем за 8 часов, из смеси 1 — в течение 12 часов (уд. поверхность 384 см2/г, активность 8,7% СаО). Максимум прочности образцов из остальных смесей достигается после 16 часов.
Морозостойкость определялась по ГОСТ 4800-49 и ГОСТ 7025 54. Определения морозостойкости образцов прекращались после того, как образец получал оценку «2» (образец крошится). При этом, через каждые три цикла попеременного замораживания и оттаивания образцы взвешивались. Потеря в весе цилиндрических образцов после получения оценки «2» была в пределах 1÷1,5%, у кубиков вес образцов после прекращения испытании равнялся весу образцов до испытаний.
Исследовательскими работами установлены оптимальные режимы запаривания для разных видов силикальцитных изделий [9].
При установлении оптимального режима запаривания основывались, главным образом, на наиболее экономичном режиме для получения максимальной прочности изделий.
Для получения максимальной морозостойкости изделий необходимо придерживаться определенной продолжительности запаривания, чтобы получить структуру новообразования, обеспечивающую высокую морозостойкость.
Па рис. 19 представлена зависимость морозостойкости некоторых образцов от продолжительности запаривания. Выяснилось, что при запаривании морозостойкость образцов повышается до определенного момента, а после этого снова начинает снижаться. На графике приведены только данные относительно образцов, морозостойкость которых была меньше 100 циклов. Так как испытания морозостойкости прекращались после 100 циклов, коэффициент морозостойкости во всех случаях быт свыше 0,75, в отдельных случаях — 0,99.
Характерно, например, что морозостойкость образцов, запаренных в течение 8 часов, равна 56, 84, 46 циклам, запаренных в течение 20 часов — 18, 30, 15, 30 циклам (смеси 7, 8, 9).
Па рисунке 20 изображены образцы 70x70x70 мм после 100 циклов попеременного замораживания и оттаивания.
- а) смесь 8, объемный вес 1,85 г/см3;
- б) смесь 8, объемный вес 1,95 г/см3;
- в) смесь 9, объемный вес 1,95 г/см3 (испытания продолжаются).
Подробный анализ наших опытных данных позволяет дать оптимальные активности смесей, а также оптимальные продолжительности запаривания для достижения максимальной морозостойкости изделий.
Результатом анализа является график (рис. 21) зависимости отношения оптимальной активности к морозостойкости в зависимости от удельной поверхности смеси, а также оптимальные продолжительности запаривания. (Время выдерживания изделия под постоянным давлением.)
График составлен на основании испытаний образцов объемным веселя 1,65—1,95 г/см3 из смеси удельной поверхностью 250±500 см3/г.
На рис. 21 приведены кривые,в широком диапазоне активностей. Практически можно рекомендовать изготавливать смеси с отклонением от установленной оптимальной активности не более ±1% СаО. При этом необходимо соблюдать устанавливаемые, в зависимости от требуемых показателей изделия, продолжительности запаривания.
В случае требования высокой прочности изделий нужно ориентироваться на продолжительность запаривания, обеспечивающую максимальную прочность. В случае требований морозостойкости — на продолжительность запаривания, обеспечивающую максимальную морозостойкость (на основании рис. 21).
Нами было установлено, что морозостойкость силикальцита при быстром выпуске пара [12, 13] уменьшается. При опытах варьировали продолжительностью выпуска пара в пределах от 1 до 4 часов, при разных активностях смеси и объемных весах образцов, уменьшение морозостойкости составило, в среднем, 30%. Прочность на сжатие изменялась незначительно.
Применяемые в практике продолжительности выпуска пара в зависимости от толщины изделия колеблются от 2,5 до 5 часов при толщине изделий соответственно 20 и 40 см. Полученные нами результаты подтверждают, что применяемые в настоящее время продолжительности выпуска пара, вероятно, являются пригодными и для производства изделий высокой морозостойкости.
После открытия крышки автоклава для предотвращения больших разрешающих термических напряжений и возникновения дефектов изделия нужно выдерживать в автоклаве с открытой крышкой еще в течение 1—2 часов, в зависимости от толщины
в) Плотность и структура изделий
Долговечность, в том числе и морозостойкость, бетонов и известково-песчаных материалов существенно зависит от их плотности [3, 10, 11, 12, 13]. Повышение плотности, т. е. объемного веса, является одним из важнейших факторов, повышающих морозостойкость силикальцита.
При приготовлении крупных детален из дезинтегрированных смесей главным способом уплотнения является вибрирование (в том числе и с поверхностным пригрузом).
При изготовлении изделий малых размеров уплотнение обычно достигается прессованием. Общим требованием, предъявляемым ко всем видам уплотнения, является получение однородной структуры.
Ясно, что неоднородная структура слабее противодействует разрушающим напряжениям. Например, морозостойкость канализационных труб, трамбованных вручную, составляет только 25—50% от морозостойкости труб, формованных на шнековом прессе [14]
По той же причине морозостойкость черепицы ручной формовки трамбованием при влажных смесях больше морозостойкости черепицы из относительно более сухих смесей, формованных до той же плотности [6].
Образование структуры силикальцита максимальной морозостойкости
Результаты наших испытаний еще раз подтверждают предположение о том, что максимальной морозостойкости силикальцита соответствует определенная структура новообразования, в которой в процессе запаривания происходят различные изменения.
Рассмотрим некоторые из них подробно.
а) Состав новообразования
Вопросами исследования зависимости качества известково-песчаных из гелий от состава новообразования посвящены некоторые работы теоретического характера. В основном, исследовались смеси с очень высокой активностью и большой удельной поверхностью песка (до 7500 см2/г).
Фазовый состав новообразования силикальцита определен нами в исследовательских работах 1957 и 1958 г. [12, 17], зависимость состава новообразования от продолжительности запаривания установлена в 1959 г. [13].
При запаривании силикальцитных изделий в известный промежуток времени происходит увеличение прочности при сжатии. Затем прочность начинает снова медленно снижаться. Снижение прочности объясняется изменением в структуре новообразования — уплотнением и перекристаллизацией.
Во время запаривания в новообразовании происходит постепенное уменьшение соотношения CaO:SiO2.
Термографические исследования подтверждают, что максимальной морозостойкости соответствует момент, когда суммарный состав новообразования CaO:SiO2 равен приблизительно 1,25.
На рис. 22 приведены некоторые термограммы силикальцитных образцов. Образцы запарены при 10 ати.
На основании термографического анализа выясняется следующее:
1) С увеличением продолжительности запаривания от 8 до 16 часов экзотермический эффект в интервале температур 105—250° остается неизменным или несколько уменьшается. Можно предположить, что количество гелеобразного вещества с увеличением продолжительности запаривания с 8 до 16 час. больше не увеличивается.
2) Экзотермический эффект в интервале температур 450—480° с увеличением продолжительности запаривания уменьшается. Причина заключается в дальнейшем взаимодействии образующихся в начальный период запаривания высокоосновных компонентов новообразования с кристаллическим SiO2. С увеличением продолжительности запаривания заметно также смещение максимума эффекта в сторону более низких температур.
3) Экзотермии при температурах 540—550°, соответствующих температуре дегидратации Са(ОН)2, не наблюдается.
4) С увеличением продолжительности запаривания экзотермический эффект при температурах свыше 800° увеличивается в противоположность уменьшению эндотермического эффекта при 450—480°. Характерно, что если после запаривания в течение 8 часов в интервале 750—850° наблюдается лишь сильный эндотермический эффект, то после запаривания в течение 12 часов уже заметна экзотермия, а в течение 16 часов — появляется сильный экзотермический эффект. Следовательно, увеличивается количество компонентов новообразования с мольным соотношением CaO/SiO2=1. Можно наблюдать смещение экзотермического эффекта в сторону более низких температур, т. е. в сторону понижения основности новообразования.
Резюмируя вышеуказанное, можно сделать вывод, что максимальной морозостойкости силикальцита соответствует определенный состав новообразования при соотношении CaO/SiO2=1,25. Дальнейшее запаривание ведет к уменьшению морозостойкости.
б) Распределение объемов пор
В связи с изменением состава новообразования должно измениться и расположение объемов пор силикальцитного монолита Известно, что температура замерзания воды в порах материала зависит от размеров пор Например, по данным Р. Е. Брилинга температура замерзания воды в капилляре диаметром в 1,57 мм равна — 6,4°С, при диаметре капилляра 0,06 мм она понижается до — 18,5°С [18]. Некоторое влияние на температуру замерзания воды оказывает наличие в ней в растворенном состоянии веществ того или иного строительного материала.
В целях исследования изменения распределения объемов пор нами были проведены соответствующие определения при помощи ртутного порометра. Метод основывается на вдавливании ртути в поры материала. Аппаратура составлена по схеме А. С. Беркмаиа [19].
Б 1959 г. нами был определен угол смачивания ртути на поверхности силикальцита. Было получено, что угол смачивания ртути находится в пределах 115—120°. Но известно, что при определении угла смачивания очень трудно получить достоверные данные. Поэтому в настоящей работе за величину угла смачивания принят по данным Т. Г. Плаченова [20] угол в 145°.
На рис. 23 изображены некоторые дифференциальные кривые распределения объемов пор образцов, запаренных в течение 8,12 и 16 часов при 10 ати Оптимальная продолжительность запаривания в отношении морозостойкости — 12 часов.
На основании наших опытов установлено, что пористость силикальцита в ходе запаривания изменяется. Максимальной морозостойкости соответствует наименьшие диаметры пор.
Выводы
Существует связь между активностью смеси, удельной поверхностью песка в смеси и продолжительностью запаривания для получения максимальной морозостойкости силикальцита (рис. 18).
Образование структуры силикальцита максимальной морозостойкости нужно объяснить следующим образом:
В новообразовании силикальцита во время запаривания происходит постепенное соотношение CaO/SiO2.
Максимальная морозостойкость достигается в тот момент, когда суммарный состав новообразования станет равным CaO/SiO2 1,25, т. е. практически весь компонент новообразования с отношением Ca0/SiO2≈2 превратится в компонент с меньшей основностью. При этом наблюдается наибольшая плотность монолита.
При быстром выпуске пара из автоклава в течение 1 часа вместо 4-х часов морозостойкость изделий понижается из-за возникновения микродефектов.
Подтверждается требование применения для изготовления силикальцита высокой морозостойкости только полностью гашенной извести.