Свойства бетонных смесей
Для приготовления бетонов, отвечающих современным требованиям, необходимы высококачественные цемент и заполнители.
Свежеприготовленную смесь из этих материалов и воды, взятых в строго определенных пропорциях, называют бетонной смесью или товарным бетоном. Бетон и бетонная смесь — это разные состояния материала, с различными свойствами и требованиями, предъявляемыми к ним. Поэтому не следует смешивать эти два понятия.
Для получения бетона высокого качества помимо применения высококачественных материалов укладываемая бетонная смесь должна обладать определенными свойствами, соответствующими выбранной технологии.
Одним из важных свойств бетонной смеси является удобоукладываемость — способность ее заполнять форму с наименьшими затратами труда и энергии, обеспечивая при этом максимальную плотность, прочность и долговечность бетона.
Удобоукладываемость смеси зависит от ее подвижности (текучести) и пластичности (связности), т. е. способности не расслаиваться при транспортировании и в процессе укладки. Показателем подвижности служит осадка конуса в сантиметрах или показатель жесткости, измеряемый в секундах1.
В зависимости от подвижности бетонные смеси подразделяют на литые с осадкой конуса (ОК) более 12 см, подвижные — с ОК=2÷12 см, малоподвижные при ОК=0,5÷2 см и показателем жесткости (ПЖ) менее 30 с, жесткие — с ОК=0 и ПЖ=30÷200 с и особо жесткие при ПЖ более 200 с.
Подвижность бетонной смеси зависит прежде всего от содержания в ней воды, а также от водоцементного отношения, вида цемента, крупности заполнителей, количества и гранулометрического состава песка, введения в бетон добавок и др.
Хотя увеличение содержания воды в бетоне увеличивает подвижность бетонной смеси и облегчает ее укладку, однако лишняя вода в бетоне вредна. Она увеличивает вероятность расслаивания бетонной смеси, увеличивает пористость и усадку бетона, что снижает его качество.
Форма, размеры зерен крупного заполнителя и характер его поверхности также влияют на подвижность бетонной смеси. При окатанной гладкой поверхности зерен гравия уменьшается трение между ними, т. е. увеличивается подвижность. Более крупный заполнитель имеет меньшую суммарную поверхность. Следовательно, при одинаковом количестве цементного теста его прослойки между зернами будут иметь большую толщину, что увеличивает подвижность смеси.
С увеличением расхода песка или применении мелких песков повышается суммарная поверхность заполнителей, что снижает подвижность смеси. По этой же причине повышенный расход цемента при постоянном содержании воды снижает подвижность бетонной смеси, увеличивая прочность бетона. Вид цемента, тонкость его помола также влияют на подвижность. Так, шлакопортландцемент, обладая большей водопотребностью, чем портландцемент, при одинаковом содержании воды обеспечивает меньшую подвижность смеси.
Введение в бетонную смесь добавок поверхностно-активных веществ (ПАВ) увеличивает ее подвижность. Некоторые ПАВ, адсорбируясь в виде тончайших пленок на поверхности зерен заполнителя, снижают трение между ними. В результате увеличиваются подвижность и пластичность бетонных смесей. Такие добавки называют пластифицирующими.
Другая группа ПАВ — гидрофобизирующие — при перемешивании способствуют вовлечению в бетонную смесь мельчайших пузырьков воздуха, которые равномерно распределяются по всей ее массе. Такие добавки не только увеличивают подвижность и пластичность смеси, но и повышают морозостойкость и долговечность бетона.
Бетонные смеси с большой подвижностью (ОК=4 см и более) легче укладывать, т. е. они более технологичны. Трудоемкость и расход энергии на укладку жестких смесей, наоборот, больше. Хорошо уплотненные жесткие смеси позволяют получить более качественный бетон, чем, например, литые. Однако из-за большой трудоемкости укладки жесткие смеси иногда остаются недоуплотненными, что снижает качество бетона.
На практике подвижность бетонных смесей принимают в зависимости от способов подачи их в блок бетонирования, а также от размеров конфигурации и степени армирования конструкций.
В табл. 7-1 приведены показатели подвижности бетонной смеси в момент ее укладки.
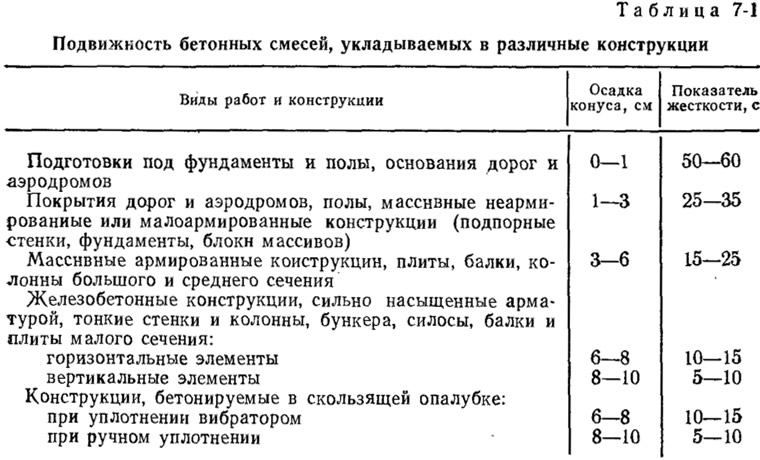
Осадка конуса бетонных смесей, перемещаемых ленточными транспортерами, не должна превышать 6 см, в противном случае смесь будет стекать с ленты транспортера. Подвижность бетонных смесей, перекачиваемых по трубопроводам с помощью бетононасосов или пневмонагнетателей, должна находиться в пределах 6—12 см.
Под водоудерживающей способностью бетонной смеси понимают максимальный расход воды, при котором смесь сохраняет свою связность, т. е. не расслаивается. Это свойство зависит от водоудерживающей способности вяжущего, тонкомолотых добавок, а также количества и гранулометрического состава песка, размеров зерен и. формы поверхности крупного заполнителя. В бетонных смесях, содержащих большой излишек воды, после их укладки вплоть до полного схватывания наблюдаются процессы расслаивания и водоотделения.
Приготовление бетонных смесей
Технологический процесс приготовления бетонных смесей показан на схеме рис. 7-1.
В современных условиях бетонные смеси готовят на районных или центральных заводах товарного бетона. Как исключение, их получают на смесительных установках, располагаемых вблизи от места укладки бетона.
Районные заводы производительностью 100 000—200 000 м3 товарного бетона в год обеспечивают им несколько строительных площадок, расположенных в радиусе 25—30 км.
Районные бетоносмесительные заводы могут состоять из одной, двух или трех типовых секций. Каждая секция представляет собой самостоятельную технологическую линию (рис. 7-2). Важными преимуществами таких заводов являются низкая себестоимость и трудоемкость 1 м3 товарного бетона. Недостаток их — большие издержки на транспортирование бетонных смесей и снижение их качества в результате длительного нахождения в пути.
Центральный бетоносмесительный или бетонорастворный завод (БРЗ) обеспечивает товарным бетоном и раствором одну крупную строительную площадку. Производительность БРЗ достигает 30—50 тыс. м3 в год, а срок службы на одном месте составляет 5—7 лет. Конструкции таких заводов разборно-переставные (рис. 7-3) для облегчения перебазирования их с объекта на объект.
Себестоимость приготовления 1 м3 бетонной смеси на БРЗ не превышает 0,5—0,6 руб., а трудоемкость — 0,1—0,3 чел·ч. Хотя эти показатели несколько хуже, чем на районных заводах, зато снижаются затраты на перевозку товарного бетона и практически не ухудшается качество бетонной смеси в пути.
Для обеспечения бетонной смесью мелких рассредоточенных объектов используют передвижные или инвентарные бетоносмесительные установки. Передвижные бетоносмесительные установки монтируют на трейлерах, прицепах или железнодорожных платформах и устанавливают непосредственно у места бетонирования. Свежеприготовленную бетонную смесь подают непосредственно в опалубку транспортерами, бетононасосами или с помощью кранов. Производительность передвижных бетоносмесительных установок от 5 до 15 м3/ч.
Инвентарную бетоносмесительную установку (рис. 7-4) собирают из отдельных секций и блоков, а после окончания работ на участке демонтируют и перевозят на новое место.
Бетоносмесительные заводы и установки могут быть цикличного {периодического) и непрерывного действия. Цикл состоит из трех операций: загрузки исходных материалов в бетоносмесители, перемешивания и выгрузки готовой смеси. Такая схема позволяет оперативно менять дозировку и выдавать в течение смены бетонную смесь с разными параметрами: подвижностью, маркой и т. п.
На заводах и установках непрерывного действия процессы дозирования, загрузки, перемешивания и выдачи готовой смеси протекают без перерыва. Такие установки целесообразно размещать там, где необходимо получать большое количество бетонной смеси с одинаковыми технологическими параметрами (например, в гидротехническом строительстве).
Бетоноемесительные заводы и установки имеют высотную и ступенчатую (партерную) схемы компоновки.
Высотная схема (рис. 7-5, а) отличается тем, что материалы (цемент, заполнители) поднимают в расходные бункера, откуда они перемещаются вниз гравитационно, под силой собственной массы.
Заполнители подают со складов ленточными конвейерами 1 и 2 через поворотную воронку 6 в расходные бункера 7. Одновременно в расходный бункер подают цемент с помощью элеватора 8 или пневматическим способом. Отмеренные в дозаторах 5 и 9 материалы через сборную воронку 10 поступают в смеситель 11. Готовая смесь через раздаточный бункер 4 поступает в автобетоновоз 3. Такая компоновка проста и надежна, однако увеличивается высота и усложняется строительная часть завода (установки).
При ступенчатой (партерной) компоновке (рис. 7-5, б) материалы поднимают в два приема: сначала в расходные бункера, а после дозирования в смесители.
Заполнители с помощью конвейеров 1 и 2 подают через воронку б в раздаточные бункера 7, а цемент закачивают в бункер с помощью элеватора 8 или пневмосистемы. Далее сыпучие материалы попадают через дозаторы 9 и сборную воронку 10 на ленточный транспортер 12 или в ковш скипового подъемника, с помощью которых их подают в смеситель 11. Готовую смесь через раздаточный бункер 4 разгружают в автобетоновоз 3.
Ступенчатая компоновка обеспечивает меньшую высоту, но площадь завода (установки) увеличивается. По такой схеме выполняют обычно передвижные и инвентарные установки построечного типа.
Основным механизмом бетоносмесительных установок и заводов являются смесители.
По принципу действия различают бетоносмесители гравитационного и принудительного действия.
Компоненты в гравитационных смесителях (рис. 7-6) перемешиваются с использованием принципа свободного падения частиц. Емкость смесительных барабанов у таких смесителей может быть 100, 250, 500, 750, 1200, 2400 и 4500 л. Вместимость барабана определяют по объему сухих материалов (без воды), загружаемых в смеситель.
В гравитационных смесителях (рис. 7-7) нет трущихся и быстроизнашивающихся деталей, но габариты их большие по сравнению с аналогичными смесителями принудительного действия. В них целесообразно приготовлять пластичные бетонные смеси. При снижении же осадки конуса бетонной смеси время перемешивания резко возрастает, производительность смесителей падает. Вследствие этого гравитационные смесители для приготовления жестких смесей применять нецелесообразно.
В бетоносмесителях принудительного действия (рис. 7-8 и 7-9) смесь перемешивается лопастями. Такие 6eтоносмесители имеют небольшие габариты и обеспечивают более высокую однородность смеси. В них целесообразно приготовлять жесткие смеси и бетоны на легких и пористых заполнителях. К недостаткам таких смесителей относятся наличие трущихся быстроизнашивающихся деталей и некоторая конструктивная сложность.
Часовую производительность бетоносмесителя, работающего по цикличному принципу, определяют по формуле

где Vб — вместимость бетоносмесителя, л; К'в — коэффициент выхода бетона: nз — количество замесов в 1 ч.
Количество замесов раствора определяют по формуле

где tц — продолжительность цикла приготовления бетонной смеси, мин;

где tз — время загрузки смесителя, tп — заданная длительность перемешивания; tв — время выгрузки.
Коэффициент выхода бетона учитывает уменьшение объема бетонной смеси на выходе по отношению к суммарному объему сухих материалов, загружаемых в смеситель. Для тяжелых бетонов он равен 0,67, для бетонов на легких заполнителях — 0,75, для ячеистых бетонов — 0,80.
Для получения бетонных смесей хорошего качества в процессе их приготовления нужно вести пооперационный лабораторный контроль. Лаборатория контролирует влажность и зерновой состав заполнителей, качество цемента, точность дозирования, продолжительность перемешивания, подвижность или жесткость бетонной смеси и другие параметры.
Для контроля прочности бетона изготовляют образцы-кубы, выдерживаемые до испытаний в условиях нормального твердения (t=20°С, В0=90%). Количество образцов и сроки их испытаний устанавливает строительная лаборатория в соответствии с указаниями СНиП III-15—76.
Современные бетоносмесительные заводы и установки отличаются высоким уровнем механизации и автоматизации. Все рабочие операции по разгрузке заполнителей и цемента, подаче их в расходные бункера, дозировке, перемешиванию и выдаче готовой смеси выполняет комплект взаимоувязанных механизмов.
Автоматизация бетоносмесительных заводов и установок может быть частичной и комплексной. При частичной автоматизации имеются дистанционное или автоматическое управление отдельными механизмами или их группами, а также средства автоматического контроля отдельных параметров (влажность заполнителей, точность дозировки и т. п.).
При комплексной автоматизации управление всеми механизмами, транспортными средствами и контроль за технологическими операциями ведутся с одного пульта. Управляют такими заводами-автоматами несколько операторов.
Охрана труда
Ввиду технологической сложности современных бетоносмесительных заводов и установок от обслуживающего персонала требуются глубокие знания но охране труда. Лица, допущенные к управлению машинами и механизмами, должны пройти техминимум по изучению правил охраны труда и получить соответствующие удостоверения.
Для обеспечения условий безопасной работы движущиеся механизмы и узлы машин, лестницы, площадки должны быть ограждены и хорошо освещены. Электродвигатели и электроустановки требуется надежно заземлить.
Помещения, в которых работают с пылящими материалами (цементом), нужно оборудовать хорошей вентиляцией и устройствами, исключающими их распыление. Рабочие в запыленных помещениях должны пользоваться очками, респираторами и противопылевыми комбинезонами.
На время очистки, смазки и ремонта машины и механизмы останавливают; пускать машину можно только после предупреждающего сигнала, который дается оператором.
Запрещается опорожнять вращающийся барабан с помощью лопат или других инструментов. Очищать барабан можно только после снятия приводного ремня и отключения электропредохранителей.
Приямок ковша скипового подъемника разрешается очищать только после дополнительного закрепления поднятого ковша на раме.
Во время работы транспортера запрещается очищать барабан, ленту и рольганги от грязи и налипшего бетона. Нельзя проходить под неогражденной движущейся лентой транспортера, а также проверять крепление ковшей к ленте на работающем элеваторе, снимать крышку с работающего винтового транспортера.
Запрещается ремонтировать пневматические устройства (пневмоцилиндры, разводки и т. п.) под давлением.
Работы в силосах должны выполнять только опытные и проинструктированные рабочие, снабженные предохранительными поясами, средствами индивидуальной защиты и обязательно под наблюдением инженерно-технических работников.
Примечания
1. Методика измерения осадки конуса, а также показателя определяемой жесткости с помощью технического вискозиметра изучается в курсе «Строительные материалы».