Оптимальным является равномерное распределение массы в отдельных элементах. Из этих соображений рационально использовать щиты каркасной конструкции с повышенной несущей способностью. Плоские щиты целесообразны при устройстве опалубки плоских плит перекрытий или наклонных конструкций небольшой толщины.
Размер щитов опалубки отечественной конструкции принимается, как правило, кратным модулю 300 мм, что позволяет при большом числе вариантов сборки опалубки по размерам значительно снизить их число и тем самым трудоемкость опалубочных работ. Предпочтительны следующие размеры щитов: длина — 1200, 1500, 1800 мм; ширина — 300 и 600 мм. Возможно применение щитов, имеющих ширину 400 и 500 мм, особенно при бетонировании ступенчатых фундаментов. Использование таких щитов позволяет собирать без применения доборов опалубку для конструкций с модулем 100 мм.
Унифицированная инвентарная опалубка системы «Монолит» (рис. 7) применяется для образования вертикальных бетонных поверхностей. При бетонировании конструкций с горизонтальными и наклонными поверхностями комплект дополняется элементами для поддержания опалубки: стойками, ригелями, балками, прогонами и специальными креплениями. Кроме этого, в комплекте имеется вспомогательная оснастка для производства опалубочных и бетонных работ (навесные стремянки, рабочие площадки и пр.).
Щиты каркасной конструкции выполнены как полностью из металла, так и комбинированными с использованием в качестве палубы дерева, фанеры, древесностружечных плит, пластика.
Торцы неметаллической палубы защищены по всему периметру от механических повреждений приваренной по контуру металлической рамкой. От увлажнения торцы палубы защищены водостойким герметиком. В качестве материала для защиты торцов могут быть применены следующие составы:
- К-115 (СТУ 30-14148-63): эпоксидная смола ЭД-5, пластифицированная полиэфиром МГФ-9, отвердитель — полиэтиленполиамин (15 мас. ч), компаунд (10 мас. ч), наполнитель — цемент (100...200 мас. ч);
- К-163 (СТУ 30-14161-64): ЭД-5, пластифицированная полиэфиром МГФ-9 и тиоколом, отвердитель — полиэтиленполиамин;
- К-168 (МРТУ 6-05-1023-66): ЗД-б, пластифицированная полиэфиром МГФ-9, отвердитель — полиэтиленполиамин;
- К-201 (СТУ 30-1447-63): ЭД-5. пластифицированная полиэфиром МГФ-9, отвердитель — полиэтиленполиамин (15 мас. ч), компаунд (100 мас. ч), наполнитель — цемент или вибропомолотый кварц.
Для улучшения качества поверхности бетонных конструкций, а также для повышения оборачиваемости палубы из фанеры, древесностружечных и древесноволокнистых плит целесообразно применение пленок, получаемых путем пропитки бумажной или стеклотканевой основы фенольными смолами. Пленки наносят на древесные материалы с помощью прессов с подогреваемыми плитами. Продолжительность прессования под давлением 1,4...1,8 МПа при толщине фанеры 18 мм составляет от 5 до 12 мин в зависимости от температуры (130..160°С).
Крепление неметаллической палубы осуществляется с помощью накладок, закрепляемых к продольным и поперечным ребрам каркаса щита, что позволяет осуществлять быструю замену палубы. Для крепления щитов между собой, а также со схватками в каркасе щита предусмотрены круглые отверстия диаметром 20 мм, устраиваемые с шагом 100 мм. Крепление щитов к схваткам осуществляют с помощью натяжных крюков с винтовым или клиновым запором, а крепление щитов один к другому — с помощью специального замка (рис. 8). При соединении палец замка заводят в отверстие щитов, замок поворачивается вокруг оси пальца, и клинообразная прорезь пластины охватывает уголки соединения щитов. При легком ударе уголки щитов стягиваются и надежно фиксируются от продольных смещений. Палец замка удерживает щиты от поперечного смещения. Конструкция замка позволяет осуществлять надежное соединение щитов. Она значительно эффективнее широко применяемых пружинных скоб кашпо технологии изготовления, так и по надежности и удобству в работе. Кроме того, при изготовлении его используют обычные стали вместо пружинных, более дефицитных и требующих термической обработки при гибке.
Применение в качестве инвентарных тяжей арматуры периодического профиля позволяет увеличить шаг установки тяжей и тем самым снизить трудоемкость работ. Для закрепления тяжей из арматуры периодического профиля применен замок с клиновидным запором (рис. 9). Закрепление тяжей осуществляется с помощью неподвижного и подвижного сухарей, имеющих рисунок внутренней поверхности, соответствующий рисунку арматуры. Обжатие, затяжку и освобождение стержня осуществляют с помощью клина.
Схватки (рис. 10,а) выполнены из двух спаренных швеллеров. Продолговатые отверстия служат для соединения схваток под углом. Соединять их можно как по концам схваток, так и в любом месте по длине. Масса схваток при длине 2 м составляет 24,2 кг; при длине 2,5 м — 30,2 кг; 3 м — 36,2 кг; 3,5 м — 42,2 кг. Балки, (рис. 10,6), применяемые в основном для сборки опалубки ступенчатых фундаментов, состоят из двух поясов схваток, соединенных распорками. Высота балок соответствует высоте ступеней фундаментов — 300 и 600 мм. Применяют также балки высотой 400 и 500 мм. Балки являются несколько специфичными элементами разборно-переставной опалубки; масса их превышает 50 кг, установка и демонтаж их возможны только с помощью крана. Поэтому монтаж и демонтаж их целесообразно производить укрупненными панелями и блоками вместе с навешенными на них щитами.
Для устойчивостй установленных панелей опалубки их закрепляют подкосами. Подкосы служат также для рихтовки, точной установки опалубки, распалубливания. Подкосы, прикрепляемые к бетонному основанию, могут применяться для восприятия давления бетонной смеси. При этом может быть значительно сокращено (или даже исключено) число устанавливаемых стяжных болтов.
Поддерживающие элементы опалубки перекрытий включают телескопические стойки, раздвижные ригели, прогоны, балочные струбцины и т.д. Телескопические стойки имеют переменную длину и позволяют устанавливать опалубку перекрытий на высоте от 2 до 5 м. При бетонировании перекрытий на большей высоте (до 30 м) применяются дополнительные опорные нераздвижные стойки (табл. 3 и 4).
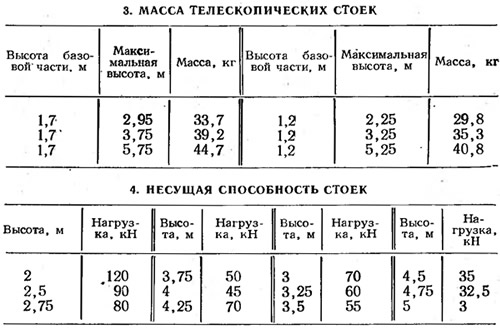
На верхнюю часть стоек могут быть надеты сменные оголовники с шипом для установки деревянных прогонов, а также с винтовым запором для закрепления как деревянных, так и металлических прогонов. Последние выполнены как статическими, так и поворотными для установки опалубки наклонных поверхностей.
Для установки опалубки балок используют специальные раздвижные 'балочные струбцины для бетонирования балок сечением от 200X300 до 600X800 мм. Для увеличения несущей способности стойки объединяют в трех- или четырехветвевые (в плане) колонны с помощью специальных струбцин.
Раздвижные ригели выполнены трех модификаций на пролеты от 1,2 до 2,в м; от 2,5 до 4 м и от 4 до 6 м. Первый ригель выполняется из двух швеллеров № 10, соединенных болтами. При установке ригелей с шагом 600 мм могут быть забетонированы плоские плиты перекрытий толщиной 250 мм.
Ригели на большие пролеты изготовляются из сварных пространственных ферм и входящих в них телескопических выдвижных балок. Балка ригеля для пролетов от 2,5 до 4 м выполнена из двутавра № 16, балки ригеля для пролетов от 4 до 6 м — из двутавра № 24, облегченного отверстиями, прорезанными по нейтральной оси, или двутавра №14, разрезанного и сваренного по выступам среза с образованием двутавра высотой 24 см с отверстиями посредине. Масса трех модификаций ригеля составляет соответственно 24,5; 71,4 и 100 кг (табл. 5).
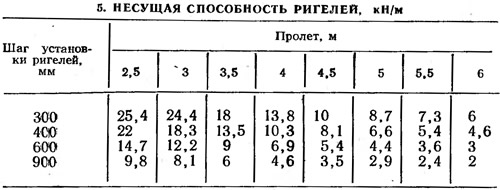
При использовании мелкощитовой опалубки до 80% работ может быть выполнено с применением крупноразмерных панелей и блоков.
Для увеличения оборачиваемости панелей необходима разработка ЛПР при тщательном анализе размерных характеристик. В ряде случаев с целью укрупнения панелей и уменьшения их типоразмеров целесообразно использование доборных элементов и доборных панелей меньших размеров.
Панели и блоки, рассчитанные на длительное использование, должны иметь большую жесткость и прочность, чем собранная поэлементно опалубка, и рассчитываться на восприятие транспортных и монтажных нагрузок. Поэтому часть креплений должна выполняться на болтах. В панелях (для увеличения несущей способности) широко можно использовать сдвоенные схватки, а также фермы шпренгельного типа.
Из условий деформации при монтажных и транспортных нагрузках соотношение сторон панелей должно быть ограничено (табл. 6).
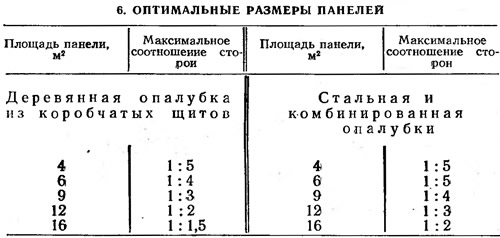
Панели и блоки собирают на специальных открытых площадках и стендах или в ремонтных или опалубочных цехах (рис. 11). При сборке панелей палубой вниз раскладывают щиты опалубки, по контуру устанавливают 'фиксаторы, щиты выверяют и соединяют между собой замками.
По верху щитов устанавливают и закрепляют схватки или фермы, причем крайние щиты соединяют со схватками с помощью болтового соединения. Болтовые соединения устанавливают также через каждые 1,5...2 м по длине панели и в каждом ярусе щитов по высоте. Крепление второго ряда схваток, устанавливаемых перпендикулярно первому, также производится на болтах. После установки подкосов и подмостей для бетонирования панель приводят в вертикальное положение и с ней при необходимости стыкуют другую панель (при сборке блоков опалубки).
Монтаж панелей и блоков производится краном по рискам, нанесенным на основание. Выверка и точная установка в вертикальной плоскости производится с помощью винтовых домкратов, устанавливаемых на подкосах панели. При монтаже верхних ярусов панелей по нижним первые после закрепления должны закрепляться растяжками или телескопическими стойками, установленными наклонно и упирающимися в основание или отсыпку. Монтаж панелей верхнего яруса после демонтажа нижних производится на опорные консоли, закрепляемые в стенах при бетонировании нижнего яруса, или на телескопические стойки, закрепляемые к забетонированной стене (при небольшой высоте).
При пропуске тяжей между соседними панелями в месте их стыковки устанавливают дополнительные схватки или другие несущие опоры.
Демонтаж панелей краном производится только после полного снятия креплений, отсоединения стяжных болтов и отрыва панели от бетона. Отрыв от бетона достаточно жестких и недеформированных панелей производится при ослаблении винтовых домкратов, установленных на подкосах, или при ослаблении установленных наклонно в распор телескопических стоек.
Монтаж опалубки замкнутых конструкций типа ступенчатых фундаментов, а также угловых сопряжений целесообразно производить Г-образными, а также замкнутыми или не замкнутыми в плане блоками. Перед установкой блока нижней ступени фундамента под колонны основание выверяют и выравнивают, на него наносят риски. Рихтовка выверенного перед монтажом блока по высоте производится подбивкой конусных прокладок. После установки тяжей или опор, опирающихся в забитые в основание якоря или в уплотненный грунт и воспринимающих нагрузки при бетонировании, блок окончательно выверяют по-размерам и рихтуют. Следующий блок опалубки монтируют на нижний, выверяют и закрепляют на нем.
При поэлементном монтаже опалубки ступенчатого фундамента вначале устанавливают опорные балки первой ступени, а балки между собой в углах не стягивают. После выверки балок на них навешивают щиты опалубки, начиная от углов. После установки, подгонки и рихтовки щитов весь короб опалубки выверяют, при необходимости устанавливают тяжи и балки окончательно закрепляют между собой, в углах. Аналогично производят монтаж опалубки следующих ступеней. При установке опалубки подколонника на схватках (также желательно применение балок) их раскладывают по опалубке верхней ступени и соединяют в углах. На них устанавливают и закрепляют за низ щиты опалубки подколонника. По верху щитов устанавливают второй ряд схваток. Щиты соседних сторон подколонника и схватки закрепляют между собой в углах.
После сборки и закрепления Г-образной поверхности аналогично устанавливают опалубку следующих поверхностей, начиная от углов. После установки одного яруса опалубки подколонника при необходимости вертикально устанавливают дополнительные схватки с перепуском на следующий ярус. После этого монтируют щиты в углах второго яруса, прикрепляя их к нижним щитам, и на них навешивают снизу схватки, которые сразу же соединяют в углах. После этого устанавливают остальные щиты по длине опалубки подколонника, соединяя их с нижним рядом щитов и соседними, закрепленными, щитами. Установленные щиты соединяют со схватками. После монтажа опалубку подколонника закрепляют растяжками и на нее навешивают подмости для бетонирования. Установку опалубки стен, ленточных фундаментов и фундаментов под оборудование также начинают с углов или угловых сопряжений. На установленную опалубку первого яруса сразу же закрепляют подкосы, устанавливаемые щиты (желательна вертикальная установка) последовательно соединяют с ранее установленными и со схватками. Поверхность опалубки стен должна через 1,5...2 м скрепляться с противостоящей опалубкой или прикрепляться к основанию. Закрепление может .производиться с помощью забитых в основание опор или в уплотненный грунт. Для устойчивости опалубки, а также для восприятия нагрузок при бетонировании могут использоваться наклонно устанавливаемые телескопические стойки. Однако поэлементный монтаж опалубки стен, фундаментов под оборудование и других конструкций с большими поверхностями должен производиться в исключительных случаях.
Набор необходимых элементов (условный комплект) (табл. 7) может быть использован для прикидочных расчетов потребности и материалоемкости опалубки, а также при заказе опалубки, когда неизвестна номенклатура возводимых конструкций. Для изготовления опалубки под конкретные монолитные конструкции из комплекта выбирают необходимые элементы.
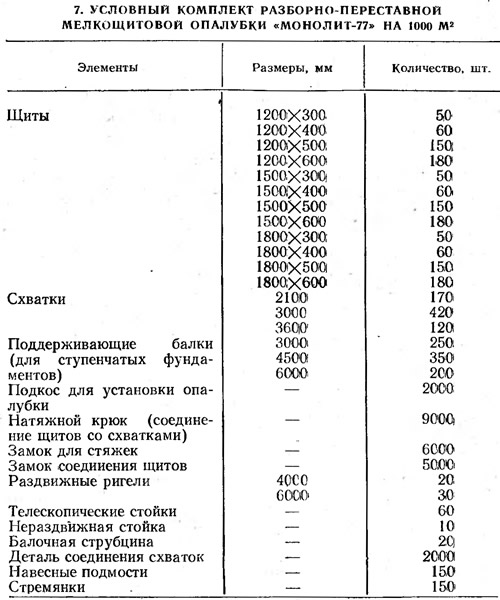
С целью определения рациональной конструкции панелей и блоков опалубки, а также для оптимизации установки поддерживающих и несущих элементов в ЦНИИСКе были проведены расчеты опалубок различных конструктивных схем1. В ЦНИИОМТП были проведены тензометрические испытания опалубки, позволившие уточнить расчетные данные и получить опалубку равнопрочной конструкции. Нагрузки принимались по СНиП III-15-76 при невысокой скорости бетонирования (V<0,5 м/ч). Нагрузки от вибрирования — 4 кПа, коэффициент перегрузки — 1,3. Шаг продольных схваток а менялся от 1 до 1,5 м, а шаг поперечных схваток b менялся от 1 до 4 м. Щиты принимались каркасной конструкции шириной 600 мм.
Наиболее оптимальным с точки зрения расхода материалов явилось расположение схваток с шагом а = 1 м и в = 1,5 м. Средние по высоте продольные схватки могут быть сдвинуты к центру (к месту стыка щитов по высоте).
При в = 0,5 возможно применение схваток из двух сдвоенных швеллеров № 6,5, при в > 0,5 необходима установка двойных швеллеров; увеличение в от 2 до 3 м почти не изменяет массу 1 м2 опалубки при соответствующем подборе несущих элементов. Однако сечение схваток должно увеличиваться или должны использоваться двойные схватки с дополнительными накладками.
При увеличении а до 1,5 м для сохранения равнопрочности конструкции желательно увеличение несущего каркаса щита.
Увеличенные шаги установки схваток (а = 1,5, в > 2,5) нецелесообразны, так как при незначительном снижении числа тяжей (и тем самым некотором снижении трудоемкости) значительно увеличиваются масса и стоимость опалубки, отдельные элементы нельзя монтировать вручную.
Изменение числа тяжей и шага расстановки схваток может изменять массу опалубки при тех же нагрузках от 4,7 до 8,3 кПа, т. е. почти в 2 раза, в соответствии с этим резко меняются (при использовании тех же несущих элементов) деформативность опалубки, точность и качество поверхности возводимых конструкций.
При расчете опалубки замкнутых конструкций (рис. 12) и стен принимались значительно большие нагрузки (по п. 2 табл. 1 прил. 1 к СНиП III-15-76, K1 = 1; K2 = 0,85; V = 3 м/ч, нагрузки при вибрировании 4 кН/м2 — коэффициент перегрузки 1,3) при достаточно высокой для таких конструкций скорости бетонирования 3 м/ч.
В расчетах и экспериментах варьировались конструкции и материал опалубки, шаг установки схваток и тяжей, просматривался также вариант установки опалубки без тяжей. Размеры блока (L) изменялись от 1,5 до 3 м. Щиты устанавливались вертикально.
Опалубка выполнялась из различных материалов:
- а) каркас щита и схватки из деревянных брусков;
- б) полностью металлическая опалубка, каркас щита из уголков, палуба из листа толщиной 2 мм;
- в) металлические схватки и каркас щита (из уголков) и палуба из фанеры толщиной 1,2 см;
- г) каркас щита и схватки из алюминиевого сплава (алюминий марки 1925Т с пределом текучести σT — 155 МПа), палуба из фанеры толщиной 1,2 см.
С увеличением ширины щитов увеличивается несущая способность опалубки, масса опалубки снижается в среднем на 10% с увеличением ширины щита от 0,3 до 0,6 м. Несущая способность и жесткость деревянной опалубки увеличиваются при росте отношения высоты бруса к ширине, при этом масса опалубки в среднем снижается на 30%. при изменении этого соотношения от 2 до 5.
Из конструктивных соображений отношение высоты бруса к ширине в дальнейшем принято равным 2.
Использование деревянной опалубки при пролетах до 3 м без установки тяжей оказалось нецелесообразным. Масса опалубки (табл. 8) составляла от 103 до 155 кг/м2 при числе схваток по высоте соответственно от 7 до 3 шт. (шаг установки от 0,5 до 1,5 м). При этом сечение деревянных брусьев при трех схватках составляет 38X38 см, при семи — 15,5X31 см, масса трехметровых схваток составляет соответственно 260 и 86 кг. В этом случае необходимо применение горизонтальных ферм шпренгельного типа или металлических схваток.
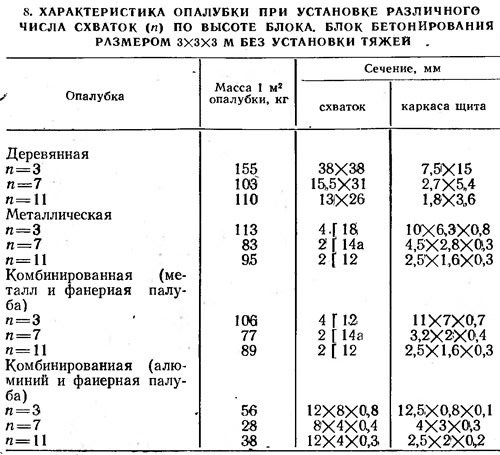
'Как видно из табл. 8 и 9, оптимальным для всех вариантов опалубки является установка по высоте блока семи схваток с шагом 0,15 м. Как меньшее, так и большее число схваток приводит к увеличению массы опалубки (при использовании оптимальных профилей для каждой схемы). Использование фанеры толщиной 12 мм в качестве палубы щита позволяет снизить массу опалубки в среднем на 6—10%.
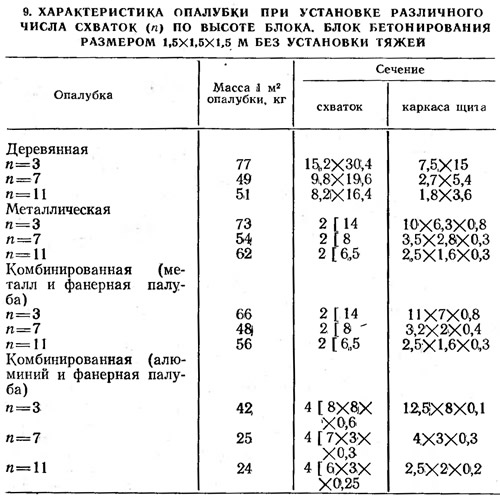
Расчеты показывают, что изменение шага схваток при уменьшении сечения блока бетонирования менее целесообразно, чем использование опалубок облегченных конструкций.
Установка промежуточных тяжей позволяет значительно (на 20—25%) снизить массу опалубки. Схема установки тяжей варьировалась как по высоте, так и по длине блока опалубки (через 0,5 м).
Расчеты показывают, что наибольший эффект дает равномерная установка тяжей по длине (через 1 м), причем первые тяжи должны устанавливаться на расстоянии 1 м от краев (углового закрепления) блока бетонирования и 0,5 м от низа опалубки через 1 м по высоте. Такая установка позволяет на 10%. снизить массу опалубки по сравнению с установкой тяжей на расстоянии 0,5 м от краев с расстоянием между, ними 2 м.
Просчитывалась также оптимальная установка несущих элементов опалубки при бетонировании протяженных стен высотой 3 м. Варьировался шаг установки тяжей и схваток. Металлические щиты приняты каркасной конструкции, каркас щитов выполнен из уголка, схватки — из двух швеллеров, тяжи принимались диаметром 12 мм.
Как показывают расчеты и эксперименты, снижение шага установки тяжей на 0,6 м или увеличение количества тяжей с 0,67 до 1,1 шт. на 1 м2 позволяет снизить массу опалубки на 20...25%.
Замена тяжей (диаметр 12 мм) жесткими опорами позволяет при том же расходе материалов уменьшить прогибы опалубки в среднем на 6%, моменты при этом уменьшаются всего на 2%.
Соображения, приведенные выше, по рациональному расположению тяжей, а также по размещению несущих элементов применимы и для других типов опалубки, в том числе крупноразмерных, при бетонировании стен и других конструкций с вертикальными поверхностями.
Поддерживающие элементы опалубки горизонтальных и наклонных поверхностей должны устанавливаться на надежных основаниях и иметь достаточную площадь опоры.
Телескопические стойки закрепляются горизонтальными и диагональными связями. 'Прогоны устанавливают по оголовникам, закрепленным на верху стоек.
При опалубливании плоских плит перекрытия по прогонам монтируют раздвижные ригели.
Для устройства опалубки балок на оголовниках телескопических стоек или на ригелях закрепляют балочные струбцины (рис. 13). После установки щитов днища балок устанавливают боковые щиты, а между ними — временные распорки или струбцины (по верху щитов). Установка струбцин для восприятия давления бетонной смеси целесообразна при значительной высоте балок. Боковые щиты целесообразно устанавливать на прогоны или струбцины, а не на щиты днища, чтобы предотвратить вытекание цементного молока даже при незначительных прогибах горизонтальных щитов! После установки щитов их закрепляют кронштейнами балочных струбцин. Между щитами плоской плиты перекрытия и боковыми щитами балок устанавливают легко извлекаемые прокладки. Демонтаж опалубки начинается с опускания всей системы при последовательном вращении винтовых домкратов.
При демонтаже опалубки балок ослабляют крепление балочных струбцин и отрывают от бетона боковые щиты. После этого последовательным вращением домкратов телескопических стоек на 10—15 см опускают опалубку балок, снимают боковые щиты и щиты днища. При опирании на боковые щиты опалубки плоских плит перекрытия демонтаж начинают с нее.
Демонтаж опалубки плоских перекрытий начинают со среднего ригеля, который выводят из опорных гнезд и снимают. При этом щиты обоими концами должны опираться на недемонтированные ригели. После ослабления (но не снятия) этих ригелей щиты осторожно снимают и выводят из-под них. Щиты, с которых начинается демонтаж, должны устанавливаться с зазором по отношению к соседним. Зазор между ними заделывают паклей, резиновым жгутом или закрывают сверху листовым материалом.
Опускание стоек опалубки сводов, арок и большепролетных балок производят постепенно, начиная с центра конструкции, и ведут последовательно в направлении к периметру.
К недостаткам мелкощитовой опалубки следует отнести значительное количество стыковых соединений, что не позволяет часто получить высокое качество бетонных поверхностей. Значительное число монтажных соединений определяет значительно большие трудозатраты, чем у других видов опалубки, в частности крупнощитовой.
Примечания
1. Работа выполнялась докт. техн. наук А. В. Гемерлингом и канд. техн. наук Р. А. Дубровской.